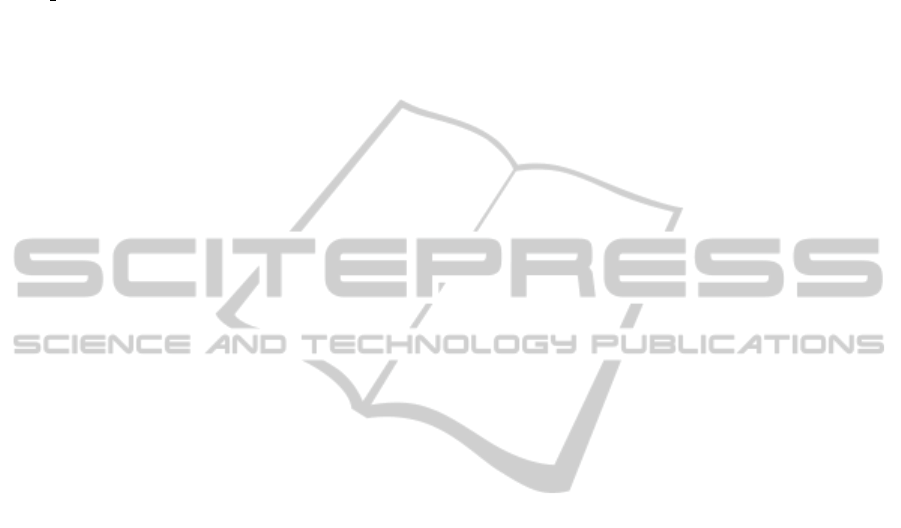
Shirdel, A. H., Bjork, K-M., Toivonen, H. T.: Identifica-
tion of Linear Switching System with Unknown Di-
mensions. In: 47 Hawaii International Conference on
System Sciences, HICSS-47 (2014)
The Association of Finnish Steel and Metal Pro-
ducers, Structure Review of Metal Refinement
(2012), http://www.teknologiateollisuus.fi/file/14190/
MJ rakennekatsaus212.pdf.html
Geerdes, M., Toxopeus, H. L., Van der Vliet, C.,
Chaigneau, R., Vander, T.: Modern Blast Furnace
Ironmaking: An Introduction. Ios PressInc, ISBN
9781607500407(2009)
Nath, N. K.: Simulation of gas flow in blast fur-
nace for different burden distribution and cohesive
zone shape. Materials and Manufacturing Processes,
17(5):671681 (2002). doi: 10.1081/AMP-120016090
Danloy, J., Mignon, R., Munnix, G., Dauwels, L., Bonte, L.:
A blast furnace model to optimize the burden distri-
bution. In: 60th Ironmaking Conference Proceedings,
pages 3748, Baltimore (2001)
Yu, Y., Saxn, H.: Experimental and dem study
of segregation of ternary size particles in a
blast furnace top bunker model. Chemical En-
gineering Science, 65(18):52375250 (2010). doi:
10.1016/j.ces.2010.06.025
Agarwal, A., Tewary, U., Petterson, F., Das, S.,
Saxn, H., Chakraborti,N.: Analysing blast fur-
nace data using evolutionary neural network
and multiobjective genetic algorithms. Ironmak-
ing and Steelmaking, 37(5):353359 (2010). doi:
10.1179/030192310X12683075004672
Saxn, H., stermark, R.: Varmax-modelling of blast furnace
process variables. European Journal of Operational
Research, 90(1):85101 (1996). doi: 10.1016/0377-
2217(94) 00304- 1
Korpi, M., Toivonen, H., Saxn,B.: Modelling and identifica-
tion of the feed preparation process of a copper flash
smelter. Computer Aided Chemical Engineering, El-
sevier (2003),(14):731-736, ISSN 1570-7946, ISBN
9780444513687
Bhattacharya, T.: Prediction of silicon content in blast fur-
nace hot metal using partial least squares (pls). ISIJ
International, 45(12):19431945, (2005)
Hao, X., Zheng, P., Xie, Z., Du, G., Shen, F.: A predic-
tive modeling for blast furnace by integrating neu-
ral network with partial least squares regression. In:
IEEE International Conference on industrial tech-
nology, volume 3, pages 11621167 Vol. 3,106-107
(2004). doi: 10.1109/ICIT.2004.1490724
Helle, M., Saxn, H.: A method for detecting cause-effects in
data from complex processes. In: Proceedings of the
International Conference in Coimbra, Pages 104107,
Portugal (2005)
Pettersson, F., Chakraborti, N., Saxn, H.: A genetic algo-
rithm based multi-objective neural net applied to noisy
blast furnace data. Applied Soft Computing, Volume
7, Issue 1, January 2007, Pages 387397
Heemels, W.P.M.H., De Schutter, B., Bemporad, A.: Equiv-
alence of hybrid dynamical models. Automatica, vol.
37, no. 7, pp. 10851091, (2001)
Sontag, E. D.: Nonlinear regulation: The piecewise linear
approach. IEEE Trans. Automatic Control, vol. 26, no.
2, pp. 346358, (1981)
Lin, J. N., Unbehauen, R.: Canonical Piecewise-linear
Approximations. IEEE Trans. Circuits Systems I-
Fundamental Theory and Applications, vol. 39, no. 8,
pp. 697699, (1992)
Saad, A., Avineri, E., Dahal, K., Sarfraz, M.: Soft Comput-
ing in Industrial Applications, Springer (2007)
Aliev, R. A., Fazlollahi, B, Aliev, R. R.: Soft Comput-
ing and Its Applications in Business and Economics,
Springer, edition 5 (2004)
Ohlsson, H.,Ljung, L., Boyd, S.: Segmentation of ARX-
models using sum-of-norms regularization. Automat-
ica, vol. 46, pp. 1107-1111 (2010)
Bako, L.: Identification of switched linear systems via
sparse optimization. Automatica, vol. 47, pp. 668-677
(2011)
Le, V. L., Lauer, F., Bako, L., Bloch. G.: Learning nonlin-
ear hybrid systems: from sparse optimization to sup-
port vector regression. In: HSCC - 16th ACM Inter-
national Conference on Hybrid systems: Computation
and Control - 33-42 (2013)
Lughofer, E. and Kindermann, S. (2010). SparseFIS: Data-
driven learning of fuzzy systems with sparsity con-
straints. Fuzzy Systems, IEEE Transactions on, 18(2),
396-411.
ICINCO2014-11thInternationalConferenceonInformaticsinControl,AutomationandRobotics
648