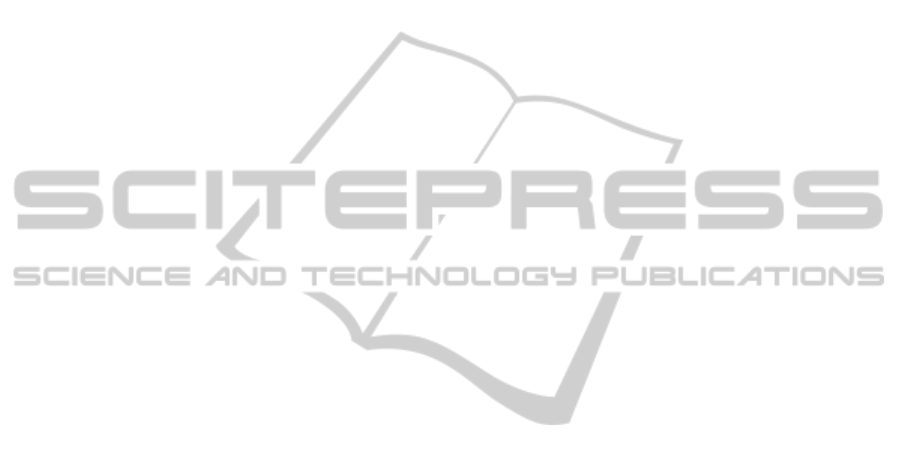
Abdellatif, H., Grotjahn, M., and Heimann, B. (2005, De-
cember). High efficient dynamics calculation ap-
proach for computed-force control of robots with par-
allel structures. In Decision and Control, 2005 and
2005 European Control Conference. CDC-ECC’05.
44th IEEE Conference on (pp. 2024-2029). IEEE.
Weck, M., Staimer, D. (2002). Parallel kinematic machine
toolscurrent state and future potentials. CIRP Annals-
Manufacturing Technology, 51(2), 671-683.
Jamwal, P. K., Xie, S. Q., Tsoi, Y. H., and Aw, K. C.
(2010). Forward kinematics modelling of a parallel
ankle rehabilitation robot using modified fuzzy infer-
ence. Mechanism and Machine Theory, 45(11), 1537-
1554.
Gough, V. E. (1956) Contribution to discussion of papers
on research in automobile stability, control and tyre
performance. In Proc. Auto Div. Inst. Mech. Eng (Vol.
171, pp. 392-394).
Stewart, D. (1965). A platform with six degrees of free-
dom. Proceedings of the institution of mechanical en-
gineers, 180(1), 371-386.
Vermeiren, L., Dequidt, A., Afroun, M., and Guerra, T. M.
(2012). Motion control of planar parallel robot using
the fuzzy descriptor system approach. ISA transac-
tions, 51(5), 596-608.
Cheung, J. W., Hung, Y. S. (2005, July) Modelling and con-
trol of a 2-DOF planar parallel manipulator for semi-
conductor packaging systems. In Advanced Intelligent
Mechatronics. Proceedings, 2005 IEEE/ASME Inter-
national Conference on (pp. 717-722). IEEE.
Pierrot, F., Krut, S., Baradat, C., and Nabat, V. (2011).
Par2: a spatial mechanism for fast planar two-degree-
of-freedom pick-and-place applications. Meccanica,
46(1), 239-248.
Khalil, W., Ibrahim, O. (2007). General solution for the
dynamic modeling of parallel robots. Journal of intel-
ligent and robotic systems, 49(1), 19-37.
Staicu, S., Liu, X. J., and Wang, J. (2007). Inverse dynamics
of the HALF parallel manipulator with revolute actu-
ators. Nonlinear Dynamics, 50(1-2), 1-12.
Staicu, S. (2009). Recursive modelling in dynamics of
Agile Wrist spherical parallel robot. Robotics and
Computer-Integrated Manufacturing, 25(2), 409-416.
Ghorbel, F. H., Chtelat, O., Gunawardana, R., and
Longchamp, R. (2000). Modeling and set point con-
trol of closed-chain mechanisms: theory and exper-
iment. Control Systems Technology, IEEE Transac-
tions on, 8(5), 801-815.
Ouyang, P. R., Zhang, W. J., and Wu, F. X. (2002).
Nonlinear PD control for trajectory tracking with
consideration of the design for control methodol-
ogy. In Robotics and Automation, 2002. Proceedings.
ICRA’02. IEEE International Conference on (Vol. 4,
pp. 4126-4131). IEEE.
Ouyang, P. R., Zhang, W. J., and Gupta, M. M. (2006). An
adaptive switching learning control method for trajec-
tory tracking of robot manipulators. Mechatronics,
16(1), 51-61.
Le, T. D., Kang, H. J., and Suh, Y. S. (2013). Chattering-
Free Neuro-Sliding Mode Control of 2-DOF Planar
Parallel Manipulators. Internation Journal of Ad-
vanced Robotic Systems (October 22, 2013).
Piltan, F., Rahmdel, S., Mehrara, S., and Bayat, R.
(2012). Sliding mode methodology vs. Computed
torque methodology using matlab/simulink and their
integration into graduate nonlinear control courses.
International Journal of Engineering, 6(3), 142-177.
Yang, Z., Wu, J., and Mei, J. (2007). Motor-mechanism
dynamic model based neural network optimized com-
puted torque control of a high speed parallel manipu-
lator. Mechatronics, 17(7), 381-390.
Zhu, X., Tao, G., Yao, B., and Cao, J. (2009) Integrated di-
rect/indirect adaptive robust posture trajectory track-
ing control of a parallel manipulator driven by pneu-
matic muscles. Control Systems Technology, IEEE
Transactions on, 17(3), 576-588.
Slotine, J. J. E., Li, W. (1991). Englewood Cliffs, NJ:
Prentice-Hall. Applied nonlinear control (Vol. 199,
No. 1).
Sadati, N., Ghadami, R. (2008). Adaptive multi-model slid-
ing mode control of robotic manipulators using soft
computing. Neurocomputing, 71(13), 2702-2710.
Zeinali, M., Notash, L. (2010). Adaptive sliding mode con-
trol with uncertainty estimator for robot manipulators.
Mechanism and Machine Theory, 45(1), 80-90.
Castaos, F., Fridman, L. (2006). Analysis and design of
integral sliding manifolds for systems with unmatched
perturbations. Automatic Control, IEEE Transactions
on, 51(5), 853-858.
AL-Samarraie, S. A. (2013). Invariant Sets in Sliding Mode
Control Theory with Application to Servo Actuator
System with Friction. WSEAS TRANSACTIONS on
SYSTEMS and CONTROL, 8(2), 33-45.
Utkin, V., Guldner, J., and Shijun, M. (1999). Sliding mode
control in electro-mechanical systems (Vol. 34). CRC
press.
Sankaranarayanan, V., Mahindrakar, A. D. (2009). Control
of a class of underactuated mechanical systems us-
ing sliding modes. Robotics, IEEE Transactions on,
25(2), 459-467.
Geravand, M., Aghakhani, N. (2010). Fuzzy sliding mode
control for applying to active vehicle suspentions.
Wseas Transactions on Systems and Control, 5(1), 48-
57.
Lin, F. J., Chen, S. Y., and Shyu, K. K. (2009). Robust dy-
namic sliding-mode control using adaptive RENN for
magnetic levitation system. Neural Networks, IEEE
Transactions on, 20(6), 938-951.
Lin, F. J., Chen, S. Y., and Shyu, K. K. (2009). General de-
sign issues of sliding-mode controllers in DCDC con-
verters. Industrial Electronics, IEEE Transactions on,
55(3), 1160-1174
Khiari, B., Sellami, A., Andoulsi, R., and Mami, A. (2012).
A Novel Strategy Control of Photovoltaic Solar Pump-
ing System Based on Sliding Mode Control. Interna-
tional Review of Automatic Control, 5(2)
SlidingModeControlofBiglidePlanarParallelManipulator
309