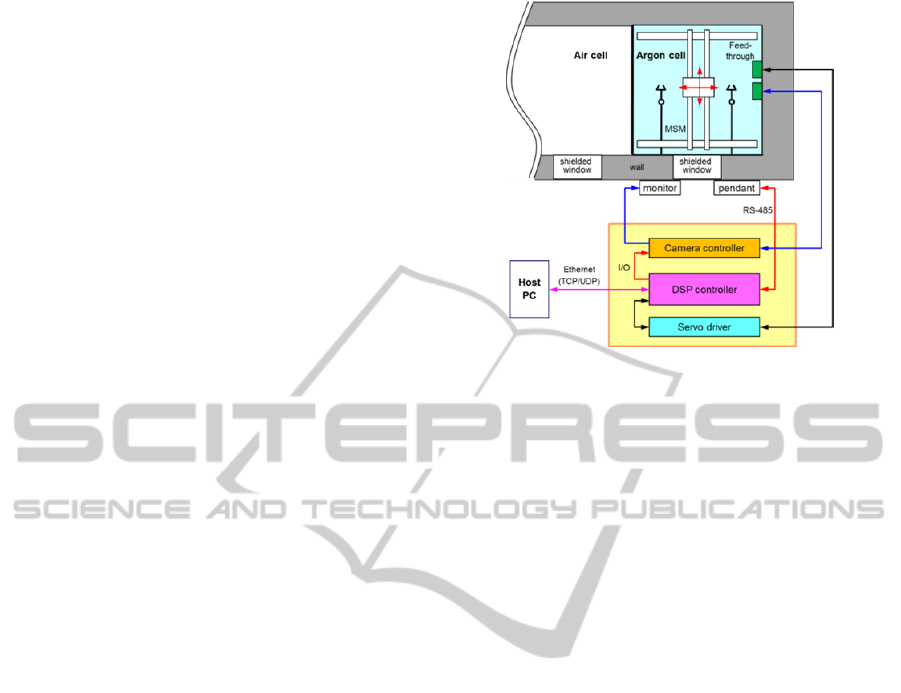
4 CONTROL SYSTEM
OF CRANE
Manual operation of a crane while watching inside
the hot-cell through a lead-glass shielding window
often fails in accomplishing the given tasks due to an
imprecise operator cognition. In addition, because
the location of the processing equipment is known to
be a priori in an argon compartment, predefined
sequential operations can simplify the complicated
operation. Therefore, we designed a remote control
system based on absolute positioning and automatic
operation to provide a safer and more efficient
operation of the processing equipment. The crane
has 3 degrees of freedom actuated with Tamagawa
brushless servo motors equipped with a resolver
sensor. We designed a control system on the basis of
the servo control. The absolute position of each
motion axis can be measured using a wire sensor in
which a multi-turn potentiometer is coupled with a
steel wire.
To increase the performance of the absolute
positioning measurement, we used a combination of
a wire sensor and resolver pulse reading. When the
control system is re-initialized, it reads the absolute
position from the wire sensor through an analog-to-
digital conversion, and set the value as the initial
position of the crane system. Next, the motion
control system uses resolver pulse readings instead
of wire sensor readings because the resolver pulse is
much more robust against noise. Since the analog
readings from a wire sensor are normally affected by
noise, the average value of the preset time duration
is chosen as the initial value. In addition, whenever
the limit switch is activated, the control system
resets the origin as the preset value in absolute
Cartesian coordinates. This makes it possible for the
control system to be operated in absolute positioning
mode.
Figure 7 shows the overall layout of the control
system in which a digital signal processor (DSP)-
based controller interfaces with both the camera
controller and motion controller. Servo motors are
operated in position control mode with various speed
profiles. The DSP controller receives control
parameters from the PC through network
communication, and transfers operational
information to the PC. The operator can manipulate
the crane system by looking through the lead-glass
shielding window and viewing a supplementary
camera monitor. All functions concerning the
control of the crane and camera are interfaced with a
touch pendant through RS-485 communication.
Figure 7: Overall layout of the integrated control system.
5 PROTOTYPE OF CRANE
SYSTEM
Figure 8 shows a full-scale evaluation mock-up
facility that provides same operation conditions and
useful means for testing and verifying the remote
operability and maintainability of the constructed
process equipment, cell utilities, and relevant
devices in advance before they are installed in the
argon compartment of the ACPF. Cell utilities
consisting of a window, a cell light, an antechamber
for transportation, a door, two sets of MSMs, a feed-
through, and a camera system were installed inside
the argon compartment, while a camera monitor and
touch pendant for crane control were installed
around the window in the operation area. Several
mechanical and electrical tests were performed to
check whether the crane system is performing to the
desired level of performance. The maximum
deflection of the girder frame is about 0.3 mm,
which may not influence the performance of the
linear motion system, such as the ball screw and ball
spline. Because the mechanical parts of the crane
system were placed over the MSM, the load hook
can be moved along the ceiling without any
interference with the MSMs. Several control modes
such as jog mode, absolute positioning mode, and
sequential operation mode can be selectively
performed using a touch pendant in which several
graphic pages linked to each control mode.
As shown in Fig. 9, several remote maintenance
operations have been performed to verify that the
driving modules and sensor modules can be replaced
using an MSM only. From the experimental results,
all the design goals have been generally achieved,
ICINCO2014-11thInternationalConferenceonInformaticsinControl,AutomationandRobotics
394