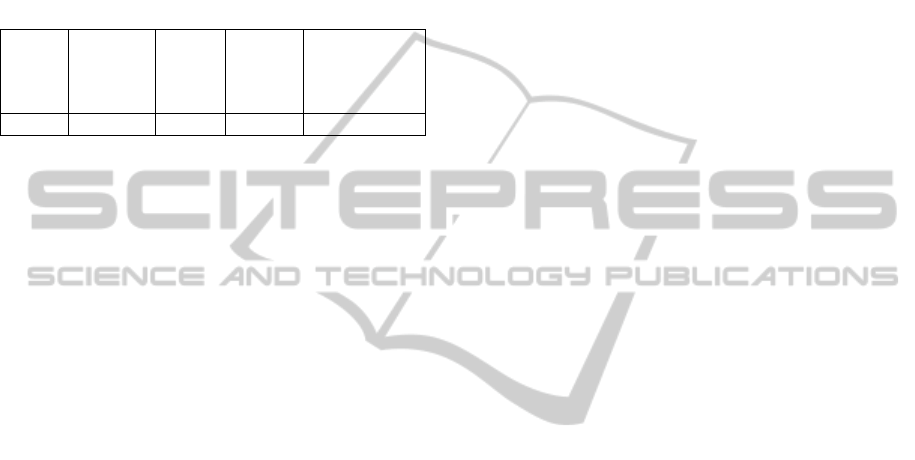
Five samples of pull forces necessary to cause disk
slippage in gripper jaws with pads were averaged
and recorded in Table 2.
The additional pull force required to cause disk
slippage is significantly larger, which confirms that
jaws with discrete peripheral pads result in a larger
effective torque radius r
e
than flat jaws without
peripheral pads.
Table 2: Effective torque radius experiment – long flat
gripper jaws with pads.
Jaw
length
(mm)
Effective
radius
(mm)
Force
applic.
radius
(mm)
Clamp
force
(N)
Average slip
force (N)
80 30 43 70 16.9
Just like in the previous experiments, the
experimentation carried out here is not aimed at high
accuracy results but rather to highlight the difference
in the effective torque radius of jaws with pads
compared to jaws without pads.
4 CONCLUSION AND FUTURE
WORK
While performing object grasping and manipulation
experiments it was noticed that object manipulation
reliability was influenced significantly by the ability
of a parallel gripper to develop optimum reaction
forces at all grasp points. It was found that this
ability was dependent on the ability to resist object
rotation in the gripper, which in turn was dependent
on the gripper design and the locations of grasp
points on the grasped object.
Equal load sharing by all grasp points resulted in
higher resistance to slippage. When one grasp point
was holding a higher share of the load it was more
likely to slip during manipulation.
A modified gripper jaw design and grasping
strategy that together offered a higher resistance to
object rotation in the gripper and minimised the
required grasp forces was also proposed.
It is believed that the concept of effective torque
radius presented here can be extrapolated to other
gripper types and grasping strategies to improve
their reliability and effectiveness.
The concepts in this paper are applicable to most
object grasping devices that create contact points
with the object, including multi-finger humanoid
hands.
Future work can be done to develop designs and
grasping strategies for multi-finger robotic grasping
devices that would increase their resistance to object
rotation and therefore minimise the effect of
torsional forces at the object-gripper interface that
contribute to object slippage.
REFERENCES
Chinellato, E., Morales, A., Fisher, R.B., del Pobil, A.P.,
2004. Visual quality measures for characterizing
planar robot grasps. In IEEE Trans. Systems, Man and
Cybernetics - Part C: Applications and Reviews, pp.
30–41.
Morales, A., Chinellato, E., Fagg, A.H., del Pobil, A.,
2004. Using experience for assessing grasp reliability.
In International Journal of Humanoid Robotics, vol. 1,
no. 4, pp. 671–691.
Flanagan, J.R., King, S., Wolpert, D.M., Johansson, R.S.,
2001, Sensorimotor prediction and memory in object
manipulation. In Canadian Journal of Experimental
Psychology, no. 55, vol. 2, pp. 87 - 95.
Diankov, R., Kanade, T., Kuffner, J., 2009. Integrating
grasp planning and visual feedback for reliable
manipulation. In IEEE/RAS International Conference
on Humanoid Robots (Humanoids), pp. 646–652.
Ciocarlie, M., Hsiao, K., Jones, E. G., Chitta, S., Rusu, R.
B., Sucan, I. A., 2010, Towards reliable grasping and
manipulation in household environments. In
International Symposium on Experimental Robotics,
New Delhi, India, pp. 241-252.
Dzitac, P., Mazid, A. M., 2013. Factors that influence
reliable object manipulation. In Proceedings of the
IEEE Industrial Electronics and Applications
International Conference (ICIEA), Melbourne,
Australia, pp. 1468-1473.
Budynas R. G., Nisbett, J.K., 2006. Shigley's Mechanical
Engineering Design (8th Ed.), McGraw-Hill, pp. 826-
829.
TheEffectiveRadiusandResistancetoSlippage
401