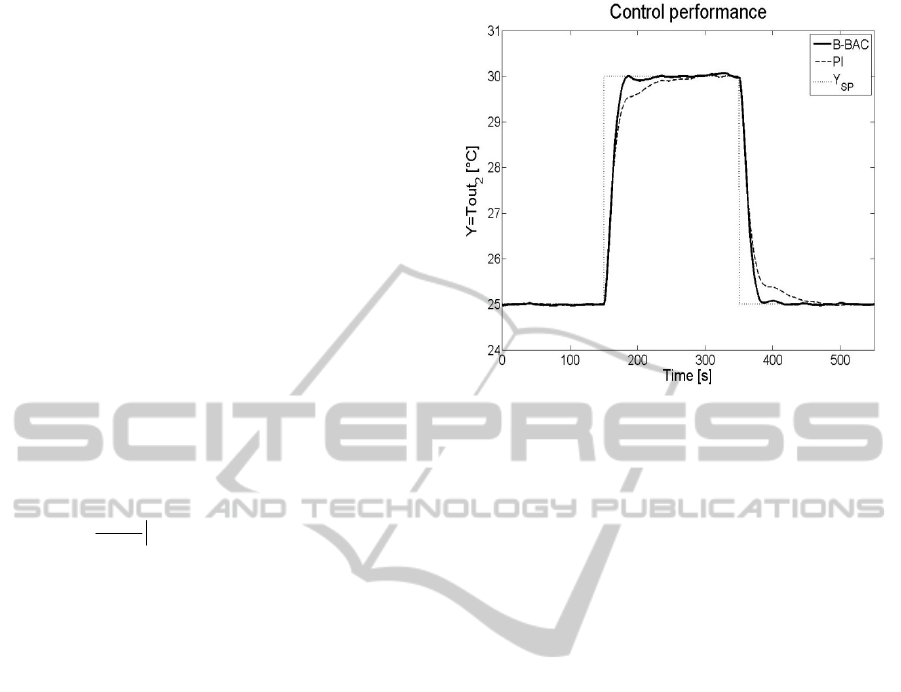
the set point for the heating system with the inner
control loop that ensures possibly high tracking
properties. Thus, this actuating system has its own
dynamics that can deteriorate the performance of the
suggested PHE control system. During simulation
experiments, this dynamics was simulated by the
additional first-order lag system with unitary gain
and time constant adjusted as T
H
= 6 [s]. Readers
should note that this dynamics is not included in the
model applied for the synthesis of the
B-BAController (11) and it can be considered as the
unknown substitute dynamics of the actuating
system.
It was also decided to make the simulation
results more realistic by adding the additive random
noise to the measurement data from the controlled
temperature T
out2
and for the measured disturbances
F
1
, F
2
and T
in2
. This noisy data was used for
computing the estimation procedure (9) - (10) and
the manipulated variable by the control law (11).
The same data was also applied to excite the OCM
model used for approximation of the space
derivative
tA
tY
z 0,20
)(
for both the
estimation and the B-BAController.
The control performance of the suggested
B-BAController (11) is compared with the
performance of the conventional PI controller that is
still in use in the vast majority of the industrial
control loops. The PI controller was tuned based on
the process step response. Then, its tunings were
recalculated into the tunings of the B-BAController
(11) (namely, into its gain
and the forgetting factor
for the estimation procedure α
f
) by the tuning
method suggested by Stebel et al. (2014). Finally,
both controllers were retuned manually to ensure
possibly the same aperiodic tracking properties.
Thus, it can be assumed that both controllers were
tuned equivalently with the tunings k
r
= 1.7,
T
I
= 19.8 [s] for the conventional PI controller and
= 0.12, α
f
= 0.9949 for the B-BAController (11).
This equivalence can be seen in Fig. 3 that shows the
tracking properties of both controllers in the
presence of the indicated step changes of the set
point Y
sp
.
For this equivalent tuning, the disturbances
rejection for both controllers was investigated. The
system with the B-BAController (11) provides the
feedforward action from the measurable
disturbances F
2
and T
in2
, which results from the
direct application of the distributed parameter model
of PHE for the synthesis of the control law. Thus,
the significantly better disturbances rejection can be
obtained for the B-BAController (11), in the
Figure 3: Tracking properties of the considered
controllers. Noisy case.
comparison with the equivalently tuned conventional
PI controller.
The control performance of both controllers can
be seen in Figs. 4 - 6, at the presence of the step
changes of the respective disturbing signals F
2
, T
in2
and F
1
applied to the system. Upper diagrams of
each figure show the variations of the controlled
variable Y = T
out2
, while the lower diagrams show
the accuracy of the approximation of the space
derivative A
2,0
at the outlet of the cold water and
required for computing the estimation procedure (9)-
(10) and the control law (11). The FDM model is
used to compute the real value of A
2,0
while its
approximation is computed from the OCM model.
Readers should note relatively high accuracy of the
space derivative approximation and the fact that
such comparison is possible only in simulation - in
the practice, the real value of A
2,0
is always
unknown.
Note that at each case, the B-BAController (11)
ensures significantly shorter settling time with
smaller overregulation, even in the presence of the
changes of the disturbing flow rate F
1
, whose
measurement data is not included in the
B-BAController (11). At the same time, the presence
of the measurement noise does not corrupt the
control performance of the B-BAController (11)
more significantly as it does in the case of the
conventional PI controller, which makes the
suggested approach an promising alternative in the
industrial practical systems for the control of PHE.
SIMULTECH2014-4thInternationalConferenceonSimulationandModelingMethodologies,Technologiesand
Applications
662