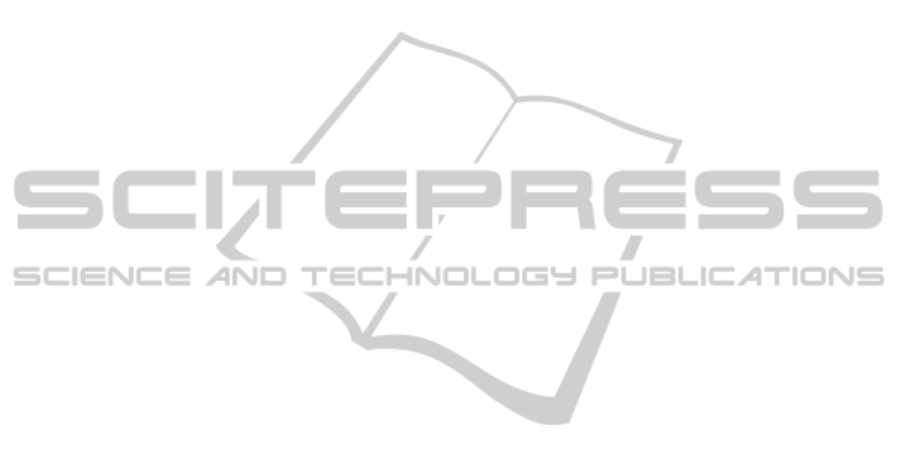
5 CONCLUSIONS
A coloured Petri net model of a distribution ware-
house, in which AGVs move pallets and rolls from the
storage area to the gates of the warehouse, has been
described in this paper. The AGV system is open path
and the proposed CPN model is able to represent the
behaviour of a variable number of AGVs which freely
travel on the system layout. To ensure safety, the pro-
posed CPN model includes colours, guards and arc
expressions which constrain each AGV to be at least
0.8-1 meter distant from any other AGV.
This CPN model has been also used to build
a discrete-event simulator of the distribution ware-
house. Such a simulator, implemented in Extend-
Sim, is currently used to test a scheduling procedure
(based on the solution of some mathematical pro-
gramming problems and a heuristic algorithm) aimed
at assigning the AGVs to the trucks which arrive at the
warehouse and sequencing transportation tasks on the
AGVs. Moreover, the use of the proposed CPN model
for determining the actual paths that the AGVs have
to be follow to minimize travel times and to reduce in-
teractions with other AGVs is currently investigated.
ACKNOWLEDGEMENTS
This work has been supported by A.I.R.O.N.E.
project funded by European Union and Regione Lig-
uria (Italy) under POR-FESR 2007/2013. Special
thanks to the partners of the project: Softeco Sismat
SpA, Sogegross SpA, and Genova Robot Srl.
REFERENCES
Aized, T. (2009). Modelling and performance maximization
of an integrated automated guided vehicle system us-
ing coloured Petri net and response surface methods.
Computers and Industrial Engineering, 57(3):822–
831.
Ajmone Marsan, M., Conte, G., and Balbo, G. (1984). A
class of Generalized Stochastic Petri Nets for the per-
formance evaluation of multiprocessor systems. ACM
Transactions on Computer Systems, 2(2):93–122.
Castillo, I., Reyes, S. A., and Peters, B. A. (2001). Model-
ing and analysis of tandem AGV systems using gener-
alized stochastic Petri nets. Journal of Manufacturing
Systems, 20(4):236–249.
Dotoli, M. and Fanti, M. (2004). Coloured timed Petri net
model for real-time control of automated guided vehi-
cle systems. International Journal of Production Re-
search, 42(9):1787–1814.
Duinkerken, M. B., ter Hoeven, T., and Lodewijks, G.
(2006). Simulating the operational control of free
ranging AGVs. In Perrone, L. F., Wieland, F. P., Liu,
J., Lawson, B. G., Nicol, D. M., and Fujimoto, R. M.,
editors, Proceedings of the 2006 Winter Simulation
Conference, pages 1515–1522.
Holloway, L. E. and Krogh, B. H. (1990). Synthesis of feed-
back control logic for a class of controlled Petri nets.
IEEE Transactions on Automatic Control, 35(5):514–
523.
Hsieh, S. (1998). Synthesis of AGVS by coloured-timed
Petri nets. International Journal of Computer Inte-
grated Manufacturing, 11(4):334–346.
Hsieh, S. and Chen, Y.-F. (1999). AgvSimNet: A
Petri-net-based AGVS simulation system. Interna-
tional Journal of Advanced Manufacturing Technol-
ogy, 15(11):851–861.
Jensen, K. and Kristensen, L. M. (2009). Coloured Petri
Nets. Springer.
Le-Ahn, T. and De Koster, M. B. M. (2006). A review of de-
sign and control of automated guided vehicle systems.
European Journal of Operational Research, 171:1–
23.
Lee, D. Y. and DiCesare, F. (1994). Integrated schedul-
ing of flexible manufacturing systems employing au-
tomated guided vehicles. IEEE Transactions on In-
dustrial Electronics, 41(6):602–610.
Mart´ınez-Barber´a, H. and Herrero-P´erez, D. (2010). Au-
tonomous navigation of an automated guided vehicle
in industrial environments. Robotics and Computer-
Integrated Manufacturing, 26:296–311.
Murata, T. (1989). Petri Nets: Properties, analysis and ap-
plications. Proceedings of the IEEE, 77(4):541–580.
Nishi, T. and Maeno, R. (2010). Petri net decomposition
approach to optimization of route planning problems
for AGV systems. IEEE Transactions on Automation
Science and Engineering, 7(3):523–537.
Nishi, T. and Tanaka, Y. (2012). Petri net decomposition
approach for dispatching and conflict-free routing of
bidirectional automated guided vehicle systems. IEEE
Transactions on Systems, Man, and Cybernetics Part
A:Systems and Humans, 42(5):1230–1243.
Petri, C. A. (1962). Kommunikation mit Automaten. Bonn:
Institut f¨ur Instrumentelle Mathematik, Schriften des
IIM Nr. 2.
Seelinger, M. and Yoder, J.-D. (2006). Automatic visual
guidance of a forklift engaging a pallet. Robotics and
Autonomous Systems, 54:1026–1038.
Sen, A., Wang, C., Ristic, M., and Besant, C. (1991). The
supervisory system of the imperial college free rang-
ing automated guided vehicle project. In Proceedings
of the 1991 IEEE International Conference on Sys-
tems, Man, and Cybernetics, pages 1017–1022.
Vis, I. F. A. (2006). Survey of research in the design and
control of automated guided vehicle systems. Euro-
pean Journal of Operational Research, 170:677–709.
Wu, N. and Zhou, M. (2005). Modeling and deadlock avoid-
ance of automated manufacturing systems with multi-
ple automated guided vehicles. IEEE Transactions on
Systems, Man, and Cybernetics, Part B: Cybernetics,
35(6):1193–1202.
APetriNetModelforanOpenPathMulti-AGVSystem
745