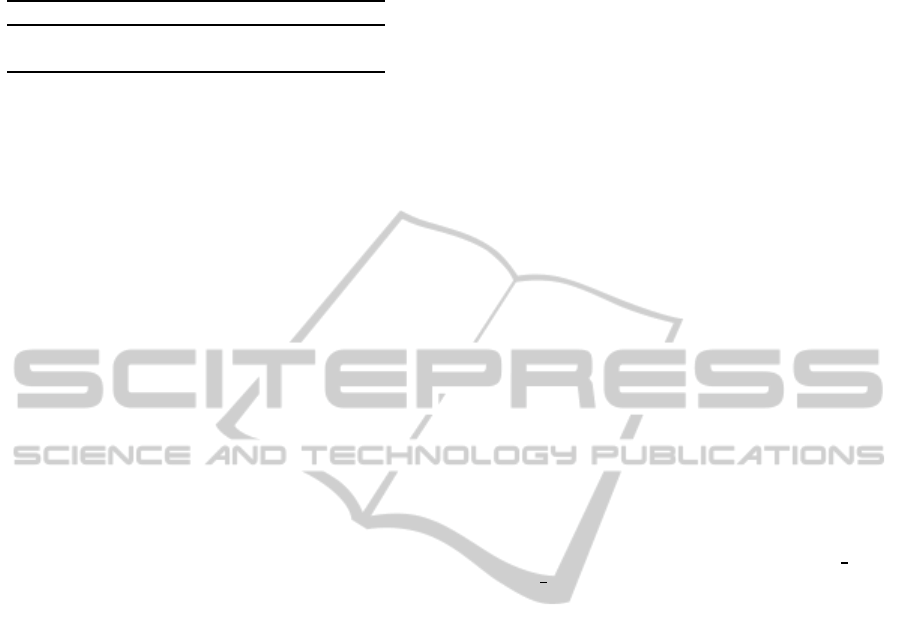
Table 1: Results of experimenting with real revolute joint
AX-12 servo drive.
Play True pos. [%] False neg. [%]
With play 98 2
W/o play 100 0
ing it was necessary to obtain also samples without
play. To ensure that the conditions for the measure-
ment of motion with play and without play will be
the same a small trick was used. The servo drive was
not used as a motivator. Base link of the experimen-
tal robot was actuated so entire experimental robot
was moving. To test detection of mechanical play the
robot was straightened and the servo drive was config-
ured to keep its position. The entire robot was waved
in direction perpendicular to the axis of servo drive
and to the common axis of both links so mechanical
play of the servo drive was excited. To test motion
without mechanical play the servo drive was bypassed
by mounting two links of robot together by solid met-
alic part so the servo drive could not move anymore.
Other difficulty was the actuator itself. It was nec-
essary to actuate entire robot by actuator without its
own play. As a simple solution of actuator without
play human hand was used. Human hand can hardly
generate perfectly periodic motion but for this exper-
iment it was not essential because impacts appear ev-
ery time the acceleration changes its direction.
Results of the experiment are shown in table 1.
The true positivein the table 1 means that the property
was detected correctly. The false negative means that
the property was not detected despite it was present in
the sample. False positive is not present in the table
beacause the properties are in mutual exclusive rela-
tion so false negative of one property is false positive
of the other.
5 CONCLUSION
In this paper a method of detection of mechanical
play based on impact recognition was proposed. The
method in proposed form is usable for revolute joints
only. Theoretical principles were tested on real joint
based on Dynamixel AX-12A servo drive. Experi-
ments prove that the method is usable for distinguish-
ing between motion of servo drive with play and with-
out play. Reliability of detection was not perfect.
There are still several problems that need to be
solved in the future before the method will be us-
able in common use cases. Extending this method to
robots with more than one degree of freedom bring
a problem of distiguishing between sources of the
play - especially if there are two joints with parallel
axes. Another problem is automatized way of find-
ing proper values for the parameters of the method
and also proper value of acceleration of the excita-
tion motion. It would be also very useful to extend
the method to not only detect the mechanical play but
also measure the size of mechanical play.
ACKNOWLEDGEMENTS
This work was supported by the European Regional
Development Fund in the IT4Innovations Centre of
Excellence project (CZ.1.05/1.1.00/02.0070).
REFERENCES
Ahmad, S. (1985). Second order nonlinear kinematic ef-
fects and their compensation. School ef Electrical En-
gineering, Purdue University.
Collective of employees of ROBOTIS ComSchool ef Elec-
trical Engineering, P. U. (2006). Dynamixel AX-12
User’s Manual. ROBOTIS Company.
Diankov, R. (2010). Automated construction of
robotic manipulation programs. Carnegie Mel-
lon University, Robotics Institute, CMU-RI-TR-10-
29, http://www.programmingvision.com/rosen
di-
ankov
thesis.pdf.
Gautier M., Janot A., Vandanjon P.O. (2008). Didim: A new
method for the dynamic identification of robotsfrom
only torque data. In IEEE International Conference
on Robotics and Automation,. Pasadena, CA, USA.
Hyun-Kyu Lim, Dong-Heyok Kim, S.-R. K. and Kang, H.-
J. (2009). A practical approach to enhance positioning
accuracy for industrial robots. IROS-SICE Interna-
tional Joint Conference.
Koenig, N. and Howard, A. (2004). Design and use
paradigms for gazebo, an open-source multi-robot
simulator. In In IEEE/RSJ International Conference
on Intelligent Robots and Systems, pages 2149–2154.
Meng Li, Tian Huang, Z. L. (2003). Conceptual design and
kinematic analysis of 3-dof robot wrist. International
Conference on Robotics & Automation.
Michel, O. (2004). Professional mobile robot simulation.
International Journal of Advanced Robotic Systems,
1(4):39–42. Commercial Mobile Robot Simulation
Software.
R. Kalantari, M. S. F. (2009). Backlash nonlinearity model-
ing and adaptive controller design for and electrome-
chanical power transmission system. Mechanical En-
gineering, 16(6):463 – 469.
S¸ucan, I. A., Moll, M., and Kavraki, L. E. (2012).
The Open Motion Planning Library. IEEE
Robotics & Automation Magazine, 19(4):72–82.
http://ompl.kavrakilab.org.
ICINCO2014-11thInternationalConferenceonInformaticsinControl,AutomationandRobotics
332