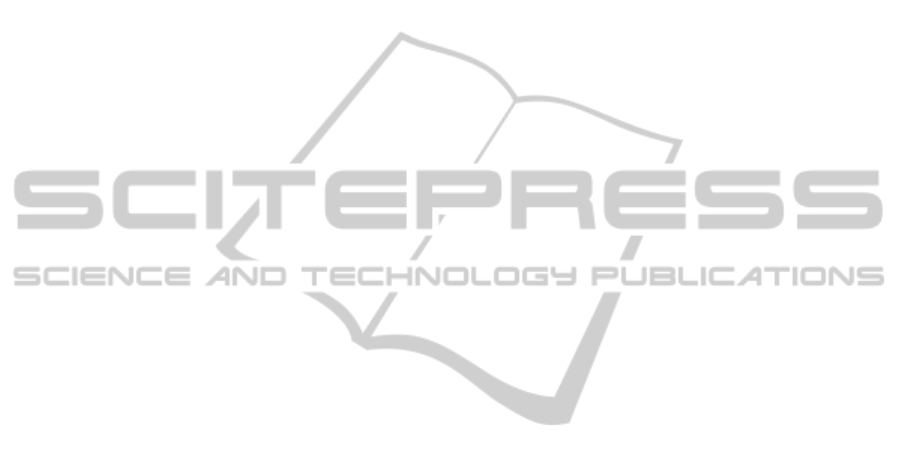
program-based and model-based design, for the de-
velopment of PLC applications. Specifically, the pre-
sented tool flow supports either the design of new
control algorithms or the translation of existing al-
gorithms into C. Then, HLS and FPGA implemen-
tation tools are adopted, to implement the selected
algorithms as multicore, embedded designs, offering
performance improvements and hardware utilization
efficiency. Overall, the proposed methodology and
underlying tool flow support a novel high productiv-
ity prototyping platform for digital control applica-
tions, offering performance improvements compared
to software and very promising future extension capa-
bilities by utilizing state-of-the-art FPGA devices.
ACKNOWLEDGEMENTS
This research has been co-financed by the European
Union (European Social Fund - ESF) and Greek na-
tional funds through the operational program “Edu-
cation and Lifelong Learning” of the National Strate-
gic Reference Framework (NSRF) - Research Fund-
ing Program: ARCHIMEDES III: Investing in knowl-
edge society through the European Social Fund.
REFERENCES
Alonso, D., Suardiaz, J., Navarro, P. J., Alcover, P. M.,
and Lopez, J. A. (2009). Automatic generation of
VHDL code from traditional ladder diagrams apply-
ing a model-driven engineering approach. In 35nd
Annual Conference on Industrial Electronics, pages
2416–2421. IEEE.
ARM Ltd. (2013). AMBA AXI and ACE Protocol Specifica-
tion.
Bagni, D. and Mackay, D. (2013). Floating-point PID con-
troller design with Vivado HLS and system generator
for DSP. Xilinx Application Note XAPP1163.
Ben Othman, S., Ben Salem, A. K., Abdelkrim, H., and
Ben Saoud, S. (2012). MPSoC design approach of
FPGA-based controller for induction motor drive. In
International Conference on Industrial Technology,
pages 134–139. IEEE.
Ben Said, M.and Hemdani, A., Naouar, M. W., Monmas-
son, E., and Slama-Belkhodja, I. (2012). Standard
FPGA-based or full cSoC controllers for three-phase
PWM boost rectifier, two viable solutions. In 15th
International Power Electronics and Motion Control
Conference. IEEE.
Coussy, P. and Morawiec, A. (2008). High-level Synthesis:
From Algorithm to Digital Circuit. Springer-Verlag.
Economakos, C. and Economakos, G. (2008). FPGA imple-
mentation of plc programs using automated high-level
synthesis tools. In 17th International Symposium on
Industrial Electronics, pages 1908–1913. IEEE.
Ghosh, S., Barai, R. K., Bhattarcharya, S., Bhattacharyya,
P., Rudra, S., Dutta, A., and Pyne, R. (2013). An
FPGA based implementation of a flexible digital PID
controller for a motion control system. In Interna-
tional Conference on Computer Communication and
Informatics. IEEE.
Janabi-Sharifi, F. and Fan, J. (2000). A learning fuzzy sys-
tem for looper control in rolling mills. In International
Conference on Systems, Man, and Cybernetics, pages
3722–3727. IEEE.
Martin, G. and Smith, G. (2009). High-level synthesis: Past,
present, and future. IEEE Design and Test of Comput-
ers, 26(4):18–25.
Monmasson, E., Bahri, I., Idkhajine, L., Maalouf, A.,
and Naouar, W. M. (2012). Recent advancements
in FPGA-based controllers for AC drives applica-
tions. In 13th International Conference on Optimiza-
tion of Electrical and Electronic Equipment, pages 8–
15. IEEE.
Monmasson, E. and Cirstea, M. N. (2007). FPGA de-
sign methodology for industrial control systems - a
review. IEEE Transactions on Industrial Electronics,
54(4):1824–1842.
Monmasson, E., Idkhajine, L., Cirstea, M. N., Bahri, I., Ti-
san, A., and Naouar, M. W. (2011). FPGAs in in-
dustrial control applications. IEEE Transactions on
Industrial Informatics, 7(2):224–243.
Naouar, M. W., Monmasson, E., Naassani, A. A., and
Slama-Belkhodja, I. (2013). FPGA-based dynamic re-
configuration of sliding mode current controllers for
synchronous machines. IEEE Transactions on Indus-
trial Informatics, 9(3):1262–1271.
Navarro, D., Lucia, O., Barragan, L. A., Urriza, I., and
Jimenez, O. (2013). High-level synthesis for acceler-
ating the FPGA implementation of computationally-
demanding control algorithms for power convert-
ers. IEEE Transactions on Industrial Informatics,
9(3):1371–1379.
Patil, M. M., Subbaraman, S., and Nilkund, P. S. (2010).
IEC control specification to HDL synthesis: Consid-
erations for implementing PLC on FPGA and scope
for research. In International Conference on Control
Automation and Systems, pages 2170–2174. IEEE.
Silva, C. F., Quintans, C., Lago, J. M., and Mandado, E.
(2006). An integrated system for logic controller im-
plementation using FPGAs. In 32nd Annual Confer-
ence on Industrial Electronics, pages 195–200. IEEE.
Subbaraman, S., Patil, M. M., and Nilkund, P. S. (2010).
Novel integrated development environment for imple-
menting PLC on FPGA by converting ladder diagram
to synthesizable VHDL code. In 11th International
Conference on Control Automation Robotics and Vi-
sion, pages 1791–1795. IEEE.
Xilinx Inc. Vivado ESL design. http:// www.xilinx.com/
products/design-tools/vivado/integration/esl-design/
index.htm.
Program-basedandModel-basedPLCDesignEnvironmentforMulticoreFPGAArchitectures
733