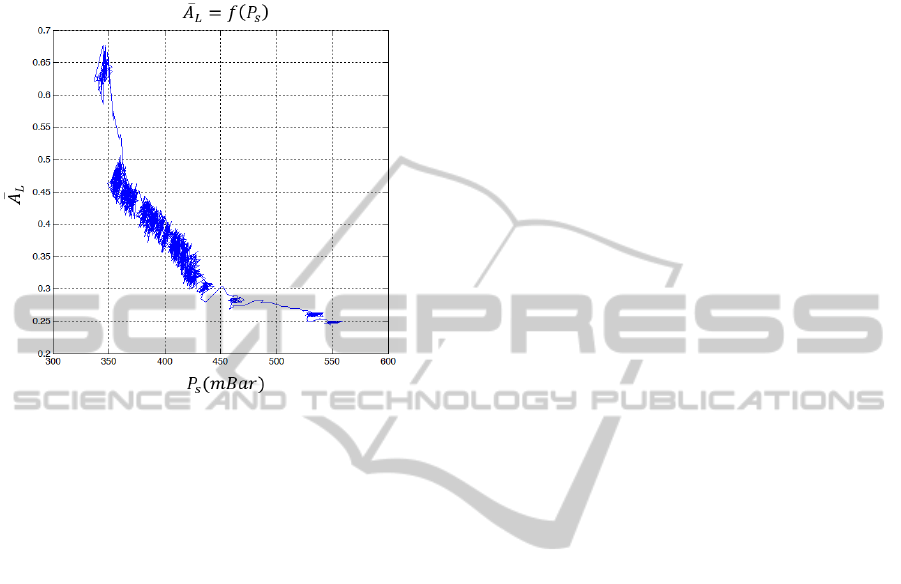
steady-state. As it can be seen in the figure, the
concentration of the points are around knee of the
curve which is a testimony to the analysis given in
section 3.1.
Figure 9: Identification data of the seal behaviour under
the condition of stable chamber pressure.
5 CONCLUSION
This paper reports the design procedure of a
nonlinear controller for the chamber pressure of the
climbing robot CREA. The controller not only
moves toward a stable attraction region but also
satisfy rigorous conditions of safety. In previous
works the safety issue is included in the path
planning high level control which administrates the
overall behaviour of several chambers and decides
according to the predefined safety measures. Many
parameters are defined for safety measures and the
response of the system is slow since the process is
high level. In this paper we incorporated reactional
safety features directly into the stability of the
system. Important feature of the system is that the
equilibrium of the controller is dependent on the
environment (wall surface). The controller observes
and interacts with environment to determine the
equilibrium and then moves towards the attraction
region. If the controller could not find equilibrium, it
will continue to search without putting robot at risk.
Its response is reactional and fast especially in risky
situations to guarantee safety. The controller is very
simple to implement in low level DSP to increase
the sampling rate. It also considerably reduces the
burden on high level planner since the control
strategy is designed in a way that the chambers work
highly distributive.
However, there are some open questions that need to
be investigated. One is the assumption of the
function
. This assumption is valid in
working on common concrete walls but there are
some specific situations like the existence of
relatively big steps on the wall that have different
leakage profile. In this cases high level planner
should be involved in overall decision making
process. We are also working on a better design for
seal to improve the behaviour of the sealing process.
It is also desirable to develop estimation and
learning methods for friction, force and coordination
of different chambers because of the strong coupling
with environment.
REFERENCES
Schmidt, D., Berns, K., 2013. Climbing robots for
maintenance and inspections of vertical structures—A
survey of design aspects and technologies. In Robotics
and Autonomous Systems, volume 61, issue 12, Pages
1288-1305.
Longo, D., Muscato, G., 2006. The Alicia
3
climbing robot:
a three-module robot for automatic wall inspection. In
Robotics & Automation Magazine, volume 13, issue 1,
pages 42-50.
Morris, W., Xiao, J., 2008. City-Climber: Development of
a Novel Wall-climbing Robot, In Journal of Student
research, volume 1.
Wettach, J., Hillenbrand, C., Berns, K., 2005.
Thermodynamical Modelling and Control of an
Adhesion System for a Climbing Robot, In IEEE
International Conference on Robotics and Automation
(ICRA), Barcelona, Spain.
Schmidt, D., 2013. Safe Navigation of a Wall-Climbing
Robot-Risk Assessment and Control Methods. The
doctrol thesis, University of Kaiserslautern, Germany,
(verlag Dr. Hut, Munich Germany 2013).
Kopietz, K., Schmidt, D., Schütz, S., Berns, K., 2014.
Friction Optimization Adhesion Control of a Wheel-
Driven Wall-Climbing Robot. In Proceedings of
International Conference of Climbing and Walking
Robots (CLAWAR).
Khalil, H., 1996. Nonlinear Systems, The book, Prentice
Hall, Englewood Cliffs, NJ, 2
nd
edition.
DesignofSafeReactionalControllerforChamberPressureinClimbingRobotCREA
89