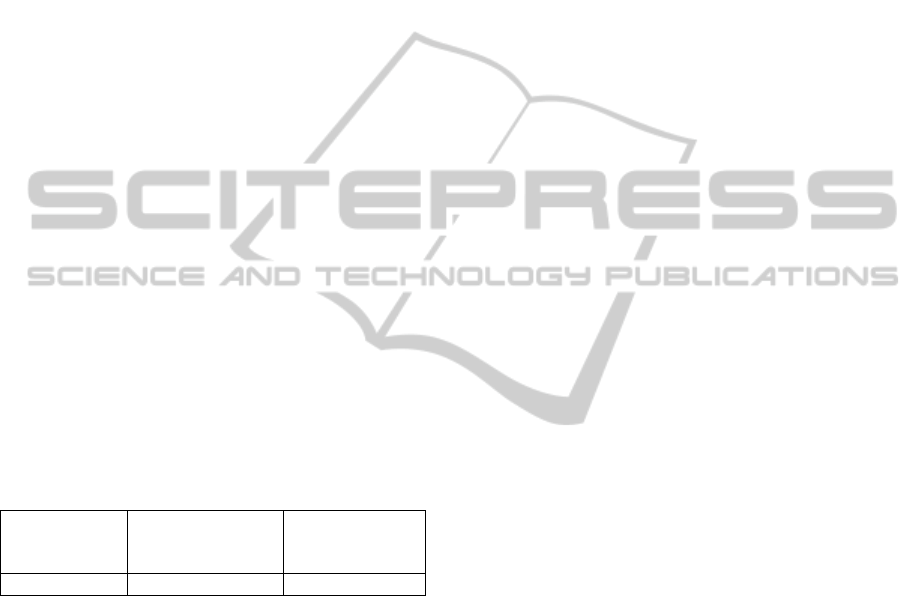
The object manipulation has been conducted
using a custom parallel gripper capable of sensing
grasp force, and also tangential force and slippage in
the vertical direction. A rectangular aluminium
object of 100x50x22mm and weighing
approximately 300 grams has been grasped, lifted
vertically and moved to a new location at a
maximum acceleration of 100mm/sec and a
maximum speed of 300mm/sec.
The experiments conducted demonstrate that
using sensor fusion to monitor proximity to slippage
and using equations 1 and 3 to adjust grasp force
safety margin allows the controller to predict and
prevent object slippage more reliably.
A summary of the experimentation results is
presented in Table 1. All object manipulation
attempts were performed on the same object, using
the same acceleration, velocity and deceleration for
all manipulation attempts.
As a result of replacing the slow vision feedback
used in the previous version of the sensor fusion
function with tangential force feedback, the
improved slippage detection function gained
slippage detection speed and the ability to predict
proximity to slippage. In most circumstances the
vision feedback was either to slow or unconvincing.
The overall performance gain is evident from the
Table 1 results.
Table 1: Slippage prevention ability comparison of
previous and current slippage detection methods when
manipulating a novel object.
Number of
object lifting
attempts
Unpredicted
slippage using
previous method
Unpredicted
slippage using
current method
10 6 1
4 CONCLUSIONS
This paper presented the redevelopped manipulation
controller framework and the additional benefits that
the elimination of unnecessary control functions,
data processing and interaction redundancies bring
to safe and reliable object grasping and
manipulation. In particular the sensor fusion
function enhancements and the use of equations 1
and 3 to control grasp force safety margin resulted in
improved controller ability to predict, detect and
control object slippage in the robot gripper.
A practical method of estimating the static
coefficient of friction (using equation 2) during
object manipulation based on feedback from the
grasp force sensor and slippage sensor was
presented.
The manipulation controller framework
presented here could be used equally well with
Cartesian and articulated robots, because the motion
controller provides the target coordinates, force and
speed information, while the robot controller tells
the robot how to get there. This means that the
manipulation controller framework can work with
any robot controller that understands the motion,
force and speed commands received from the motion
controller module.
It is envisaged that this work will be useful to
researchers developing object manipulation
controller frameworks and slippage detection and
control strategies.
REFERENCES
Dzitac, P., Mazid, A. M., 2012. Modelling of a Grasping
and Manipulation Controller. In Proceedings
(Volume 2), ICINCO 2012 – 9th International
Conference on Informatics in Control, Automation and
Robotics, Rome, Italy, pp. 199 -204.
Howard, A. H., Bekey, G., 2000, Intelligent Learning for
Deformable Object Manipulation. In Journal of
Autonomous Robots, vol. 9, pp. 51-58.
Khalil, F. F., Payeur, P., 2007. Robotic Interaction with
Deformable Objects under Vision and Tactile
Guidance - a Review. In International Workshop on
Robotic and Sensors Environments, pp.1-6.
Prats, M., Sanz, P. J., del Pobil, P. A., 2009. Vision-
tactile-force integration and robot physical interaction.
In Conference on Robotics and Automation, 2009.
ICRA '09. IEEE International, pp. 3975-3980.
Wettels, N., Parnandi, A. R., Moon, J. H., Loeb, G. E.,
Sukhatme, G.S., 2009. Grip control using biomimetic
tactile sensing systems. In IEEE/ASME Transactions
on Mechatronics, vol. 14, pp. 718–723.
Smith, S., 1999, The Scientist and Engineer's Guide
to Digital Signal Processing 2nd Ed., California
Technical Publishing, San Diego, California.
Dzitac, P., Mazid, A. M., 2012, A method to control grip
force and slippage for robotic object grasping and
manipulation. In The Proceedings, 20
th
Mediterranean
Conference on Control and Automation, Barcelona,
Spain, pp. 116-121.
RoboticGraspingandManipulationControllerFramework-ArchitectureRedevelopment
373