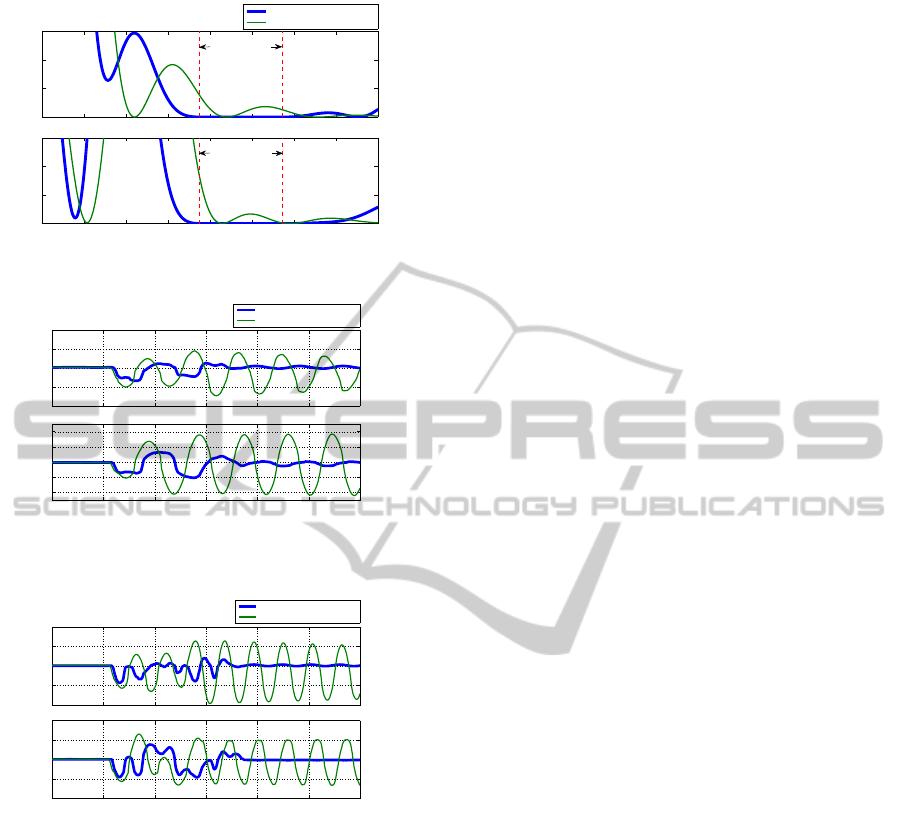
Power spectrum on X− axis
With vibration suppression
Without vibration suppression
0 1 2 3 4 5 6 7 8
0
5
10
15
Power spectrum on Y− axis
Frequency[rad/s]
Suppression band
Suppression band
Figure 9: Power spectrums of control inputs.
0 2 4 6 8 10 12
−0.4
−0.2
0
0.2
0.4
Sway angle (X−axis) [rad]
With vibration suppression
Without vibration suppression
0 2 4 6 8 10 12
−0.4
−0.2
0
0.2
0.4
Time [s]
Sway angle (Y−axis) [rad]
Figure 10: Experiment results of vibration with natural an-
gular frequency 3.74[rad/s] (Rope length:0.7[m]).
0 2 4 6 8 10 12
−0.4
−0.2
0
0.2
0.4
Sway angle(X−axis) [rad]
With Vibration suppression
Without vibration suppression
0 2 4 6 8 10 12
−0.4
−0.2
0
0.2
0.4
Sway angle(Y−axis) [rad]
Time [s]
Figure 11: Experiment results of vibration with natural an-
gular frequency 5.72[rad/s] (Rope length:0.3[m]).
The proposed method makes the transfer object avoid
the obstacles, the motion suppress the vibration in the
transfer object, and the state and the control input
keep under the constraints. Moreover, the fast solu-
tion which shorten the calculation time of the trajec-
tory optimization has been proposed in this study. In
the experiments for validating the proposed method, it
was seen that the vibration suppression, the obstacles
avoidance are accomplished. In the future works, we
will discuss the smooth interpolation method so that
the velocity and the acceleration of the transfer object
fall within the constraints.
REFERENCES
Kawakami, S, Miyoshi, T and Terashima, K, Path Planning
of Transferred Load Considering Obstacle Avoidance
for Overhead Crane, System Integration Division An-
nual Conference, p.640-641, 2003
Negishi, M, Masuda, H, Ohsumi, H and Tamura, Y, Eval-
uation of overhead crane trajectory, JSME Confer-
ence on Robotics and Mechatronics, p.1A2-p19(1)-
(4), 2013
Yano, K, Eguchi, K and Terashima, K, Sensor-Less Sway
Control of Rotary Crane Considering the Collision
Avoidance to the Ground, Transactions of the Japan
Society of Mechanical Engineers, Series(C), Vol. 68,
No. 676, p.146-153
A. Z. Al-Garni, K. A. F. Moustafa and S. S. A. K. Javeed
Nizami, Optimal Control of Overhead Cranes, Con-
trol Eng. Practice, Vol.3, No.9, p.1277-1284, 1995
Takagi, K, and Nishimura, H, Gain-Scheduled Control of A
Tower Crane Considering Varying Load-Rope Length,
Transactions of the Japan Society of Mechanical En-
gineers, Series(C), Vol. 64, No. 626, p.113-120
Harald, A and Dominik, S, Passivity-Based Trajectory Con-
trol of and Overhead Crane by Interconnection and
Damping Assignment, Motion and Vibration Control
, p.21-30, 2009
Murakami, S and Ikeda, T, Vibration suppression for High
Speed Position Control of overhead Traveling Crane
by Acceleration Inputs, Dynamics & Design Confer-
ence, p.128(1)-(6), 2006
Brunner, M, Bruggemann, B, and Schulz, D, Autonomously
Traversing Obstacle: Metrics for Path Planning of
Reconfigurable Robots on Rough Terrain, Proceed-
ings of 9th International Conference on Informatics in
Control, Automation and Robotics, p.58-69, 2012
Yu-Cheng, C, Wei-Han, H, Shin-Chung, K, A fast path
planning method for single and dual crane erections,
Automation in Construction, Volume 22, p. 468-480,
2012
Tamura, Y, Hamasaki, S, Yamashita, A and Asama, H,
Collision Avoidance of Mobile Robot Based on Pre-
diction of Human Movement According to Environ-
ments, Transactions of the Japan Society of Mechani-
cal Engineers, Series(C), Vol. 79, No. 799, p.617-628
Suzuki, M and Terashima, K, Three Dimensional Path
Planning using Potential Method for Overhead Crane,
Journal of Robotics Society of Japan, Vol.18, No.5,
p.728-736, 2000
ICINCO2014-11thInternationalConferenceonInformaticsinControl,AutomationandRobotics
660