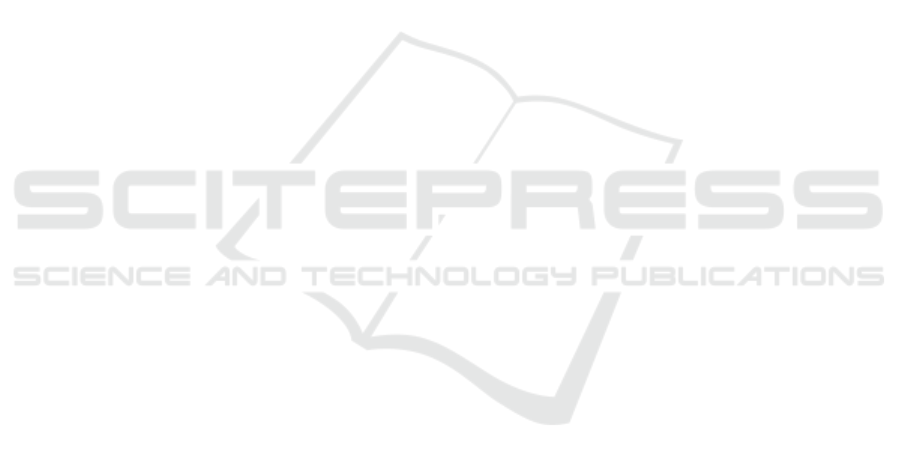
Robust Estimation of Load Performance of DC Motor using Genetic
Algorithm
Jong Kwang Lee, Byung Suk Park, Jonghui Han and Il-Je Cho
Nuclear Fuel Cycle Process Technology Development Division, Korea Atomic Energy Research Institute, Daejeon, Korea
Keywords: Load Performance, Multi-objective Optimization, Normalized Ratio of Errors.
Abstract: This paper presents a novel approach to estimate the load performance curves of DC motors whose
equations are represented as a function of the torque based on a steady-state model with constraints. Since a
simultaneous optimization of the curves forms a multi-objective optimization problem (MOP), we apply an
optimal curve fitting method based on a real-coded genetic algorithm (RGA). In the method, we introduce a
normalized ratio of errors to solve the MOP without the use of weighting factors and the nominal
parameters to automatically determine the searching bounds of the curve parameters. Compared to the
conventional least square fitting methods, the proposed scheme provides robust and accurate estimation
characteristics even when fewer measurements with a small range of torque loading are taken and used for a
data fitting.
1 INTRODUCTION
DC motors are widely used in applications ranging
from toys to automobiles. To fulfil the increasing
demands for quality and safety assurances, various
electrical tests including a performance test, a
durability test, a vibration or noise test, etc. are
being performed (Soukup, 1989). Among these tests,
the load performance test plays an important role in
verifying an agreement on the design properties and
evaluating the load performance of the motors.
Accordingly, the results of the test should have a
high reliability and repeatability.
To obtain the load performance curves or
characteristic values of DC motors, two methods
have been performed. Firstly, the steady-state test
was recommended by IEEE Std 113-1985 (1985)
and it is widely used in the industrial fields.
Readings of the current, voltage, speed, torque, and
temperatures should be obtained for six load points
equally spaced from 0.25 to 1.5 times the rated load.
During the load increases and decreases, two sets of
readings are taken at the specified load points, and
then their average value is usually chosen as a final
result. The main advantage of this method is that the
results are more accurate when compared with other
methods based on estimation. However, this method
has a disadvantage in that the time to accomplish all
the test procedures is excessive, causing the motors
to heat up severely owing to the necessity of a wide
range of torque loadings. Therefore, it is
recommended that temperatures such as the ambient
temperature, armature temperature, and field coil
temperature, should be measured to compensate for
the heating effects in the data.
Secondly, Nakamura, Kurosawa, Kurebayashi
and Ueha (1991) proposed the transient response
method to estimate the torque-speed characteristics
and the torque-efficiency characteristics of an
ultrasonic motor. It was assumed that the step
response of the speed has first order characteristics.
Its main advantage is that the torque-based
characteristic curves can be obtained from the
transient response of the speed without any
measurements of the torque. Therefore, all the
procedures can be accomplished within the transient
time of the motor, which can avoid the effects
arising from the temperature changes. In their
experiments, however, the maximum estimation
error was about 10%, which may prevent an accurate
estimation of the characteristic values.
Our research was motivated by the desire to find
a scheme that is faster than the steady-state test and
more accurate than the transient response test. To
accomplish the objectives, a new curve fitting
method based on a real-coded genetic algorithm
110
Lee J., Park B., Han J. and Cho I..
Robust Estimation of Load Performance of DC Motor using Genetic Algorithm.
DOI: 10.5220/0005008301100116
In Proceedings of the 4th International Conference on Simulation and Modeling Methodologies, Technologies and Applications (SIMULTECH-2014),
pages 110-116
ISBN: 978-989-758-038-3
Copyright
c
2014 SCITEPRESS (Science and Technology Publications, Lda.)