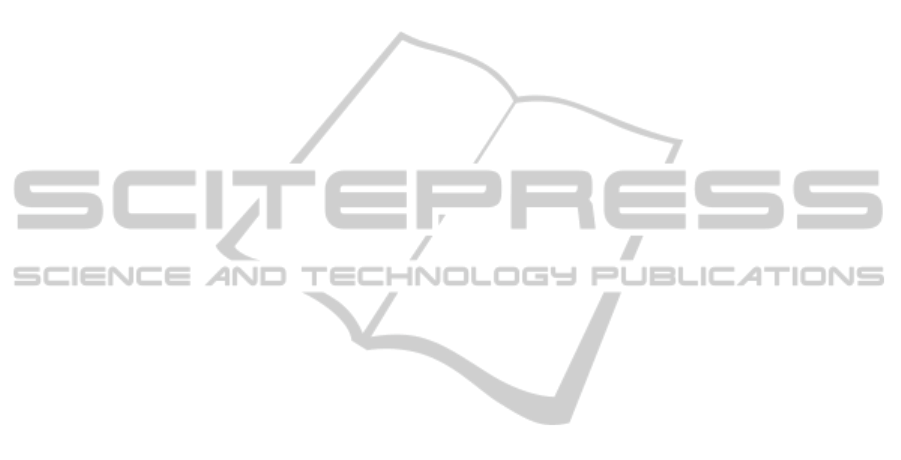
limitation and actuator constraints systematically. In
this approach, the swing-up maneuver of an inverted
pendulum from downward equilibrium to upward
equilibrium is accomplished within a two-degrees of
freedom control scheme consisting of nonlinear opti-
mal feedforward controller and the optimal feedback
controller. The feedforward control input trajectory
is generated by the newly developed optimal control
solver that can handle the input and output constraints
of the system. Simulation and experimental results
showed close resemblance, which shows that the pro-
posed method is quite practical. The swing-up of
the inverted pendulum through the proposed method
turned out to be always successful. The proposed ap-
proach enables one to make the most of performance
of the given actuator. The presented approach can be
extended to the swing-up control of a double or triple
inverted pendulum without much of modification.
ACKNOWLEDGEMENTS
This research was supported by the MSIP(Ministry
of Science, ICT and Future Planning), Korea, un-
der the C-ITRC(Convergence Information Technol-
ogy Research Center)support program(NIPA-2014-
H0401-14-1003) supervised by the NIPA(National IT
Industry Promotion Agency) and was also supported
by Korea Electric Power Corporation Research Insti-
tute through Korea Electrical Engineering & Science
Research Institute (grant number: R13GA04).
REFERENCES
˚
Astr
¨
om, K. and Furuta, K. (2000). Swinging up a pendulum
by energy control. Automatica, 36(2):287–295.
Chung, C. C. and Hauser, J. (1995). Nonlinear control of a
swinging pendulum. Automatica, 31(6):851–862.
Furuta, K., Yamakitan, M., and Kobayashi, S. (1992).
Swing-up control of inverted pendulum using pseudo-
state feedback. Journal of Systems and Control Engi-
neering, 206:263–269.
Graichen, K., Treuer, M., and Zeitz, M. (2007). Swing up
of the double pendulum on a cart by feedforward and
feedback control with experimental validation. Auto-
matica, 43:63–71.
Graichen, K. and Zeitz, M. (2005a). Feedforward control
design for nonlinear systems under input constraints.
In Meuer, T., Graichen, K., and Gilles, E. D., edi-
tors, Control and observer design for nonlinear finite
and infinite dimensional systems, LNCIS Volumn 322,
pages 235–252. Springer.
Graichen, K. and Zeitz, M. (2005b). Nonlinear feedfoward
and feedback tracking control with input constraints
solving the pendubot swing-up problem. In Proceed-
ings of the 16th IFAC World Congress, pages 841–841,
Prague, Czech.
Graichen, K. and Zeitz, M. (2008). Feedforward control
design for finite-time transition problems of nonlin-
ear systems with input and output constraints. IEEE
Transactions on Automatic Control, 53(5):1273–
1286.
Patterson, M. A. and Rao, A. V. (2014). GPOPS - II Version
1.0: A general-purpose Matlab toolbox for solving op-
timal control problems using variable-order Gaussian
quadrature collocation methods.
Rubi, J., Rubio, A., and Avello, A. (2002). Swing-up con-
trol problem for a self-erecting double inverted pen-
dulum. IEE Proceedings-Control Theory and Appli-
cations, 149(2):169–175.
Spong, M. and Block, D. (1995). The pendubot: a mecha-
tronic system for control research and education. In
Proceedings of the 35th IEEE Conference on Decision
and control,, pages 555–556, New Orleans, USA.
Wilklund, M., Kristenson, A., and
˚
Astr
¨
om, K. (1993). A
new strategy for swing up an inverted pendulum. In
Proceedings of IFAC 12th world congress, volume 9,
pages 151–154, Sydney, Australia.
Yang, J. H., Shim, S. Y., Seo, J. H., and Lee, Y. S. (2009).
Swing up control for an inverted pendulum with re-
stricted cart rail length. International Journal of Con-
trol, Automation, and Systems, 70(4):674–680.
ICINCO2014-11thInternationalConferenceonInformaticsinControl,AutomationandRobotics
482