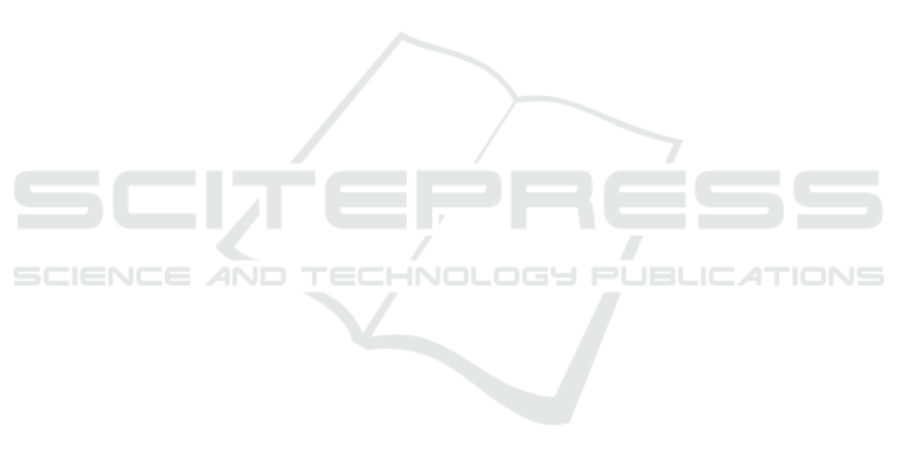
Digital Self-tuning Control for Pressure Process
Gediminas Liaucius and Vytautas Kaminskas
Department of Systems Analysis, Vytautas Magnus University, Vileikos Str. 8, LT-44404 Kaunas, Lithuania
Keywords: Self-tuning PID Control, Closed-loop Parameters and Sampling Period Optimization, Predictor-based Self-
tuning Control with Constraints, Pressure Process.
Abstract: Two digital control systems - Self-tuning PID (Proportional-Integral-Derivative) Control and Predictor-
based self-tuning control with constraints - for the continuous-time pressure process control are presented in
this paper. The digital self-tuning PID control with optimization of closed-loop parameters and sampling
period is proposed. The multidimensional optimization problem of closed-loop parameters and sampling
period is solved by subcomponent search method that enables dividing the problem to one-dimensional
optimization problems. The golden section search is adjusted to solve those – one-dimensional -
optimization problems. The predictor-based self-tuning control with constraints is adapted for both
minimum-phase and nonminimum-phase process models. The control quality of pressure process of both
control systems has been experimentally investigated. The results of experimental analysis demonstrate that
the digital self-tuning PID control with optimization is more efficient as compared to predictive-based self-
tuning control with constraints for pressure process.
1 INTRODUCTION
At present, various physical nature processes are still
continuous-time processes, but are frequently
controlled by digital controllers (Isermann, 1991;
Åström and Wittenmark, 1997; Bobál, et al, 2005).
The digital PID (proportional-integral-derivative)
control laws are the most common for such
processes (Åström and Hagglund, 1995; 2001;
Levine 1999). The PID controllers are so widely
used for its easiness to apply and generally provides
sufficient control quality if it is properly tuned.
For the digital PID control based on digital self-
tuning PID controllers the selection of suitable
closed-loop parameters (Vu, et al, 2007; Kosorus,
et al, 2012) and proper sampling period (Boucher,
et al, 1989; Isermann, 1991; Åström and
Wittenmark, 1997; Levine, 2011) is substantial since
directly influences the control quality of the process.
Furthermore, the determination of closed-loop
parameters and sampling period is not
straightforward, at the design stage of the control.
The digital self-tuning PID control system with
on-line identification and optimization of closed-
loop parameters and sampling period is developed
for pressure process control (Liaucius, et al, 2011;
Liaucius and Kaminskas, 2012a) in this paper.
As an alternative to self-tuning PID control for
pressure process, the predictor-based self-tuning
control with constraints (Kaminskas, 2007) is
analysed. This control method has been modified for
both minimum-phase and nonminimum-phase
process models. The results of experimental analysis
of both control approaches are presented.
2 THE PRESSURE PROCESS
The scheme of pressure process is depicted in
Figure 1.
The process consists of four main components:
combined air inlet and outlet tanks, two air chambers
and two tubes with balls in them. The air from the
inlet tank flows to air channels through air chambers
and leaves the equipment through the upper outlet
tank. The distance to balls is measured using
ultrasound distance sensors. The fans are used to
create pressure in the air channels in order to lift the
balls in tubes. The air chambers are utilized for the
purpose to stabilize oscillations of the pressure in
each tube. The momentum of the fan, the inductance
of the fan motor, air turbulence in the tube leads to
complex physics governing ball behaviour. Slightly
different weights of the balls and the location of the
612
Liaucius G. and Kaminskas V..
Digital Self-tuning Control for Pressure Process.
DOI: 10.5220/0005012106120619
In Proceedings of the 11th International Conference on Informatics in Control, Automation and Robotics (ICINCO-2014), pages 612-619
ISBN: 978-989-758-039-0
Copyright
c
2014 SCITEPRESS (Science and Technology Publications, Lda.)