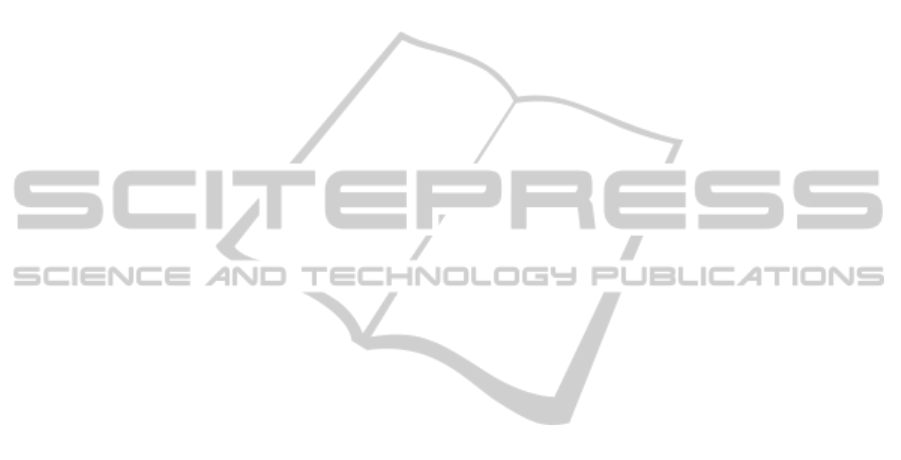
of Communications in Computer and Information Sci-
ence, pages 23–37. Springer Berlin Heidelberg.
B
¨
ucker, M., Krewet, C., Schyja, A., and Kuhlenk
¨
otter, B.
(2011). Autonome Roboter mit sensorbasierter Bahn-
planung. Industrie Management, 1:21–24.
Denavit, J. and Hartenberg, R. S. (1955). A kinematic no-
tation for lower-pair mechanisms based on matrices.
Transactions of the ASME. Journal of Applied Me-
chanics, 22:215–221.
Diankov, R. (2010). Automated Construction of Robotic
Manipulation Programs. PhD thesis, Carnegie Mellon
University, Robotics Institute.
Drumwright, E., Hsu, J., Koenig, N., and Shell, D. (2010).
Extending open dynamics engine for robotics simu-
lation. In Proceedings of the Second International
Conference on Simulation, Modeling, and Program-
ming for Autonomous robots, SIMPAR’10, pages 38–
50, Berlin, Heidelberg. Springer-Verlag.
Francois, C., Hebert, M., and Ikeuchi, K. (1991). A three-
finger gripper for manipulation in unstructured en-
vironments. In IEEE International Conference on
Robotics and Automation.
Ghita, O. and Whelan, P. F. (2003). A bin picking system
based on depth from defocus. Machine Vision and
Applications, 13(4):234–244.
Ghita, O. and Whelan, P. F. (2008). A systems engineering
approach to robotic bin picking. In Bhatti, A., editor,
Stereo Vision, chapter 4, pages 59–72. InTech.
Gottschalk, S., Lin, M. C., and Manocha, D. (1996). OBB-
Tree: A Hierarchical Structure for Rapid Interference
Detection. In Proceedings of the 23rd annual con-
ference on Computer graphics and interactive tech-
niques, SIGGRAPH ’96, pages 171–180, New York,
NY, USA. ACM.
Johnson, M. (2013). Flexible Path Planning For Bin-
Picking Applications. Masterarbeit, Technische Uni-
versitt Dortmund.
Kirkegaard, J. and Moeslund, T. B. (2006). Bin-picking
based on harmonic shape contexts and graph-based
matching. In 18th International Conference on Pat-
tern Recognition, volume 2 of ICPR, pages 581–584.
Kneupner, K. (2004). Entwicklung eines Programmier- und
Steuerungskonzepts f
¨
ur Robotersysteme auf der Basis
eines Umweltmodells. PhD thesis, TU Dortmund Uni-
versity. ISBN 3-18-338920-7 VDI Verlag, D
¨
usseldorf.
Kuhlenk
¨
otter, B., Hypki, A., Schyja, A., and Miegel, V.
(2010). Robot Workcell Simulation with Automa-
tionML Support - An Element of the CAx-Tool Chain
in Industrial Automation. In Proceedings for the joint
conference of ISR 2010 (41st International Sympo-
sium on Robotics) und ROBOTIK 2010 (6th German
Conference on Robotics). VDE Verlag GmbH.
Leonard, S., Chan, A., Little, J. J., and Croft, E. A.
(2007). Robust motion generation for vision-guided
robot bin-picking. ASME Conference Proceedings,
2007(43033):651–658.
Martinez, A. and Fernndez, E. (2013). Learning ROS for
Robotics Programming. Packt Publishing.
McKee, J. W. and Aggarwal, J. K. (1977). Computer recog-
nition of partial views of curved objects. IEEE Trans-
actions on Computers, 26(8):790–800.
Palzkill, M., Ledermann, T., and Verl, A. (2010).
Anticipation-preprocessing for object pose detection.
In 41st International Symposium on Robotics, ISR
2010, pages 440–445.
Pochyly, A., Kubela, T., Singule, V., and Cihak, P. (2012).
3d vision systems for industrial bin-picking applica-
tions. In 15th International Conference on Mecha-
tronics, MECHATRONIKA, pages 1–6. IEEE.
Project Group 510 (2008). Entwicklung einer echtzeitfhi-
gen Kollisionsbehandlung fr die physikalische Simu-
lation in virtuellen Umgebungen. Project Group, TU
Dortmund University, Computer Science VII.
RRS-Owners (1991). Realistic Robot Simulation Inter-
face Specification, version 1.3. Technical report,
Fraunhofer-Institut f
¨
ur Produktionsanlagen und Kon-
struktionstechnik (IPK), Berlin.
Schraft, R. D. and Ledermann, T. (2003). Intelligent picking
of chaotically stored objects. Assembly Automation,
23(1):38–42.
Schyja, A., Bartelt, M., and Kuhlenk
¨
otter, B. (2014). From
conception phase up to virtual verification using auto-
mationml. In 5th CATS 2014 – CIRP Conference on
Assembly Systems and Technologies. Status: accepted.
Schyja, A., Hypki, A., and Kuhlenk
¨
otter, B. (2012). A
modular and extensible framework for real and vir-
tual bin-picking environments. In 2012 IEEE In-
ternational Conference on Robotics and Automation
(ICRA), pages 5246 –5251.
Tsuboi, Y. and Inoue, T. (1976). Robot assembly system
using tv camera. Industrial Robot: An International
Journal, 3(2):67–72.
Wurdemann, H. A., Aminzadeh, V., Cui, L., and Dai, J. S.
(2011). Feature extraction of non-uniform food prod-
ucts using rgb and rgb-d data combined with shape
models. In International Conference on Robotics and
Biomimetics, ROBIO, pages 1652–1657. IEEE.
SIMULTECH2014-4thInternationalConferenceonSimulationandModelingMethodologies,Technologiesand
Applications
140