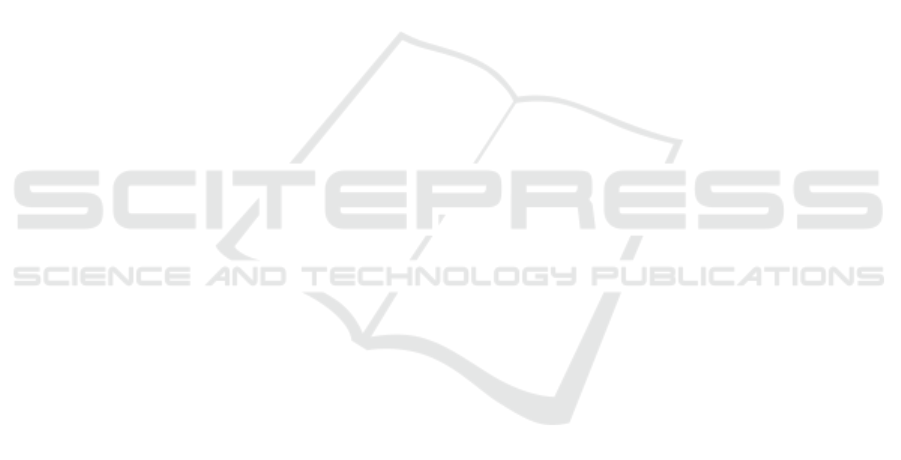
Soil Strength-based Estimation of Optimal Control Parameters
for Wheeled Robots on Rough Terrain
Jayoung Kim and Jihong Lee
Dept. Of Mechatronics Engineering, Chungnam National University, Gungdong, Daejeon, Korea
Keywords: Optimal Control Parameter, Maximum Traction Coefficient, Optimal Slip Ratio, Tractive Efficiency, Soil
Strength, Vehicle Dynamics, State Observer, Soil Identification, Wheeled Robot, Rough Terrain.
Abstract: On rough terrain, there are a variety of soil types having different soil strength. It means that it is needed for
outdoor robots to change wheel control strategies since optimal slip and maximum traction levels on wheels
differ depending on soil strength. Therefore this paper proposes an algorithm for acquiring optimal control
parameters, such as maximum traction coefficient and optimal slip ratio to maximize traction or minimize
energy consumption, based on estimating strength of soils. In this paper the optimal models of wheel
traction and slip are derived through indoor experiments by a testbed for analysis of wheel-terrain
interactions on three types of soil; grass, gravel and sand. For estimating soil strength, actual traction
coefficient, including information of motion resistance, is observed by a state estimator related to wheeled
robot dynamics. The actual traction coefficient and slip ratio on wheels are employed to estimate soil
strength by a numerical method on the basis of derived optimal models. The proposed algorithm was
verified through real driving experiments of a wheeled robot on various types of soil.
1 INTRODUCTION
Outdoor wheeled robots have overcame obstructions
of moving on rough terrains, such as a slippery
surface or a steep slope, in order to fulfil important
tasks regarding the purpose of exploration,
reconnaissance, rescue, etc. For achieving such goals,
wheeled robots should have abilities to handle two
kinds of characteristic changes on rough terrains; a
change of soil types (slippery or non-slippery) and
surface shapes (flat or steep). Both the terrain
characteristic changes are crucial factors in the
decision regarding optimal wheel slip or traction as a
control parameter of a wheel controller since tractive
force of a wheel is differently exerted on a surface
according to such changes (Terry et al., 2008, Krebs
et al., 2010, Joo et al., 2013, Ding et al, 2010,
Ishigami et al., 2008, Brooks et al., 2012). In case of
changing surface shapes, it is relatively easy for
wheeled robots to realize the level of the change by
motion sensors like inertial measurement units
(IMU). On the contrary to this, it is not such an easy
undertaking to judge a type of soil where a robot is
operated in spite of using various sensors mounted
on a robot. To solve this issue, many researches
related to soil identification have been introduced in
the field of robotics.
The studies on soil identification based on
proprioceptive sensor data, not including dynamic
state information of a moving robot, have been
proposed. As proprioceptive sensors, the vibration
information of an accelerometer or IMU and the
current information of wheel motors were used to
make the data signals, which are transformed into
soil feature data in frequency domain using a Fast
Fourier Transform (FFT). The soil feature data were
classified into one of pre-learned soil models by a
support vector machine (SVM) (Brooks et al., 2012,
Iagnemma et al., 2005) or a probabilistic neural
network (PNN) (Coyle et al., 2008, Ojeda et al.,
2006). The performance of identifying a soil type
was verified through driving simulations or real
driving experiments on rough terrains. However,
these algorithms have physical limitations on real
applications of wheeled robots. First of all, the
vibration and current information is strongly
influenced by a robot speed and also a surface shape.
Therefore, although two robots move on the same
type of soil, it might indicate the result of identifying
one into another soil type depending on a robot
speed and a surface shape.
65
Kim J. and Lee J..
Soil Strength-based Estimation of Optimal Control Parameters for Wheeled Robots on Rough Terrain.
DOI: 10.5220/0005034900650073
In Proceedings of the 11th International Conference on Informatics in Control, Automation and Robotics (ICINCO-2014), pages 65-73
ISBN: 978-989-758-040-6
Copyright
c
2014 SCITEPRESS (Science and Technology Publications, Lda.)