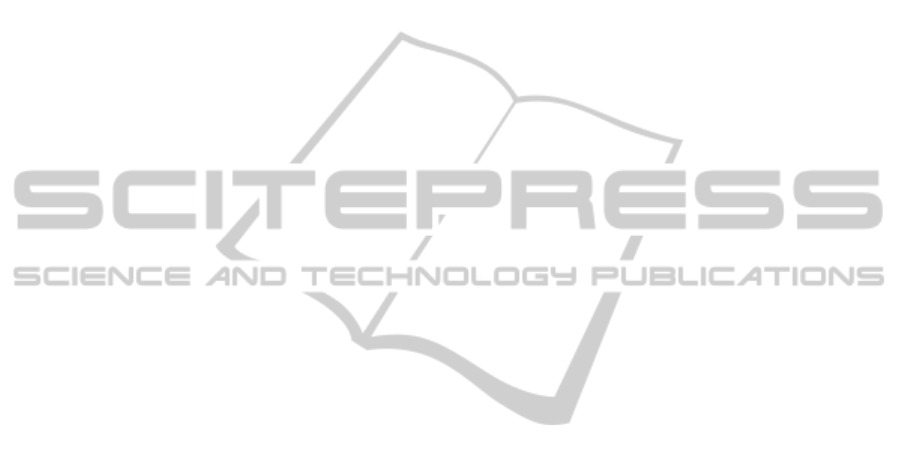
with flexibility capabilities under a number of
disrupting situations could be identified. The
identification of such components could lead to a
number of system configurations, especially able to
absorb the effects of several disturbances.
REFERENCES
Buffa, E. S., 1972, Operations Management: Problems
and models, New York, Wiley.
Chen, J. & Chen, F., 2003, Adaptive scheduling in random
flexible manufacturing systems subject to machine
breakdowns. International Journal of Production
Research, 41, 1927-1951.
Chung, C., 1996, Human issues influencing the successful
implementation of advanced manufacturing
technology. Journal of Engineering and Technology
Management, 13, 283-299.
Dimitrov, P., 1990, The impact of flexible manufacturing
systems (FMS) on inventories. Engineering Costs and
Production Economics, 19, 165-174.
Eckstein, A. & Rohleder, T., 1998, Incorporating human
resources in group technology/cellular manufacturing.
International Journal of Production Research, 36,
1199-1222.
Hillier, F. & So, K., 1991, The effect of Machine
breakdowns and interstage storage on the performance
of production line systems. International Journal of
Production Research, 29, 2043-2055.
Huselid, M. A., 1995, The impact of human-resource
management-practices on turnover, productivity, and
corporate financial performance. Academy of
Management Journal, 38, 635-672.
Hwang, S. L., Barfield, W., Chang, T. C. & Salvendy, G.,
1984, Integration of humans and computers in the
operation and control of flexible manufacturing
systems. International Journal of Production
Research, 22, 841-856.
Jayaram, J., Droge, C. & Vickery, S. K., 1999, The impact
of human resource management practices on
manufacturing performance. Journal of Operations
Management, 18, 1-20.
Kahn, J. A. & Lim, J. S., 1998, Skilled labor-augmenting
technical progress in US manufacturing. Quarterly
Journal of Economics, 113, 1281-1308.
Law, A. & Kelton, D., 2000, Simulation Modelling and
Analysis, Singapore, McGraw-Hill.
Liao, C. J. & Chen, W. J., 2004, Scheduling under
machine breakdown in a continuous process industry.
Computers and Operations Research, 31, 415-428.
Logendran, R. & Talkington, D., 1997, Analysis of
cellular and functional manufacturing systems in the
presence of machine breakdown. International Journal
of Production Economics, 53, 239-256.
Mason, R., Gunst, R. & Hess, J., 2003, Statistical design
and analysis of experiments, with applications to
engineering and science, New York, Wiley-
Interscience.
Montgomery, D. C., 2009, Design and analysis of
experiments, Hoboken, NJ, John Wiley & Sons.
Nihat, K., Haldun, A. & Anand, P., 2006, Minimizing
makespan on a single machine subject to random
breakdowns. Operations Research Letters, 34, 29-36.
Ounnar, F. & Ladet, P., 2004, Consideration of machine
breakdown in the control of flexible production
systems. International Journal of Computer Integrated
Manufacturing, 17, 69-82.
Ozmutlu, S. & Harmonosky, C., 2004, A real-time
methodology for minimizing mean flow time in FMSs
with machine breakdowns: threshold-based selective
rerouting. International Journal of Production
Research, 42, 4975-4491.
Pagell, M., Handfield, R. B. & Barber, A. E., 2000,
Effects of operational employee skills on advanced
manufacturing technology performance. Production
and Operations Management, 9, 222-238.
Robinson, S., 1994, Successful Simulation: A Practical
Approach to Simulation Projects, London, McGraw-
Hill.
Saad, S. & Gindy, N.,1998, Handling internal and external
disturbances in responsive manufacturing
environments. Journal of Production Planning and
Control, 9, 760-770.
Srinivasan, M. M. & Bozer, Y. A., 1992, Which one is
responsible for wip - the workstations or the material
handling-system. International Journal of Production
Research, 30, 1369-1399.
Taylor, B. & Clayton, E., 1982, Simulation of a
production line system with machine breakdowns
using network modeling. Computers and Operations
Research, 9, 255-264.
Udo, G. & Ebiefung, A., 1999, Human factors affecting
the success of advanced manufacturing systems.
Computers and Industrial Engineering, 37, 297-300.
Welch, P., 1983. “The statistical analysis of simulation
results.” In The computer modeling handbook, ed. S.
Lavenberg, 268-328. New York: Academic Press.
Williams, D. J., 1994, Manufacturing systems; an
introduction to the technologies, London, Chapman &
Hall.
SIMULTECH2014-4thInternationalConferenceonSimulationandModelingMethodologies,Technologiesand
Applications
384