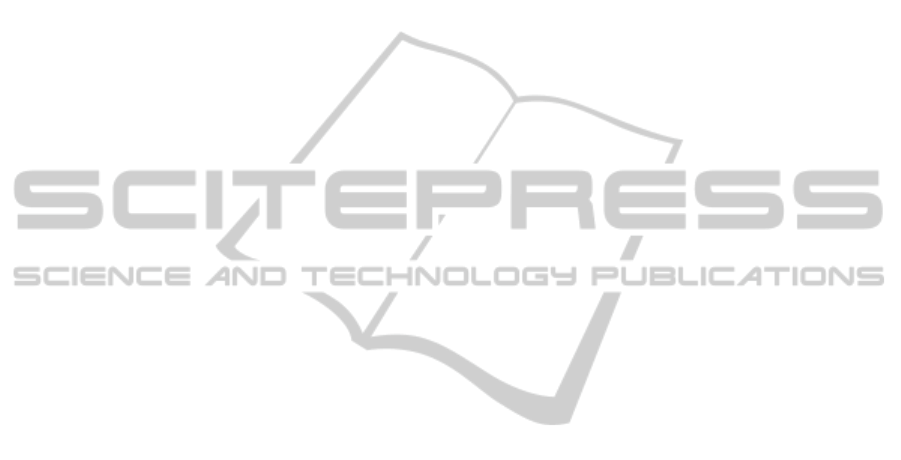
ultracapacitors and batteries. Such integration,
suggested as future work, would ensure both the
autonomy and the charging speed requirements of
the platform. In fact, using exclusively one 116F,
4.12Wh ultracapacitors module as energy-storing
device, the mobile platform achieved an autonomy
of 22 minutes after a charging time of 1 minute and
57 seconds, exceeding the autonomy required by the
platform when the charging time is limited to 2
minutes. It should be noted that the charging time is
less than 10% of the autonomy time. On the other
hand, the expected autonomy of the mobile platform
powered by a fully charged conventional 12V,
12Ah, 144Wh lead-acid battery, like the one used in
this work, ranges from 7 to 9 hours, fully satisfying
the autonomy required by the platform when there
are no charging time restrictions.
Integrating ultracapacitors and batteries in the
same power supply system also would release the
batteries from the requirement of providing high
power peaks, extending their lifetime.
Battery energy densities are much larger then the
ones offered by ultracapacitors but the introduction
of new materials may reduce the difference in a near
future.
An ultracapacitor is much more expensive than a
battery with the same energy storage capacity.
However, ultracapacitors cost has been significantly
decreasing. Furthermore, because ultracapacitors
allow much more charging/dicharging cycles than
batteries, the cost difference between the two
components is mitigated.
In addition to the suggested integration of
ultracapacitors and batteries in the same power
supply system, the following tasks are suggested as
future work: implementing control algorithms
capable of identifying the battery type to be charged
and its voltage; using a high-frequency transformer
instead of a 50Hz transformer, which would reduce
the cost, size and weight of the charger module,
allowing its installation onboard the mobile
platform; developing more compact PCBs using
surface-mount devices (SMD).
ACKNOWLEDGEMENTS
This work has been supported by FCT – Fundação
para a Ciência e Tecnologia within the Project
Scope: Pest-OE/EEI/UI0319/2014.
REFERENCES
Awerbuch, J. J.; Sullivan, C. R.; Control of Ultracapacitor-
Battery Hybrid Power Source for Vehicular
Applications; ENERGY 2008, Energy 2030
Conference, 2008, Page(s): 1 – 7. Digital Object
Identifier: 10.1109/ENERGY.2008.4781003.
Awerbuch, J. J.; Sullivan, C. R.; Filter-based Power
Splitting in Ultracapacitor-Battery Hybrids for
Vehicular Applications; COMPEL 2010, Control and
Modeling for Power Electronics, 2010, Pages(s): 1 –
8. Digital Object Identifier: 10.1109/
COMPEL.2010.5562429.
Bernholc, J.; Ranjan, V.; Zheng, X. H.; Jiang, J.; Lu, W.;
Abtew, T. A.; Boguslawski, P.; Nardelli, M.B.;
Meunier, V.; Properties of High-Performance
Capacitor Materials and Nanoscale Electronic
Devices, HPCMP-UGC 2010, High Performance
Computing Modernization Program Users Group
Conference, 2010, Page(s): 195 – 200. Digital Object
Identifier: 10.1109/HPCMP-UGC.2010.76.
Dai Haifeng; Chang Xueyu; A Study on Lead Acid
Battery and Ultra-capacitor Hybrid Energy Storage
System for Hybrid City Bus; ICOIP 2010,
International Conference on Optoelectronics and
Image Processing, 2010, Page(s): 154 – 159. Digital
Object Identifier: 10.1109/ICOIP.2010.321.
Haihua Zhou; Bhattacharya, T.; Duong Tran; Siew, T. S.
T.; Khambadkone, A. M.; Composite Energy Storage
System Involving Battery and Ultracapacitor With
Dynamic Energy Management in Microgrid
Applications; IEEE Transactions on Power
Electronics, 2010, Page(s): 923 – 930. Digital Object
Identifier: 10.1109/TPEL.2010.2095040.
Hua, A. C. -C.; Syue, B. Z. -W.; Charge and discharge
characteristics of lead-acid battery and LiFePO4
battery; IPEC 2010, International Power Electronics
Conference, 2010, Page(s): 1478 – 1483. Digital
Object Identifier: 10.1109/IPEC.2010.5544506.
JennHwa Wong; Idris, N. R. N.; Anwari, M.; Taufik, T.; A
Parallel Energy-Sharing Control for Fuel cell-Battery-
Ultracapacitor Hybrid Vehicle; ECCE 2011, Energy
Conversion Congress and Exposition, 2011, Page(s):
2923 – 2929. Digital Object Identifier: 10.1109/
ECCE.2011.6064162.
Lei Wang; Hui Li; Maximum Fuel Economy-oriented
Power Management Design for a Fuel Cell Vehicle
Using Battery and Ultracapacitor; IEEE Transactions
on Industry Applications, 2010, Page(s): 1011 – 1020.
Digital Object Identifier: 10.1109/TIA.2010.2045097.
Li Siguang; Zhang Chengning; Xie Shaobo; Research on
Fast Charge Method for Lead-Acid Electric Vehicle
Batteries; ISA 2009, International Workshop on
Intelligent Systems and Applications, 2009, Page(s): 1
– 5. Digital Object Identifier: 10.1109/
IWISA.2009.5073068.
Miller, J. M.; Energy Storage Technology Markets and
Application’s: Ultracapacitors in Combination with
Lithium-ion; ICPE 2007, International Conference on