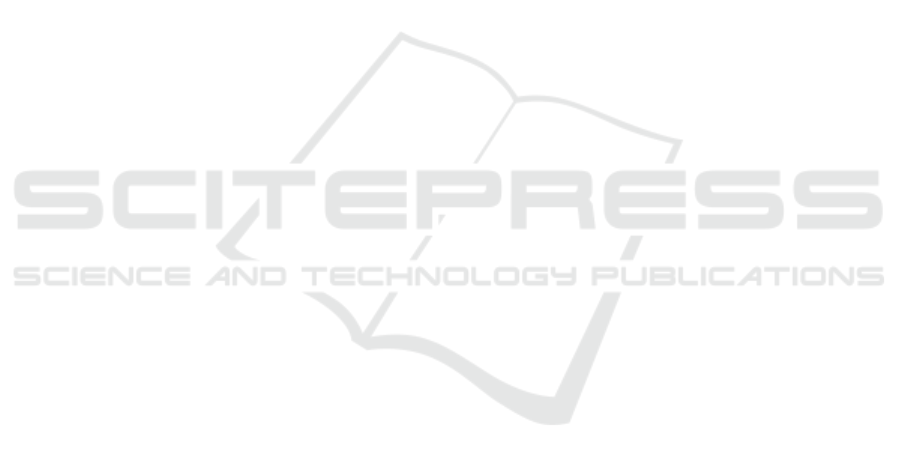
Research of Cable Identification Method
Based on Single Fiber
Qiang Sun and Qifu Wu
School of Electronics and Information Engineering , Beijing Jiaotong University, Beijing, China
Keywords: Interference, Redundant Fiber, Phase Difference.
Abstract: Optical cable identification plays a very important role in cable maintenance and fault detection. In this paper,
a new cable identification method based on optical fiber end reflection is proposed. Based on the theory of
optical fiber sensor and phase modulation technology, single fiber optical cable identification is effectively
achieved. System composition of this method is introduced in this paper. According to light interference
principle, the expression of phase change when signal acts on fiber sensor is deduced; the relationship
between redundant optical fiber and the system output signal is analyzed. The reasonable redundant fiber
length is obtained by Matlab simulation, and the feasibility of the method is verified by experiment.
Compared with other cable identification method, experimental results show that the single fiber optical cable
identification has greatly improved in detection sensitivity and low maintenance time and costs.
1 INTRODUCTION
With the rapid development of optical fiber
communication technology, it has become an
important platform of much information, such as
voice, data and images (Tan et al., 2006). As a basic
transmission carrier of optical communication
network, the optical cable has almost covered the
major national backbone network. The portion of the
cable label begins to blur, even to drop off with the
time going on (Huang et al., 2007). So when optical
cable has fault, it is a difficult work to identify the
target cable quickly and easily (Yao and Zhang,
2008; Leonowicz et al., 2006). Based on optical
fiber end face reflection, this paper proposed a new
cable single fiber identification method according to
the characteristics of the optical signal interference.
This method achieves cable single fiber
identification with fast response and has the same
accuracy in the entire measuring range.
There are mainly three kinds of cable
identification methods at present, including artificial
pulling, optical power test, and dual fiber optic cable
identification. Artificial pulling method is pulling
the cable directly to identify the fiber optical cable
along the damage locations by the maintenance
workers. This method is very clumsy and consumes
long time. Optical power test method is receiving
end of the fiber optical power changes by real-time
monitoring to achieve the object of identifying
cable. This method is not accurate positioning and
low accuracy. Dual fiber optic cable identification
method (Sun and Chen, 2011) has high detection
accuracy, but this method requires the double fiber
loop, which cannot identify the only one dark fiber
of the cable.
In this paper, a new cable identification method
is proposed based on single fiber. This method will
not damage to the cables, and high detection
sensitivity, greatly reduce the fiber optic network
management, repair and maintenance time and costs.
Users can easily find the object cable by knocking
the optical cable.
2 SYSTEM COMPONENTS OF
CABLE SINGLE FIBER
IDENTIFICATION
As is shown in Figure 1, the principle of single fiber
identification system is light emitting from the light
source via the coupler 1 divided into two paths. The
first light reaches to coupler 2 directly, and then
reaches reflection face via the sensor fiber, after
reflection, reaches coupler 1 all the way through
sensor fiber, coupler 2, and redundant fiber. The
45
Sun Q. and Wu Q..
Research of Cable Identification Method Based on Single Fiber.
DOI: 10.5220/0005022500450050
In Proceedings of the 5th International Conference on Optical Communication Systems (OPTICS-2014), pages 45-50
ISBN: 978-989-758-044-4
Copyright
c
2014 SCITEPRESS (Science and Technology Publications, Lda.)