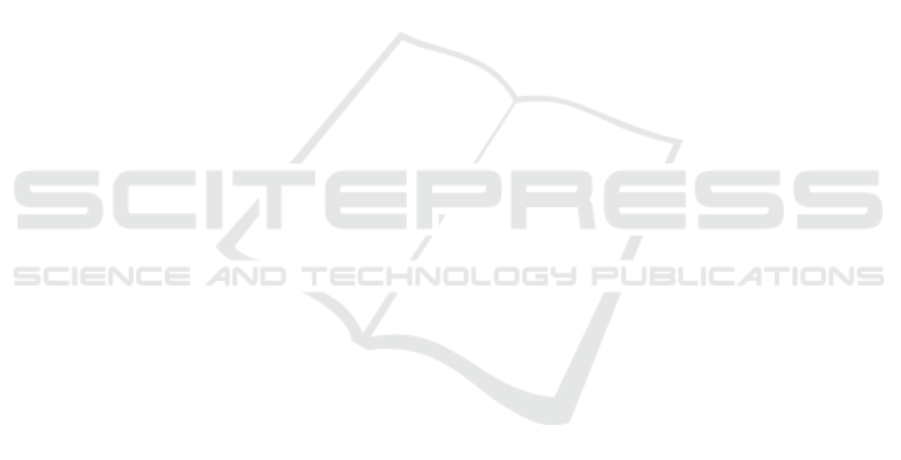
Parallel Robotic Manipulation via Pneumatic Artificial Muscles
Dimitris Gryparis, George Andrikopoulos and Stamatis Manesis
Department of Electrical and Computer Engineering, University of patras, Eratosthenous str., Rio, Greece
Keywords: Pneumatic Artificial Muscles, Parallel Manipulator, PID Control.
Abstract: In this article, a 6 Degree-of-Freedom (DOF) parallel manipulator, actuated by Pneumatic Artificial Muscles
(PAMs), is being presented. Incorporated in a two Stewart Platform-based design, the novel manipulator’s
motion capabilities are being examined through kinematic analysis, while the open-loop operation
characteristics and performance of the manipulator’s control via a multiple PID-based scheme are being
experimentally evaluated.
1 INTRODUCTION
Over the last decade, there has been an increasing
scientific interest in robotic manipulators that are
lightweight, safe and compliant (Calabria et al.,
2012; Radojicic & Surdilovic, 2009; Denkena et al.,
2008). In such cases, the selection of the type of
actuation that will power the manipulator is of
utmost importance. The Pneumatic Artificial Muscle
(PAM) has drawn the attention of the scientific
community regarding its merits for utilization in
biorobotic, medical and industrial applications
(Andrikopoulos, Nikolakopoulos & Manesis, 2011).
By mimicking the operation and properties of the
organic muscle, the PAM provides a suitable
solution for safer user interaction, as well as more
strong and natural motion through inherent
compliance, absence of mechanical parts, as well as
an impressive power-to-mass ratio. The most
utilized PAM-type is the McKibben Artificial
Muscle which was invented by the physician Joseph
L. Mckibben in the 1950s and was incorporated in
artificial limps (Stewart, 1965).
So far, similar PAM-actuated manipulator
approaches have included one Degree-of-Freedom
(DOF) per platform concepts (Calabria et al., 2012),
Stewart-based platforms via the utilization of 3
PAMs conically incorporated (Radojicic &
Surdilovic, 2009) and via more complex pneumatic
actuation mechanics (Denkena et al., 2008).
Parallel manipulator aproaches with the
utilization of other actuation means have included 3-
DOF parallel manipulators actuated by servomotors
(Cazalilla et al., 2014), (Khosravi et al., 2014),
(Ning et al., 2006) and 6-DOF Stewart-based
platforms actuated via hydraulic actuators placed at
the base of the robots (Guo, et al., 2007), (Pi et al.,
2010).
This article presents the development and control
of a parallel manipulator with 6 DOFs, which was
implemented in a two Stewart Platform-based
design. In this novel approach, each platform
consists of four PAM actuators in parallel
configuration, which are being operated as
antagonistic pairs, while a pneumatic cylinder is
being incorporated in the center of each platform,
thus, achieving 3 DOFs per moving platform.
The presented manipulator possesses the
advantage of incorporating more DOFs than the
manipulators found in related literature, thus
possessing enhanced motion capabilities, improved
motion range and increased relative workspace. In
addition, the cascaded configuration of the two
platforms is enhanced by the placement of all the
PAMs on the lower segment of the manipulator in
order to provide a novel mechanical approach on the
actuated motion of this parallel robotic structure.
The PAM-actuated manipulator is being depicted in
Figure 1.
In the following sections, the experimental setup
components and the kinematic analysis of the
manipulator’s structure are being presented, followed
by a presentation of the open-loop operation
characteristics of the manipulator. Finally, the
performance of the setup’s control via a multiple
PID-based scheme is being experimentally evaluated.
29
Gryparis D., Andrikopoulos G. and Manesis S..
Parallel Robotic Manipulation via Pneumatic Artificial Muscles.
DOI: 10.5220/0005008700290036
In Proceedings of the 11th International Conference on Informatics in Control, Automation and Robotics (ICINCO-2014), pages 29-36
ISBN: 978-989-758-040-6
Copyright
c
2014 SCITEPRESS (Science and Technology Publications, Lda.)