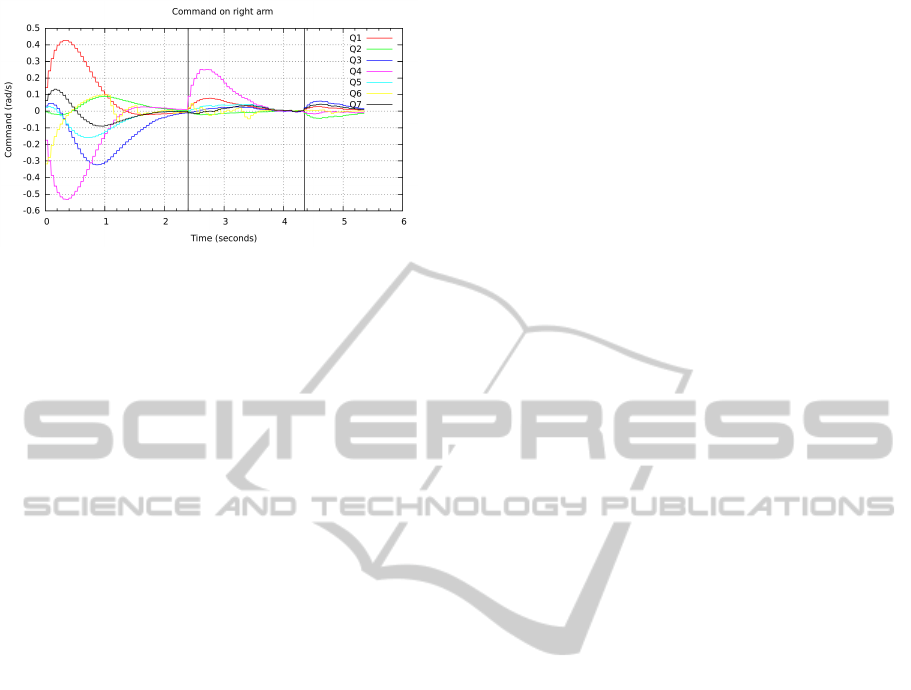
Figure 7: Control sent to the left arm.
5 CONCLUSION
In this paper, we have tackled the problem of coor-
dinating two manipulator arms from a control point
of view. We have proposed a vision-based control
strategy allowing to truly coordinate the motions of
a dual-arm robotic system. The task to be performed
has been described by a sequence of three subtasks.
Each of them is defined by visual features character-
izing the relative pose between the end effectors so
that a true collaboration between both arms has been
achieved. A multi-cameras image based visual ser-
voing has then been designed. Finally, the proposed
control strategy has been validated and the obtained
simulation results have demonstrated its interest and
its efficiency.
Now, to go further and improve our approach, it is
necessary to take into account the unexpected events
which may occur during the task and hamper its exe-
cution (e.g., joint limits, singularities, collisions, oc-
clusions, etc.). Therefore, our next step will be to ad-
dress this problem by taking advantage of the system
redundancy. In addition to these theoretical improve-
ments, we also plan to experimentally validate our ap-
proach on the LAAS PR2 robot and to perform more
complex coordination tasks.
REFERENCES
Adorno, B., Fraisse, P., and Druon, S. (2010). Dual posi-
tion control strategies using the cooperative dual task-
space framework. In Intelligent Robots and Systems
(IROS), 2010 IEEE/RSJ International Conference on,
pages 3955–3960.
Albrichsfeld, C. V. and Tolle, H. (2002). A self-adjusting
active compliance controller for multiple robots han-
dling an object. Control Engineering Practice,
10(2):165 – 173.
Berry, F., Martinet, P., and Gallice, J. (2000). Turning
around an unknown object using visual servoing. In
Intelligent Robots and Systems, 2000. (IROS 2000).
Proceedings. 2000 IEEE/RSJ International Confer-
ence on, volume 1, pages 257–262 vol.1.
Bonitz, R. and Hsia, T. (1996). Robust internal-force based
impedance control for coordinating manipulators-
theory and experiments. In Robotics and Automation,
1996. Proceedings., 1996 IEEE International Confer-
ence on, volume 1, pages 622–628 vol.1.
Caccavale, F., Ciro, N., Siciliano, B., and Villani, L. (2001).
Achieving a cooperative behavior in a dual-arm robot
system via a modular control structure. Journal of
Robotic Systems, 18(12):691–699.
Caccavale, F. and Uchiyama, M. (2008). Cooperative ma-
nipulators. In Siciliano, B. and Khatib, O., edi-
tors, Springer Handbook of Robotics, pages 701–718.
Springer Berlin Heidelberg.
Chaumette, F. (2002a). A first step toward visual servoing
using image moments. In Intelligent Robots and Sys-
tems, 2002. IEEE/RSJ International Conference on,
volume 1, pages 378–383 vol.1.
Chaumette, F. (2002b). La commande des robots manipu-
lateurs: Asservissement visuel, chapter 3, pages 101 –
151.
Chaumette, F. and Hutchinson, S. (2006). Visual servo con-
trol part 1: Basic approaches. IEEE Robotics and Au-
tomation Magazine, 13(4):82–90.
Dauchez, P., Fraisse, P., and Pierrot, F. (2005). A vi-
sion/position/force control approach for performing
assembly tasks with a humanoid robot. In 5th IEEE-
RAS International Conference on Humanoid Robots,
pages 277–282.
Espiau, B., Chaumette, F., and Rives, P. (1992). A new
approach to visual servoing in robotics. IEEE Trans-
actions on Robotics and Automation, 8(3):313–326.
Hynes, P., Dodds, G., and Wilkinson, A. J. (2006). Un-
calibrated visual-servoing of a dual-arm robot for mis
suturing. In The First IEEE/RAS-EMBS International
Conference on Biomedical Robotics and Biomecha-
tronics, pages 420–425.
Kermorgant, O. and Chaumette, F. (2011). Multi-sensor
data fusion in sensor-based control application to
multi-camera visual servoing. In IEEE International
Conference on Robotics and Automation, pages 4518–
4523.
Kraus, W., J. and McCarragher, B. J. (1997). Hybrid posi-
tion/force coordination for dual-arm manipulation of
flexible materials. In Intelligent Robots and Systems,
1997. IROS ’97., Proceedings of the 1997 IEEE/RSJ
International Conference on, volume 1, pages 202–
207 vol.1.
Mansard, N. and Chaumette, F. (2004). Tasks sequencing
for visual servoing. In Intelligent Robots and Systems,
2004. (IROS 2004). Proceedings. 2004 IEEE/RSJ In-
ternational Conference on, volume 1, pages 992–997
vol.1.
Miyabe, T., Konno, A., and Uchiyama, M. (2003). Auto-
mated object capturing with a two-arm flexible ma-
nipulator. In Robotics and Automation, 2003. Pro-
ceedings. ICRA ’03. IEEE International Conference
on, volume 2, pages 2529–2534 vol.2.
Multi-camerasVisualServoingtoPerformaCoordinatedTaskusingaDualArmRobot
43