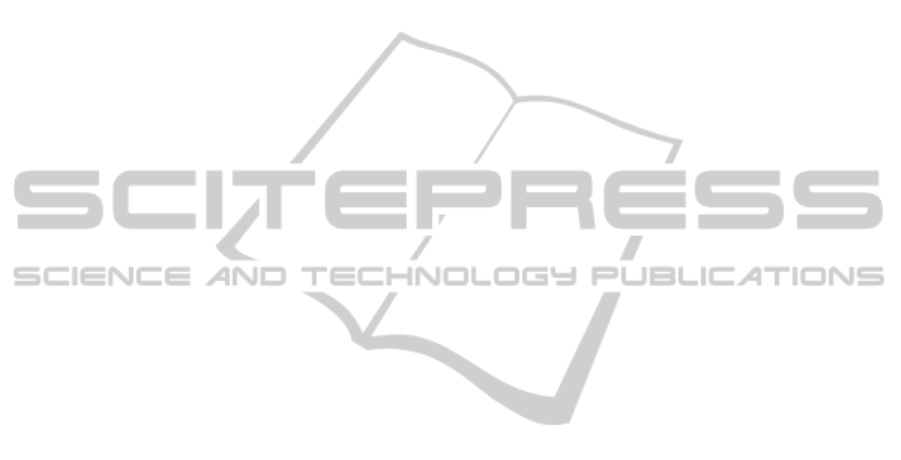
though computation is offline, exhaustive enumera-
tion of a large number of potential robot, sensor and
human positions combined with finite computational
resources demands further research into both the can-
didate function for single and multi-camera place-
ment, and an optimisation strategy that does not re-
quire such exhaustive enumeration. Promising ap-
proaches are genetic algorithms (Dunn et al., 2006)
or simulated annealing (Mittal and Davis, 2008) for
highly non-linear optimisation to reduce the number
of camera state vectors s to be evaluated. Fast opti-
misation strategies enable online robot path planning
for full human visibility and best collision avoidance
performance.
ACKNOWLEDGEMENTS
The authors would like to acknowledge the support
of the University of Applied Sciences, Ingolstadt
and the Engineering and Physical Research Council
(EP/J015180/1 Sensor Signal Processing).
REFERENCES
Amanatides, J. and Woo, A. (1987). A fast voxel traversal
algorithm for ray tracing. In Proceedings of EURO-
GRAPHICS.
Angerer, S., Strassmair, C., Staehr, M., Roettenbacher, M.,
and Robertson, N. (2012). Give me a hand. In Tech-
nologies for Practical Robot Applications (TePRA),
2012 IEEE International Conference on.
Bodor, R., Drenner, A., Schrater, P., and Papanikolopoulos,
N. (2007). Optimal camera placement for automated
surveillance tasks. Journal of Intelligent & Robotic
Systems.
Brogan, D. C. and Johnson, N. L. (2003). Realistic hu-
man walking paths. In Computer Animation and So-
cial Agents, 2003. 16th International Conference on.
Chen, X. and Davis, J. (2008). An occlusion metric for se-
lecting robust camera configurations. Machine Vision
and Applications.
De Luca, A., Albu-Schaffer, A., Haddadin, S., and
Hirzinger, G. (2006). Collision detection and safe re-
action with the dlr-iii lightweight manipulator arm. In
Intelligent Robots and Systems, 2006 IEEE/RSJ Inter-
national Conference on. IEEE.
Dhillon, S. S., Chakrabarty, K., and Iyengar, S. S. (2002).
Sensor placement for grid coverage under imprecise
detections. Information Fusion, 2002. Proceedings of
the Fifth International Conference on.
Dunn, E., Olague, G., and Lutton, E. (2006). Parisian
camera placement for vision metrology: Evolutionary
Computer Vision and Image Understanding. Pattern
Recognition Letters.
Ebert, D. M. and Henrich, D. D. (2002). Safe human-robot-
cooperation: Image-based collision detection for in-
dustrial robots. In Intelligent Robots and Systems,
2002. IEEE/RSJ International Conference on. IEEE.
Fischer, M. and Henrich, D. (2009). 3D collision detec-
tion for industrial robots and unknown obstacles us-
ing multiple depth images. Advances in Robotics Re-
search.
Flacco, F. and De Luca, A. (2010). Multiple depth/presence
sensors: Integration and optimal placement for hu-
man/robot coexistence. In Robotics and Automa-
tion (ICRA), 2010 IEEE International Conference on.
IEEE.
Graf, J., Puls, S., and W¨orn, H. (2010). Recognition and un-
derstanding situations and activities with description
logics for safe human-robot cooperation. In COGNI-
TIVE 2010, The Second International Conference on
Advanced Cognitive Technologies and Applications.
Haddadin, S. (2013). Towards Safe Robots: Approaching
Asimov’s 1st Law. Springer Publishing Company, In-
corporated.
Henrich, D. and Gecks, T. (2008). Multi-camera collision
detection between known and unknown objects. In
Distributed Smart Cameras, 2008. ICDSC 2008. Sec-
ond ACM/IEEE International Conference on. IEEE.
Kulic, D. and Croft, E. (2007). Affective state estimation
for human–robot interaction. Robotics, IEEE Trans-
actions on.
Lacevic, B. and Rocco, P. (2010). Kinetostatic danger field -
a novel safety assessment for human-robot interaction.
In Intelligent Robots and Systems (IROS), 2010.
Lenz, C. (2012). Fusing multiple kinects to survey shared
human-robot-workspaces. Technical report, Techni-
cal Report Technical Report TUM-I1214, Technische
Universit¨at M¨unchen, Munich, Germany.
Mittal, A. and Davis, L. (2008). A General Method for
Sensor Planning in Multi-Sensor Systems: Extension
to Random Occlusion. International journal of com-
puter vision, 76(1):31–52.
Nikolaidis, S., Ueda, R., Hayashi, A., and Arai, T. (2009).
Optimal camera placement considering mobile robot
trajectory. In Robotics and Biomimetics, 2008. IEEE
International Conference on. IEEE.
O’rourke, J. (1987). Art gallery theorems and algorithms,
volume 1092. Oxford University Press Oxford.
Siegwart, R., Nourbakhsh, I. R., and Scaramuzza, D.
(2011). Introduction to autonomous mobile robots.
MIT Press.
Sisbot, E., Marin-Urias, L., Broquere, X., Sidobre, D., and
Alami, R. (2010). Synthesizing robot motions adapted
to human presence. International Journal of Social
Robotics.
Yao, Y., Chen, C.-H., Abidi, B., Page, D., Koschan, A.,
and Abidi, M. (2008). Sensor planning for automated
and persistent object tracking with multiple cameras.
In Computer Vision and Pattern Recognition, 2008.
IEEE Conference on. IEEE.
ICINCO2014-11thInternationalConferenceonInformaticsinControl,AutomationandRobotics
318