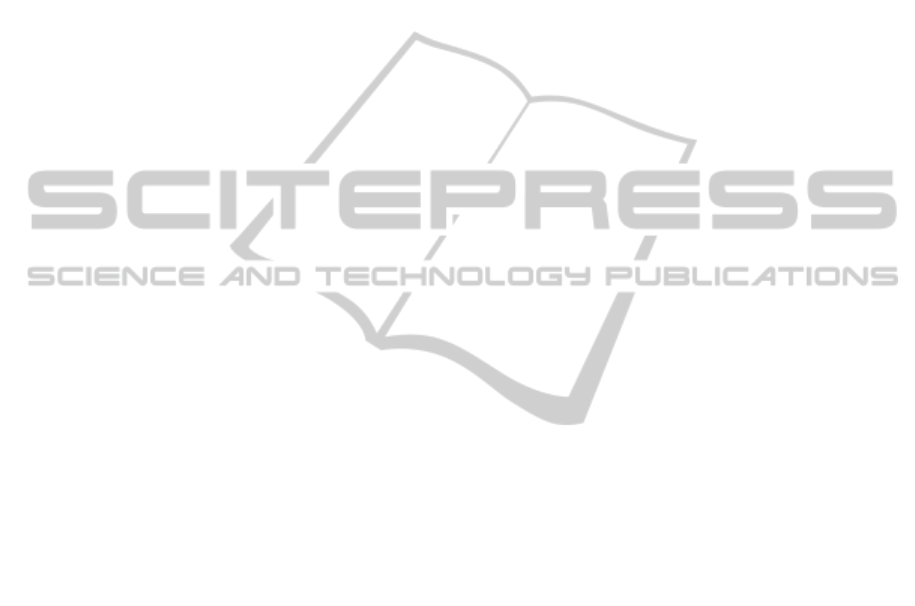
necessary during the simulation process. Further, the
Z-map can’t perform the drill function to remove
materials due to its algorithm limitation. The
Boolean operation is the only solution to simulate
drilling operation.
The difference set of Boolean can be used to
remove material from the original object.
Theoretically, Boolean operation can produce
precise machining results. However, its drawback is
that Boolean calculation needs higher computation
cost and will decrease performance during
simulation. In addition, coplanar contacts between
the cutter and work-piece are quite common during
the simulation. For the surface-based model
representation, coplanar issue is still a challenge.
8 CONCLUSIONS
The main contribution of this paper is the simulation
of turn-mill machining in 3D with accuracy and
efficiency. Triangular mesh model is used to
represent the cutter and work-piece, including
tooling turret and clamp. The advantage of turn-mill
machining is that it can shorten processing time,
increase productivity, reduce storage space, and
maintain accuracy. The turn-mill process is usually
complicated and involves multiple cutters and
spindles. The danger and cost of collision is high,
therefore accurate and efficient simulation of the
process becomes critical. To achieve this purpose
and balance between efficiency and precision, this
paper proposes a hybrid simulation method by
combining DIP, Z-map and Boolean operations. The
software will determine the appropriate material
removal method according to the NC instructions. In
the simulation processing, in order to check if the
path is correct or not, mesh collision detection
algorithm is used to find out interferences. For the
future work, first, this research will focus on the
improvement of Boolean operation. The efficiency
of Boolean operation is still a bottleneck of
simulation. In addition, the Boolean operators still
need to exclude some special cases such as coplanar
in advance to ensure the success of the simulation.
In the future, this work will also be extended to the
on-line turn-mill simulation/monitor by integrating
the simulation software with a PC-based controller.
REFERENCES
Kerning P., Yuanyuan, X., 2010, “Real-Time Boolean
Operation for NC Machining in Virtual Simulation”,
International Conference on Computer Application
and System Modeling.
Huang, Y. and Oliver, J. H., 1995, “Integrated Simulation,
Error Assessment, and Tool Path Correction for Five-
Axis NC Milling”, Journal of Manufacturing Systems.
Kim, Y. H. and Ko, S. L., 2006, “Improvement of Cutting
Simulation using the Octree Method”, The
International Journal of Advanced Manufacturing
Technology.
Jang, D., Kim, K. and Jung, J., 2000, “Voxel-based Virtual
Multi-axis Machining”, Advanced Manufacturing
Technology.
Chang, K. Y. and Goodman, E. D., 1991, “A Method for
NC Tool Path Interference Detection for A Multi-Axis
Milling System”, ASME Control of Manufacturing
Process.
Lee, S. K. and Ko, S. L., 2002, “Development of
Simulation System for Machining Process using
Enhanced Z Map Model”, Journal of Materials
Processing Technology.
Maeng, S. R., Baek, N., Shin, S. Y., and Choi, B. K., 2003,
“A Z-map Update Method for Linearly Moving Tools”,
Computer-Aided Design.
Maeng, S. R., Baek, N., Shin, S. Y., and Choi, B. K., 2004,
“A fast NC Simulation Method for Circularly Moving
Tools in the Z-map Environment”, Proceedings of the
Geometric Modeling and Processing 04.
Cai, Y., Zhen, L. and Xin, P., 2010, “A Geometrical
Simulation of Ball End Finish Milling Process and Its
Application for the Prediction of Surface Topography”,
Mechanic Automation and Control Engineering.
Tsai, J. P., 2013, “A Modified Z-map Computational
Interpolation Algorithm for Surface Machining
Simulation”, Transactions of the Canadian Society for
Mechanical Engineering.
Tayebi, A, G´omez, P. J, Gonz´alez, D. I, Catedra, F.,
2011, “Boolean Operations Implementation over 3D
Parametric Surfaces to be Included in the Geometrical
module of an Electromagnetic Solver”, Proceedings of
the 5th European Conference on Antennas and
Propagation.
Mei, G. and Tipper, C., 2013, “Simple and Robust
Boolean Operations for Triangulated Surfaces”,
Computational Geometry.
Wang, C. L., 2011, “Approximate Boolean Operations on
Large Polyhedral Solids with Partial Mesh
Reconstruction”, IEEE Transactions on visualization
and computer graphics.
Reqiuicha, A. G., and Voelcker, B., 1985, “Boolean
Operations in Solid Modeling: Boundary Evaluation
and Merging Algorithms”, Proceedings of the IEEE.
Chan, C. K., 2003, “Minimum bounding boxes and
volume decomposition of CAD models”.
Hutter, M. and Fuhrmann, A., 2007, “Optimized
Continuous Collision Detection for Deformable
Triangle Meshes”, Fifth International Conference on
Computer Graphics and Computer Vision.
Curtis, S., Tamstorf, R. and Manocha, D., 2008, “Fast
Collision Detection for Deformable Models using
Representative Triangles”,
ACM I3D.
SIMULTECH2014-4thInternationalConferenceonSimulationandModelingMethodologies,Technologiesand
Applications
724