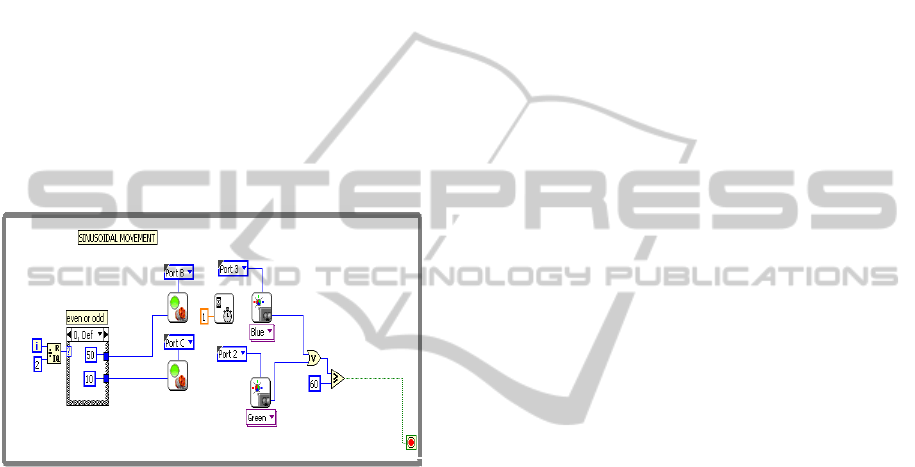
In order to cover 180˚ in the direction of motion it
was chosen to use a scanning approach such that, as
the robot travels in a straight line, the sensors cover
the area surrounding it.
The speed of the robot is 0.3 m/s at 100%
voltage input. The voltage can be modified in the
range from 0% to 200% to change speeds. The
sampling rate for the sensors is 10 times a second. A
sine wave, of given amplitude, had to be selected to
optimize the distance traveled, area scanned and
time elapsed to complete one cycle (Fig. 3).
The distance covered by the robot is directly
proportional to the amplitude of the sine curve path
chosen by the programmer. In a sine curve with
amplitude of 1, the length of a sine curve is 2.63π.
Depending on the requirements, the amplitude and
frequency can be chosen by the programmer. If there
is a need to scan a wider area, the amplitude can be
changed to a different value.
Figure 3: LabVIEW Virtual Instrument (VI) for sinusoidal
movement of the robot ending as a given high level of
light intensity is reached.
5 VOTING LOGIC APPROACH
5.1 Confidence Level
Confidence level is defined as the degree of
matching of the input signal to the features of an
ideal target, signal to interference ratio or number of
predefined features that are matched to the sensor
reading with the input signal. Here A
1
is denoted as
low confidence, A
2
and A
3
are denoted as medium
and high confidence levels for the sensor A,
respectively.
The number of confidence levels required for a
sensor is function of the number of sensors in the
system and the ease with which it is possible to
correlate target recognition features, extracted from
the sensor data, with distinct confidence levels. If
more confidence levels are available, the easier it is
to develop combinations of detection modes that
meet system detection and false-alarm probability
requirements under wide-ranging operating
conditions.
5.2 Voting Logic Sensor Fusion
As evident from the name, voting logic fusion fuses
the data of multiple sensors and based on the
information and confidence levels of these inputs
from the sensors, decision making is carried out
(Fig. 4). Voting logic fusion has many advantages
over single sensor based readings, used in series or
parallel. It provides a great deterrence against false
alarms, not compromising on the ability to detect
suppressed targets in a noisy environment. It may be
preferable technique to detect, classify and track
objects when multiple sensors are used.
Since one sensor, the ultrasonic sensor, is mainly
used for detection and avoidance of obstacles, it
does not need to be part of voting logic to declare
the presence of a fire (Fig. 5).Rather it would work
independently of the other sensors (Fig. 4). The
priority level for the sensor output is very high. As
the obstacle avoidance is very important to keep the
robot moving, the increasing gradient direction is
used for this purpose.
5.3 Modified Voting Logic
A fire declaration is only possible in the current
circumstances when the light readings above
threshold and the temperature above a certain level
are available. The probability of fire diminishes if
the light sensors are providing a reading that is
higher but the robot does not detect elevated
temperatures (Fig. 6). The robot may reach close to
the target where, due to robot geometry, the light
sensors may not give a reading that falls in any
confidence level given that the robot reached the
source. At that instance, the sensor A will give the
highest confidence level due to the temperature
present but, since the other sensors are not able to
sense it, voting logic will not declare a target based
on the output of just one sensor. At this point the
reading from the other sensors becomes irrelevant.
Normal voting logic does not keep this scenario
into account. In order to reach the point of interest
the robot has to follow any lead of increased light
only and will not declare the fire source until it
reaches a point where elevated temperatures are also
detected. To maximize the possibility of identifying
the target, an average of the previous four readings
is taken into account to linearize the readings hence
ICINCO2014-11thInternationalConferenceonInformaticsinControl,AutomationandRobotics
142