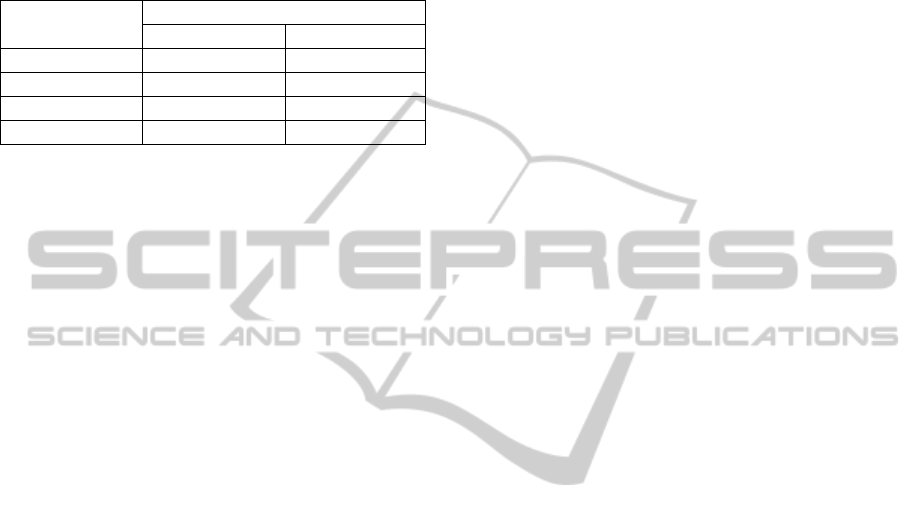
and high stability. In both of the cases the errors
reached are small and the difference between them is
slight. The main cause of such difference is the
higher resolution and computational resources of
Simulink.
Table 2: Steady-state error comparison.
Vsetpoint
Steady-state error (%)
Simulink PLC
4 -3.5 -1.7
5 4.2 6.2
5.5 4.7 4.7
6 -1.1 2.8
On the view of these results we can conclude
two facts. On the one hand, it has been demonstrated
the ability of the developed controller to adjust the
servomotor speed to the required set point. On the
other hand, these data validate the module developed
to implement fuzzy controllers in the PLC s7-1200.
6 CONCLUSIONS
A software module to implement fuzzy controllers in
a Siemens PLC s7-1200 has been presented. A
servomotor has been used as test platform to validate
the developed PLC-Fuzzy Controller.
The results under real operating conditions
constitute a proof-of-concept of the feasibility of the
proposed system.
A positive feature of the developed work is the
utilization of a PLC of recent market release and,
hence, progressive introduction in industrial plants
and research teams. This device belongs to Siemens
low-end performance range, providing automation
solutions with minor costs.
This work has contributed to a better
understanding of the abilities and procedures to
implement fuzzy controllers in PLC.
Future works focus on the application of the
controller to more complex systems such as a
hydrogen generator integrated in a hybrid renewable
energy system. Also, its integration with software
applications using OPC protocol and the
programming of more options such as fuzzy PID
structure are under study.
ACKNOWLEDGEMENTS
Authors are grateful to the University of
Extremadura and to the Gobierno de Extremadura
for their financial support by grant GR10157 and
FEDER (Fondo Europeo de Desarrollo Regional:
Una Manera de Hacer Europa).
REFERENCES
Aydogmus, Z., 2009. Implementation of a fuzzy-based
level control using SCADA. Expert Systems with
Applications, vol. 36, pp. 6593-6597.
Bogdan, S., Kovacic, Z., Krapinec, D., 2007. Sensitivity-
based self-learning fuzzy logic controller as a PLC
super block. 15th IEEE Mediterranean Conference on
Control and Automation, Athens, Greece.
Bosque, G., del Campo, I., Echanobe, J., 2014. Fuzzy
systems, neural networks and neuro-fuzzy systems: A
vision on their hardware implementation and platforms
over two decades. Engineering Applications of
Artificial Intelligence, vol. 32, pp. 283-331.
Cingolani, P., Alcalá, J., 2012. jFuzzyLogic: a robust and
flexible fuzzy-logic inference system language
implementation. IEEE World Congress on
Computational Intelligence, Brisbane, Australia.
Joelianto, E., Anura, D. C., Priyanto, M., 2013. ANFIS –
hybrid reference control for improving transient
response of controlled systems using PID controller.
International Journal of Artificial Intelligence, vol. 10,
pp. 88-111.
Karasakal, O., Yesil, E., Guzelkaya, M., Eksin, I., 2005.
Implementation of a new self-tuning fuzzy PID
controller on PLC. Turkish Journal of Electrical
Engineering & Computer Sciences 13, no. 2, 277-286.
Li, H. X., Tso, S. K., 1999. A fuzzy PLC with gain-
scheduling control resolution for a thermal process – a
case study. Control Engineering Practice, vol. 7, pp.
523-529.
Piegat, A., 2001. Fuzzy Modeling and Control (Studies in
Fuzziness and Soft Computing Series). Physica Verlag,
A Springer Verlag Company, Heidelberg, Germany.
Ruan, D., Van der Wal, A.J., 1998. Controlling the power
output of a nuclear reactor with fuzzy logic.
Information Sciences, vol. 110, pp. 151-177.
Saad, N., Arrofiq, M., 2012. A PLC-based modified-fuzzy
controller for PW-driven induction motor drive with
constant V/Hz ratio control. Robotics and Computer-
Integrated Manufacturing, vol. 28, pp. 95-112.
Song, Y., Bi, Z., Liu, K., 2007. The PLC system of egg
powder treatment based on fuzzy control algorithm.
4th IEEE International Conference on Fuzzy Systems
and Knowledge Discovery, Haikou, China.
Zhang, H., Liu, D., 2006. Fuzzy Modeling and Fuzzy
Control (Control Engineering). Birkhäuser, Boston.
FuzzyControllerbasedonPLCS7-1200-ApplicationtoaServomotor
163