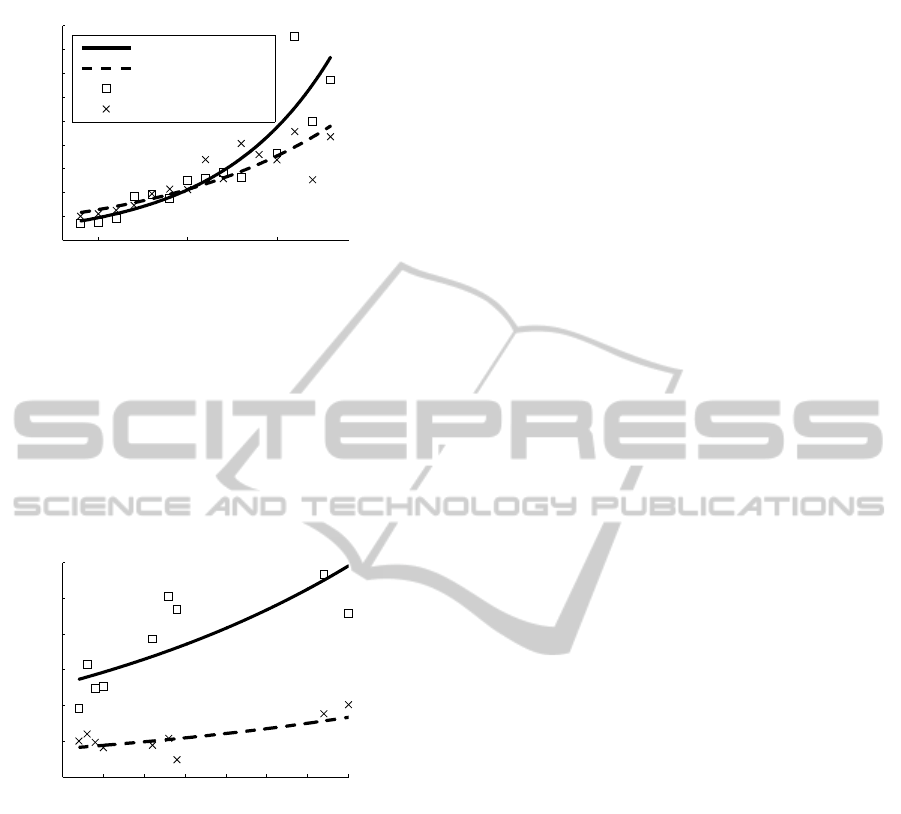
n [−]
t [ms]
Naive method
Sequential method
Naive−data
Sequential−data
Figure 9: Comparison of performance of the proposed
methods in environment with obstacles. The variable n de-
notes the number of control inputs describing the trajectory.
set to 10 control inputs. The comparison of average
time consumption is shown in Fig. 10.
The graph shows that the time consumption of
the naive method rapidly grows with increasing num-
ber of control inputs. The increase of time consump-
tion of the sequential method is more gradual due to
the reduction of the number of control inputs.
165 170 175 180 185 190 195 200
0
1
2
3
4
5
6
x 10
6
Figure 10: Comparison of performance of the proposed
methods when planning long trajectories. The legend re-
mains the same as in previous figures. The variable n de-
notes the number of control inputs describing the trajectory.
5 CONCLUSIONS
The motion planning methods presented in this paper
respect kinematic constraints of the particular MAVs
as well as the entire MAV formation. The resulting
trajectory is coded as a vector of control inputs, i.e.
in the form required by the MPC method. There-
fore, these methods are suitable for initial trajectory
planning for formations of MAVs. The proposed ap-
proaches increase the time efficiency of the method.
When employing the methods in a complex en-
vironment, an attention has to be paid to the choice
of the merging constants as well as to the setup of
the RRT algorithm. The experimental verification
showed that the sequential processing method is more
efficient, compared to the naive method. If the tra-
jectory guess for the method is selected from a set
of trajectories computed using the RRT algorithm,
the time required to find a solution can be significantly
reduced.
ACKNOWLEDGEMENTS
This work was supported by internal CTU grant no.
SGS14/073/OHK3/1T/13, GA
ˇ
CR postdoc grant no.
P103-12/P756 and M
ˇ
SMT grant under Kontakt II no.
LH11053.
REFERENCES
Abdessameud, A. and Tayebi, A. (2011). Formation control
of vtol unmanned aerial vehicles with communication
delays. Automatica, 47(11):2383 – 2394.
Chen, J., Sun, D., Yang, J., and Chen, H. (2010).
Leader-follower formation control of multiple non-
holonomic mobile robots incorporating a receding-
horizon scheme. Int. Journal Robotic Research,
29:727–747.
Krajn
´
ık, T., Nitsche, M., Faigl, J., Van
ˇ
ek, P., Martin, S.,
P
ˇ
reu
ˇ
cil, L., Duckett, T., and Mejail, M. (2014). A
practical multirobot localization system. Journal of
Intelligent and Robotic Systems, pages 1–24.
LaValle, S. M. (1998). Rapidly-exploring random trees a
new tool for path planning.
Mayne, D. Q., Rawlings, J. B., Rao, C. V., and Scokaert,
P. O. (2000). Constrained model predictive control:
Stability and optimality. Automatica, 36(6):789–814.
Maza, I., Kondak, K., Bernard, M., and Ollero, A. (2010).
Multi-uav cooperation and control for load transporta-
tion and deployment. Journal of Intelligent and
Robotic Systems, 57(1-4):417–449.
Mellinger, D., Shomin, M., Michael, N., and Kumar, V.
(2013). Cooperative grasping and transport using mul-
tiple quadrotors. In Distributed autonomous robotic
systems, pages 545–558. Springer.
Merino, L., Caballero, F., Ferruz, J., Wiklund, J., Forss
´
en,
P.-E., and Ollero, A. (2007). Multi-uav cooperative
perception techniques. In Multiple Heterogeneous
Unmanned Aerial Vehicles, pages 67–110. Springer.
Saska, M., Kasl, Z., and P
ˇ
reu
ˇ
cil, L. (2014). Motion plan-
ning and control of formations of micro unmanned
aerial vehicles. In 19th World Congress of IFAC. To
be published.
Saska, M., Mej
´
ıa, J., Stipanovi
ˇ
c, D. M., Von
´
asek, V.,
Schilling, K., and P
ˇ
reu
ˇ
cil, L. (2013). Control and
navigation in manoeuvres of formations of unmanned
mobile vehicles. European Journal of Control,
19(2):157–171.
RapidlyExploringRandomTrees-basedInitializationofMPCTechniqueDesignedforFormationsofMAVs
443