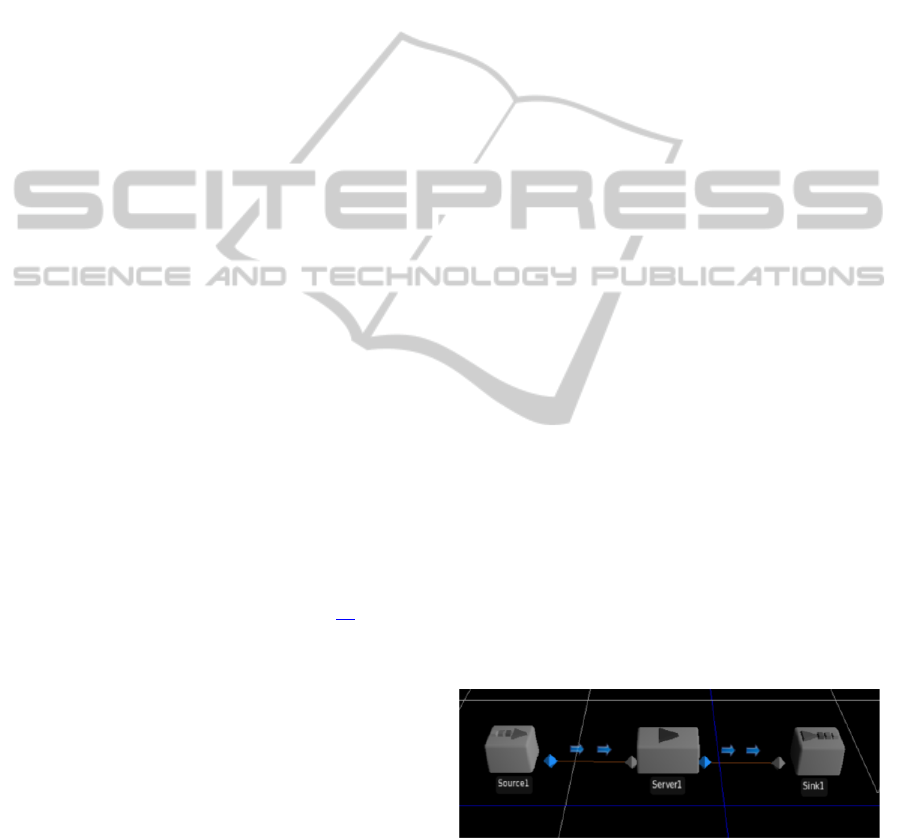
line, emulation of a new control system or
redesigning the entire production chain. The “best
guess” is usually a poor substitute for an objective
analysis, while now we can accurately predict
system behavior under different conditions and
reduce the risk of a bad decision.
Moreover, here the prediction of variability of
the process is important. A quick analysis cannot
capture the dynamic aspects of the system and issues
that can have a significant impact on system
performance. Through simulation we can be
provided with a better understanding of how
different parts interact and how they affect the
overall system performance.
Finally, with the modeled developed we are
given the capability of communicating ideas. We
can help partners, customers, employees or investors
to better understand the system. The modern 3D
modeling promotes communication and
understanding to a wide audience.
1.2 SIMIO Simulation Software
SIMIO is a SImulation Modeling framework based
on Intelligent Objects. It is a modeling tool that
combines the simplicity of objects with the
flexibility of procedures for the provision of a rapid
modeling without requiring programming (Oba et
al., 2014). It can be used to predict and improve the
performance of dynamic, complex systems (Pegden,
2014). The software prototypes and displays a three-
dimensional illustration of the behavior of the
system over time. Although simulation and
visualization tools have existed for many years,
SIMIO makes modeling extremely easy by
providing a new object-oriented approach. One can
select (http://www.simio.com/index.html) objects
from libraries and place graphics in the model.
Objects represent the physical components of the
system, such as tiles, conveyors, wagons etc. One
aspect that is often overlooked in the analysis of
systems performance is the role that randomness
plays in determining the behavior of the system. By
randomness we mean the idea that things that
happen in our system occur with some differences
from one another. Classic examples of randomness
are: the time between the arrival of a system entity
until the arrival of the next, the time between
failures of equipment or the time it takes to complete
an activity. If we want to understand and improve
our system we need to model accurately the
variations relevant to the randomness in the system.
In the model developed, the randomness factor was
implemented for the production line preceding the
furnace. The model of the furnace itself is
deterministic, as is the actual system due to control
techniques applied.
Consider a SIMIO model for a very simple
system in which entities arrive, processed by a
server, and then depart from the system. For this
simple example in which the system makes use of a
source, a server, a draw and a route from the library,
the SIMIO model is shown in Figure 1. The entities
entering the system from the source move to the
server where they are processed one by one and then
go to the draw where they leave the system.
The rate at which the source creates entities and
the processing time in the server are adjusted from
the user to the properties of the corresponding object
and the aforementioned factor of randomness can be
included (SIMIO LLC Documentation, 2011).
1.3 Overview of the Industrial, Large
Scale, Ceramics Furnace
The furnace, with which we deal, is of the
continuous, propulsion type. There are two gates,
one entrance and one exit and the tiles are baked
while moving inside the oven. In fact every time a
new wagon of tiles enters, all wagons move forward
to the next position, while the last wagon leaves the
oven. The oven has a length of 90 meters and 33
wagon positions. In normal operation, the input rate
of the heat is stable and the burners are rarely turned
off. Three distinct zones along the oven are formed.
First is the preheating zone starting from the first
wagon until the 7th. Second is the fire zone from the
8th until the 18th wagon and third is the cooling
zone from the 19th until the 33th wagon. The
thermal energy flow inside the furnace is subject to
extensive thermal analysis (Warren et al., 2000). In
Figure 2, the temperature curve throughout the
length of the oven is presented.
Figure 1: Simple SIMIO model.
2 MODELING APPROACH OF
THE FURNACE OPERATION
Each wagon is modeled as an entity carrying the
3DSimulationofIndustrialLarge-scaleCeramicsFurnaceinSIMIOPlatformEnvironment
717