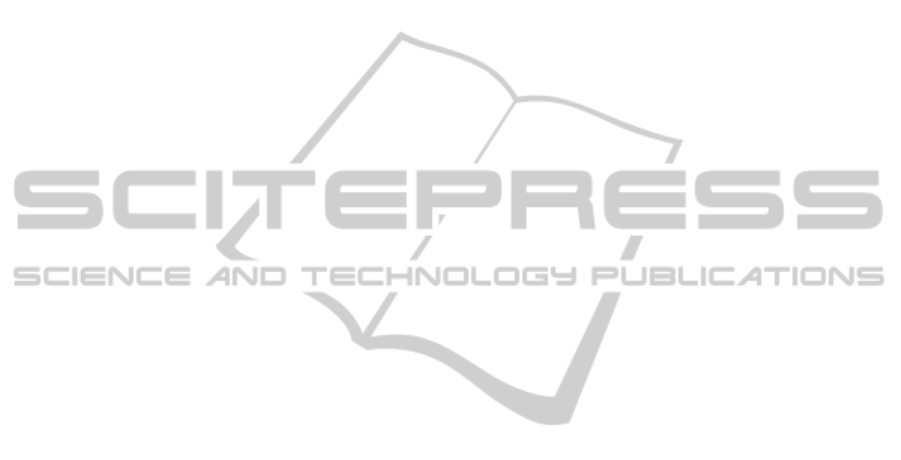
EIMaraghy, W. H , Urbanic, R.J. (2004) ‘Assessment of
Manufacturing Operational Complexity’, CIRP
Annals, vol. 53, issue 1, pp. 401–406.
Zeltzer, L., Limère,V., Aghezzaf, E. H., Van Landeghem,
H. (2012) ’Measuring the Objective Complexity of
Assembly Workstations’, Conference Proceedings,
Seventh International Conference on Computing in the
Global Information Technology
Karger, D. W., Hancock, W. M. (1982) Advanced work
measurement, New York, Industrial Press
Konz, S. (2001) Methods engineering. In Handbook of
Industrial Engineering, 3rd edition., pp. 1353–1390,
New York, Wiley
Elnekave, M., Gilad, I. (2006) ‘Rapid video-based analysis
system for advanced work measurement’,
International Journal of Production Research, vol. 44,
issue 2, pp. 271-290
Dencker, B., Balzer, H-J.,Theuerkauf, W. E., Schweres,
M. (1999) ‘Using a production-integrated video
learning system (PVL) in the assembly sector of the
car manufacturing industry’, International Journal of
Production Ergonomics, Vol. 23, Issues 5-6, pp. 525-
537
Taylor, P. (2011) ‘From figure skaters to the factory floor’
[online], Available: http://www.ft.com/intl/cms/s/
0/fc571624-ce98-11e0-a22c-00144feabdc0.html [24
Jun 2014]
Fisher, M. L. and Ittner, C. D. (1999), ‘The impact of
product variety on automobile assembly operations:
empirical evidence and simulation analysis’,
Management Science, Vol. 45, pp. 771-786
Fisher, M. L., Jain, A. and MacDuffie, J.P. (1995)
‘Strategies for product variety: lessons from the auto
industry’, B. Kogut & E.Bowman, Eds. Redesigning
the Firm., pp. 116-154, Oxford U. Press
Ouvriach, K., Dailey, M. N. (2010) ‘Clustering human
behaviours with dynamic time warping and hidden
Markov models for a video surveillance system’,
Conference Proceedings, International Conference on
electrical engineering/electronics computer
telecommunications and information technology
(ECTICON), pp. 884-888
Slembrouck, M., Van Cauwelaert, D., Van Hamme, D.,
Van Haerenborgh, D., Van Hese, P., Veelaert, P., &
Philips, W. (2014). Self-learning voxel-based multi-
camera occlusion maps for 3D reconstruction.
Conference Proceedings, 9th International Joint
Conference on Computer Vision, Imaging and
Computer Graphics Theory and Applications
(VISAPP - 2014), SCITEPRESS.
Müller, M. (2007) Information Retrieval for Music and
Motion, Springer
Laurentini, A. (1994) The Visual Hull Concept for
Silhouette-Based Image Understanding. IEEE Trans.
Pattern Anal. Mach. Intell., Vol. 16, no. 2, pp. 150-
162.
Bodor, R., Jackson, B., Papanikolopoulos, N., (2003)
‘Vision-Based Human Tracking and Activity
Recognition’, Conference Proceedings, 11
th
Mediterranean Conference on Control and
Automation, Rodos
Cristani, M., Raghavendra, R., Del Bue, A., Murino, V.
(2013)Human behavior analysis in video surveillance:
A Social Signal Processing perspective,
Neurocomputing, Vol. 100, January, pp.86-97.
AnAutomatedWorkCycleClassificationandDisturbanceDetectionToolforAssemblyLineWorkStations
691