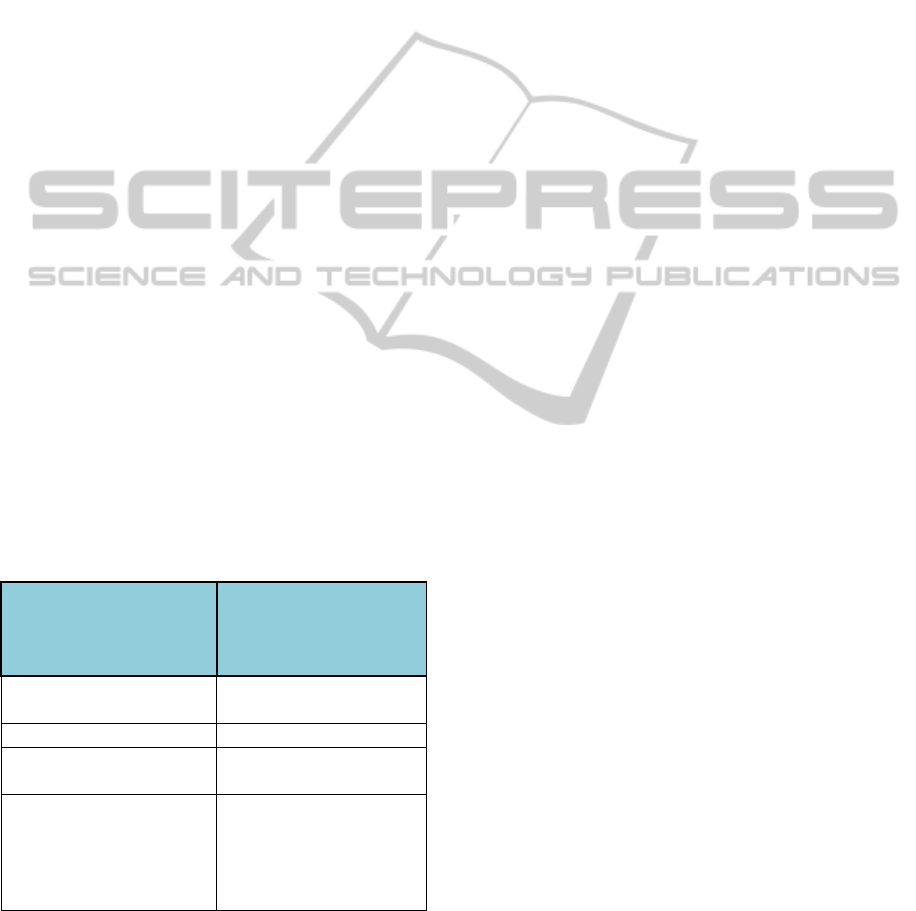
attract intensive attentions. A six-axes wrist
force/moment sensor was proposed by Kim applied
for an intelligent robot (Kim, 2007). Liang et al.
presented another type of six-dimensional wrist
force/torque for five-axes parallel machine tool
(Liang, 2010). In addition to optical torque sensors,
a six-axis capacitive-type force-torque sensor is
designed and realized to measure the power transfer
between the human body and the environment
(Brookhuis, 2014). Besides, a capacitor-type torque
sensor, capable to measure the full angular torque
range, is proposed to apply upon magnetic
anisotropies (Rigue, 2012). Unfortunately, the
aforesaid torque sensors are not applicable to rotary
shafts, particularly for high speed mode.
To count for the shortcomings of the torque
sensors discussed above, a contactless thin-layered
torque sensor with fully-digital signal processing
circuit is hence proposed in this work. The proposed
torque sensor possesses a lot of merits such as low
cost, free maintenance, thin thickness, light weight,
adaptive to be applied to high-speed rotors, and no
signal interference at all. Compared with the
traditional torque sensors, the advantages of the
proposed sensor are listed in Table 1.
This proposed digital torque sensor can be
employed for numerous applications such as
machine tools, robot arms, spindles of power tools,
washing machines and etc. Due to its merits of free
contact and noise, its measurement precision can be
retained all the time even under serious
contamination environments.
Table 1: Comparison between traditional and proposed
torque sensors.
Compared with
analog torque sensors
Compared with
rotary (brush
embedded) torque
sensor
Lower cost
Can operate in high
speed
No signal interference No brush wear
No need to compensate
temperature correction
No noise out of carbon
brush
Lower demand on the
performance
requirements of
associated photo
reflectors
Longer lifespan and
more reliability
2 DESIGN OF CONTACTLESS
THIN-LAYERED TORQUE
SENSOR
To design a torque sensor applied to robot arms with
high-speed shafts, it is expected to meet a few goals:
(i) thin along axial direction, (ii) able to operate
under high-speed rotation mode, (iii) able to real-
time measure the torque exerted on the shaft, with
no considerable time delay.
2.1 Thin and Flexible Mechanical
Structure
The profile and the parameters of proposed thin
orange-slice-alike flexible body are shown in Figure
1. The basic design concept of the mechanical
structure is to take advantage of elastic deformation
of the metal texture to reflect the exerted torque.
One outer ring and six palm anchors are combined to
construct the main part of the orange-slice-alike
flexible body. To enhance more sensitivity to the
exerted torque, the outer ring and the palm anchors
are radially connected by spokes so that the cross-
section of the mechanical structure therefore looks
like an orange slice. The parameters and dimensions
of the spokes can be obtained by consideration of the
overall volume of the torque sensor as small as
possible but its precision and resolution as high as
possible. Aside, a few screw holes are made on the
outer ring and palm anchors for connecting the
associated linkers and the orange-slice-alike flexible
body. If an external torque was applied to this
mechanical structure, the twelve spokes would be
twisted at the same time such that the deformations
of twelve spokes would together result in a relative
angular displacement between the outer ring and
palm anchors. Based on the assumption that the
torsional stiffness of the orange-slice-alike flexible
body is constant, the applied torque can be
quantified via the evaluation of this induced twisted
angle. Compared with the design of non-coplanar
flexible structure (Renaud, 2009), the sensitivity and
reliability of proposed orange-slice-alike flexible
body by authors is evidently much superior.
How to design the profile of the orange-slice-
alike flexible body directly affects the performance
of the resulted torque sensor, including the
achievable range of measurement, the rotational
speed span compatible with the torque sensor
equipped (operation bandwidth), resolution, linearity
and so on. Hence, firstly the mechanical design is
focused on: the orange-slice-alike flexible body can
ContactlessThin-LayeredTorqueSensorModulewithFully-digitalSignalProcessingCircuit
451