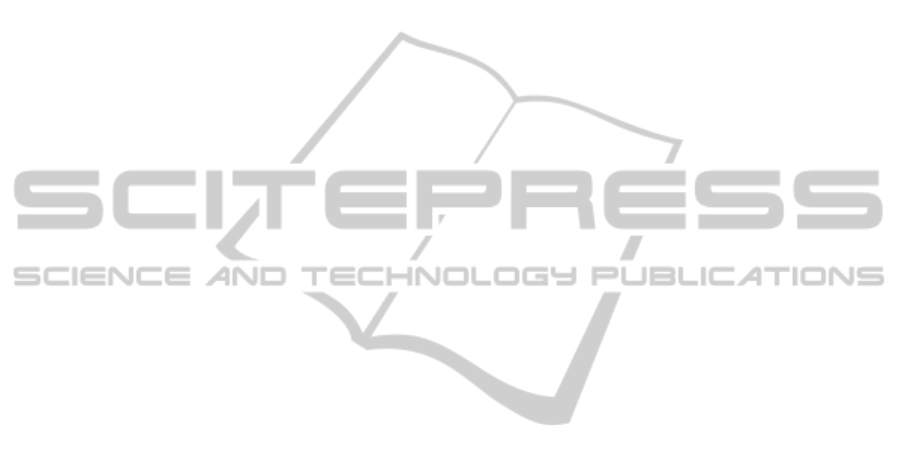
REFERENCES
Åström K. J., Hägglund T., 1995. PID controllers: theory,
design and tuning. Instrument Society of America.
Åström K.J., Hägglund T., 2000. Benchmark Systems for
PID Control. IFAC Workshop on Digital Control --
Past, present, and future of PID Control. Spain.
Bohl A. H., McAvoy T. J., 1976. Linear Feedback vs.
Time Optima Control. II. The Regulator Problem.
Industrial & Engineering Chemistry Process Design
and Development, 15(1), 30-33.
Chang W. D., Yan J. J., 2004. Optimum setting of PID
controllers based on using evolutionary programming
algorithm. Journal of the Chinese Institute of
Engineers, 27(3), 439-442.
Desanti J., 2004. Robustness of tuning methods of based
on models of first-order plus dead time PI and PID
controllers (in Spanish). Escuela de Ingeniería
Eléctrica, Universidad de Costa Rica.
Fleming P. J., Purshouse R. C., 2002. Evolutionary
algorithms in control systems engineering: a survey.
Control Engineering Practice, 10(11), 1223-1241.
Hassan G. A., 1993. Computer-aided tuning of analog and
digital controllers. Control and Computers, 21, 1-1.
Hansen N. (2006). The CMA Evolution Strategy. In:
Towards a new evolutionary computation. Lozano,
Larrañaga, Inza, Bengoetxea, Heidelberg, Springer.
Hernández J. A., Ospina J. D., 2010. A multi dynamics
algorithm for global optimization. Mathematical and
Computer Modelling, 52(7), 1271-1278.
Hernández-Riveros Jesús-Antonio, Villada-Cano Daniel.,
2012. Sensitivity Analysis of an Autonomous
Evolutionary Algorithm. Lecture Notes in Computer
Science. Volume 763. Advances in Artificial
Intelligence. Springer.
Hernández-Riveros J., Arboleda-Gómez A., 2013. Multi-
criteria decision and multi-objective optimization for
constructing and selecting models for systems
identification. Trans.Modelling and Simulation, 55.
Herreros A., Baeyens E., Perán J. R., 2002. Design of
PID-type controllers using multiobjective genetic
algorithms. ISA transactions, 41(4), 457-472.
Iruthayarajan M. W., Baskar S., 2009. Evolutionary
algorithms based design of multivariable PID
controller. Expert systems with Applications, 36(5).
Junli L., Jianlin M.. Guanghui Z., 2011. Evolutionary
algorithms based parameters tuning of PID controller.
Control and Decision Conference, IEEE. 416-420.
Lagunas J. 2004. Tuning of PID controllers using a multi-
objective genetic algorithm, (NSGA-II). (in Spanish)
(Doctoral dissertation) Departamento de Control
Automático. Centro de Investigación y de Estudios
Avanzados. México.
Li, Y., Ang, K.H., Chong, G.C., 2006. PID control system
analysis and design. IEEE Control Systems Magazine
26(1), 32-41.
Liu G. P., Daley S., 2001. Optimal-tuning PID control for
industrial systems. Control Engineering Practice,
9(11), 1185-1194.
Lozano J. A., Larrañaga P., Inza I., Bengoetxea E. (Eds.).
2006. Towards a new evolutionary computation:
Advances on estimation of distribution algorithms.
Springer.
Michail, K., Zolotas, A.C., Goodall, R.M., Whidborne,
J.F., 2012. Optimised configuration of sensors for fault
tolerant control of an electro-magnetic suspension
system, International Journal of Systems Science, 43
(10), 1785-1804.
Montgomery D. C., 2008. Introduction to statistical
quality control. John Wiley & Sons. Wiley, New York.
Mora J. 2004. Performance and robustness of the methods
based on second order models plus dead time tuning
PID controllers. (in Spanish). Escuela de Ingeniería
Eléctrica, Universidad de Costa Rica.
Dwyer A., 2009. Handbook of PI and PID controller
tuning rules (Vol. 2). London: Imperial College Press.
Saad M. S., Jamaluddin H., Darus I. Z. M., 2012a. PID
Controller Tuning Using Evolutionary Algorithms.
WSEAS Transactions on Systems and Control. Issue 4.
Saad M. S., Jamaluddin H., Darus I. Z. M., 2012b.
Implementation of PID controller tuning using
differential evolution and genetic algorithms. Int.
Journal of Innovative Computing Information and
Control, 8(11), 7761-7779.
Skolicki Z., De Jong K., 2005. The influence of migration
sizes and intervals on island models. Proceedings of
the conference on Genetic and evolutionary
computation ACM. 1295-1302.
Solera Saborío E. 2005. PI / PID Controller Tuning with
IAE and ITAE criteria for double pole plants. (in
Spanish). Escuela de Ingeniería Eléctrica, Universidad
de Costa Rica.
Sung S. W., Lee O, J., Lee I. B., Yi S. H. 1996. Automatic
Tuning of PID Controller Using Second-Order Plus
Time Delay Model. Journal of chemical engineering of
Japan, 29(6), 990-999.
Tavakoli S., Griffin I., Fleming P. J., 2007. Multi-
objective optimization approach to the PI tuning
problem. Evolutionary Computation Congress. IEEE.
3165-3171.
Vinter, R., 2000. Optimal Control. Systems & Control:
Foundations & Applications. Springer, London.
Whitley Darrell., 2001. An overview of evolutionary
algorithms: practical issues and common pitfalls.
Information and Software Technology. 43(14).
Xinjie Yu, Mitsuo Gen., 2010. Introduction to
Evolutionary Algorithms. Springer, London.
ECTA2014-InternationalConferenceonEvolutionaryComputationTheoryandApplications
20