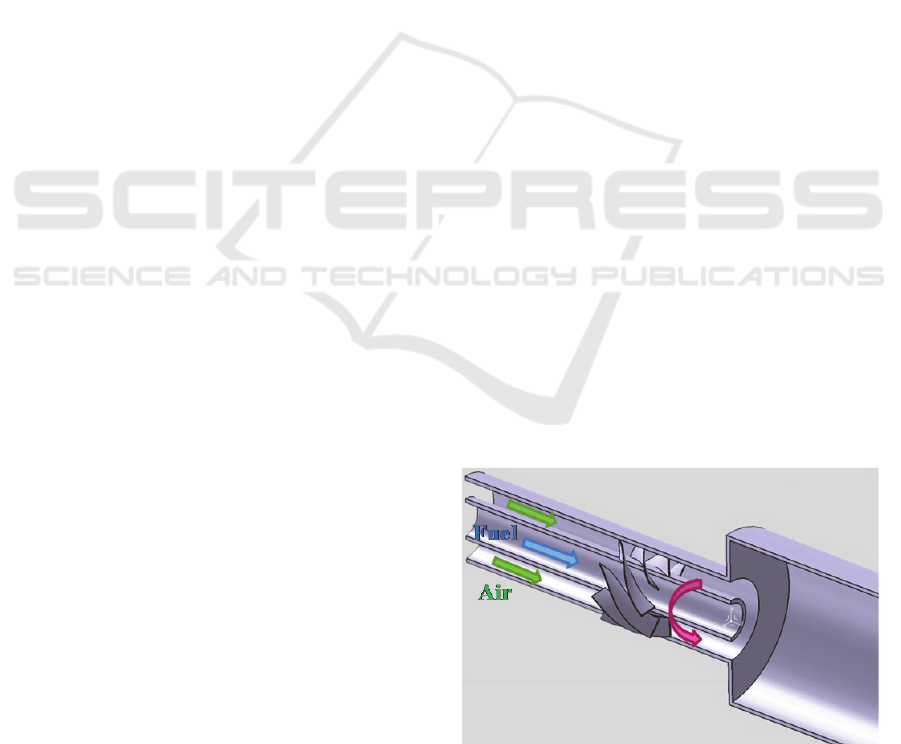
Mixing and Combustion of Turbulent Coaxial Jets
An Application of Computational Fluid Dynamics to Swirling Flows
Teresa Parra
1
, Ruben Perez
1
, Miguel A. Rodriguez
1
, Artur Gutkowski
2
, Robert Szasz
3
and Francisco Castro
1
1
Department of Energy and Fluid Mechanics, University of Valladolid, Paseo del Cauce 59, 47011 Valladolid, Spain
2
Department of Heat Technology and Refrigeration, Technical University of Lodz, Lodz, Poland
3
Energy Division, Lund University, Lund, Sweden
Keywords: CFD, Swirl Number, Recirculation Zones, Burner.
Abstract: The aim of this research is gaining an insight into flow patterns in swirling burners. These are suitable for
lean mixtures, because of procuring the fix position of the flame. The interaction of the two reactive
confined swirling jets leads to the formation of complex patterns which are not well understood. In the
present study, these flow patterns are numerically investigated using Reynolds Averaging Navier-Stokes
(RANS) equations for the flow and a Probability Density Function is used for modelling the combustion.
Two swirl numbers were characterised: 0.14 and 0.74. Strong swirling annular jets are responsible of an
inner recirculation zone. Low swirling flows produce poorer mixture and wide flame fronts whereas strong
swirling flows are precursors of mixing enhancement and thing flame fronts.
1 INTRODUCTION
The paper is focused on studying the flow pattern of
the flame for low and high swirl number. Swirling
flows let burn lean mixtures near the flammability
limits and produce low emissions.
The simplest burners are based on the interaction
of two confined coaxial jets. Annular jet goes
through a swirler that gives azimuthal component to
the flow. The exit of the two coaxial nozzles to the
chamber with an expansion ratio of four in area
produces the separation of the annular boundary
layer. The swirling annular jet is responsible for the
radial pressure gradient. For swirl numbers over 0.6,
there is reverse flow in the centre of the chamber.
The benchmark of Roback and Johnson (Roback,
1983) is the set up chosen to study the influence of
the swirler. This burner has two coaxial nozzles that
discharge into a test chamber. Figure 1 shows and
scheme of the burner and table 1 presents a summary
of the main dimensions and operation conditions of
this test case.
The swirler is a certain number of fixed vanes
located in the annular nozzle. The change of the
trailing edge angle modifies the Swirl number of the
annular jet. This paper is devoted to study the flow
pattern of the flame for low and high swirl numbers.
Figure 1: Scheme of the Roback-Johnson swirling burner.
The definition of Swirl number is the ratio of
azimuthal momentum and axial momentum. The
clear classification of low and high swirl numbers is
related to the flow pattern.
Low-swirl injector (S < 0.6) produces in the test
chamber a Central Divergence Zone (CDZ), a Shear
Layer (SL) and an Outer Recirculation Zone (ORZ).
Whereas high-swirl injectors are precursors of an
Inner Recirculation Zone (IRZ), a Shear Layer (SL)
545
Parra T., Perez R., Rodriguez M., Gutkowski A., Szasz R. and Castro F..
Mixing and Combustion of Turbulent Coaxial Jets - An Application of Computational Fluid Dynamics to Swirling Flows.
DOI: 10.5220/0005009005450550
In Proceedings of the 4th International Conference on Simulation and Modeling Methodologies, Technologies and Applications (SIMULTECH-2014),
pages 545-550
ISBN: 978-989-758-038-3
Copyright
c
2014 SCITEPRESS (Science and Technology Publications, Lda.)