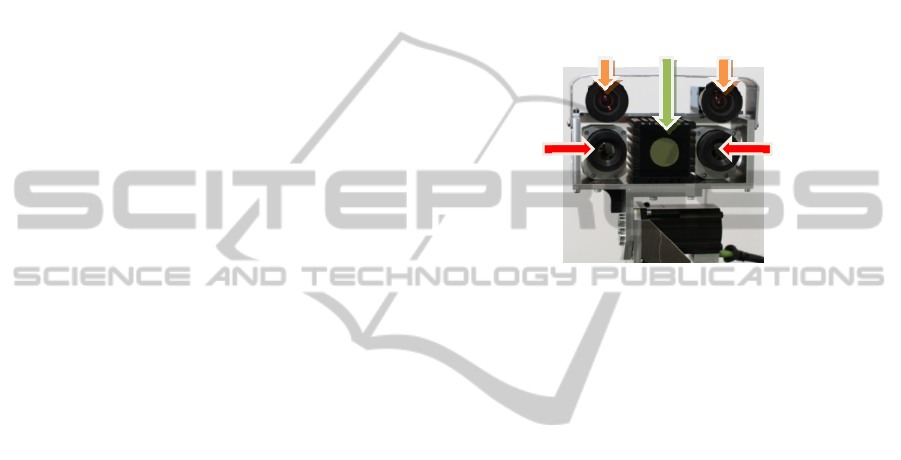
imagers into one image. Nowadays several
companies provide combined CCD – thermal
imagers, but their approach is simplistic – the
images are only geometrically aligned, so because of
parallax the images do not correspond exactly for
most cases. Furthermore the used CCD cameras are
typically of low quality and with limited field of
view. So these solutions are not appropriate for
telepresence in rescue robotics.
The technique was studied by our team in the
past (Zalud, 2005), but as the sensory prices
decreased and TOF cameras matured, the technique
now may be done more advanced. In this article we
introduce a technique for visual spectrum data and
thermal imager data alignment with help of data
from TOF camera. The TOF camera measures a
distance of an object, while corresponding pixels are
found on color camera and thermal imager. Each of
the sensors has to be calibrated for geometrical
errors, mutual position and orientation is found and
used to make the correspondence calibrations.
This is done for two stereo-pairs of cameras, so
the resulting image may be presented to head-
mounted display with stereovision support, so the
operator has a very good spatial representation of the
surrounding under any visibility conditions.
It has to be pointed out the sensors on the
sensory head will not be used only for this
technique, in parallel we also develop SLAM
technique with similar texture-mapping algorithms.
2 HARDWARE
2.1 Orpheus-X3
The Orpheus-X3 is an experimental reconnaissance
robot based on the Orpheus-AC2 model made by our
team to facilitate the measurement of chemical and
biological contamination or radioactivity for military
purposes (Fig. 1). The Orpheus-X3 offers the same
drive configuration as its predecessor, namely the
four extremely precise AC motors with harmonic
gears directly mechanically coupled to the wheels;
this configuration makes the robot very effective in
hard terrain and enables it to achieve the maximum
speed of 15 km/h. The main difference consists in
the chassis, which is not designed as completely
waterproof but consists of a series of aluminum
plates mounted on a steel frame of welded L-
profiles. This modular structural concept makes the
robot markedly more versatile, which is a very
important aspect in a robot made primarily for
research activities. Furthermore, the device is
equipped with a 3DOF manipulator for the sensory
head. The manipulator, again, comprises very
powerful AC motors combined with extremely
precise, low backlash harmonic drive gearboxes by
the Spinea company. The presence of such precise
gearboxes can be substantiated by several reasons,
mainly by the fact that the robot will be used not
only for telepresence but also for mobile mapping
and SLAM. As currently planned, the robot’s only
proximity sensor will be the TOF camera placed on
the sensory head.
Figure 2: The sensory head. 1 – the tricolor CCD cameras,
2 – the thermal imagers, 3 – the TOF camera.
2.1.1 Sensory Head
The sensory head containing five optical sensors is
shown in Fig. 2.
Two tricolor CCD cameras (see 1 in Fig. 2).
TheImagingSource DFK23G445 with 1280x960
pixels resolution, max refresh rate 30Hz, and
GiGe Ethernet protocol. A Computar 5mm 1:1.4
lens is used.
Two thermal Imagers (see 2 in Fig. 2).
MicroEpsilon TIM 450 with a wide lens,
382x288 pixels resolution, temperature resolution
of 0.08K, a USB output.
One TOF camera (see 3 in Fig. 2). A Mesa
Imaging SR4000 with the range of 10m, 176x144
pixels resolution, an Ethernet output. The field of
view is 56˚(h) x 69˚(v).
From the preceding text we can conclude, the
fields-of-view (FOVs) of the sensors are similar.
The largest FOV captures TOF camera, which is
required for simultaneous use of stereovision and
thermal stereovision. The main disadvantage of the
used TOF camera is its low number of pixels (spatial
resolution). In relation to the CCD cameras is about
10 times lower in one axis and in relation to thermal
imagers, it is 2 times lower.
1
1
2
2
3
ICINCO2014-11thInternationalConferenceonInformaticsinControl,AutomationandRobotics
460