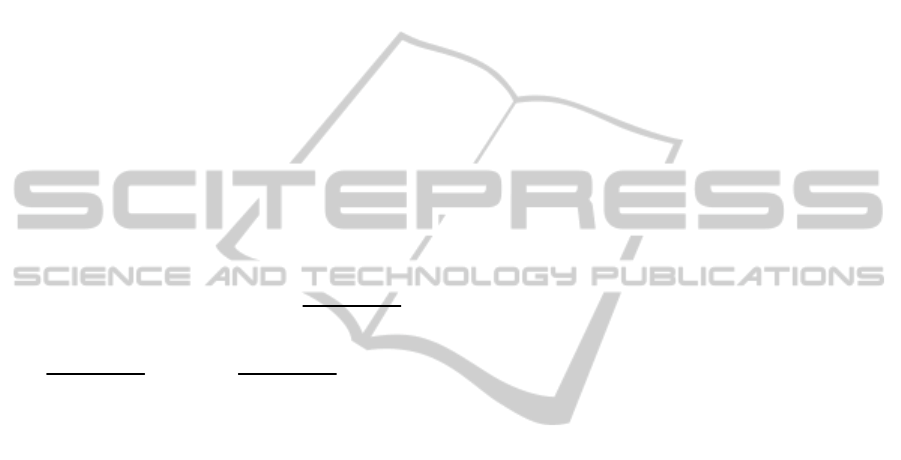
performances.
The two feedback signals associated to the
cascade structure result measuring the pH values at
the output of the two processes (at the output of tank
1, respectively equivalent tank). The process
associated to tank 1, due to the smaller length of this
tank, is faster than the process associated to
equivalent tank and it is included in the internal
loop. The compensation block CB (see Fig. 2)
receives the measurement signals of the flow and of
the pH value of the disturbance (of the acid
introduced in the reaction) and generates a control
signal that is finally subtracted from the control
signal C
2
. The compensation generated by CB
represents the feed-forward component of the
structure. The tuning of both controllers C
1
and C
2
is
made using an adapted form of module criterion for
the case when the model of the process is expressed
through PDEs (for this type of processes do not exist
specific tuning methods). Using the module criterion
(applied for second order processes) is obtained the
general form of the controller parameters, valid for
both controllers:
12
PC
EX
TT
K
2K T
,
IC
EX
K
2K T
1
,
12
DC
EX
TT
K
2K T
, where
1
T and
2
T (through singularization) are the time
constants corresponding to each of the two processes
(these constants are calculated in each of the two
cases for the corresponding values of (p)). Also,
T
AC
TTTT
. The
EX
K constant is present
in all three formulae and, while changing its value,
the three controller parameters are simultaneously
modified. Firstly, the value of the
EX
K is fixed for
the controller from the internal loop. After that,
another value of the
EX
K constant is chosen for the
controller from the external loop. The numerical
simulation of the control structure is made in order
to obtain the system performances. If the
performances are not enclosed in the imposed limits,
the value of
EX
K associated to C
1
is decreased
progressively, for each decrease the simulation of
the structure being repeated and, in each case the
obtained performances being evaluated. Hence, the
tuning method is an iterative one. In the case when,
from a simulation to the following one, the
performances of the system do not have a significant
improvement, the
EX
K constant associated to C
2
is
decreased as value and keeping this value constant,
the iterative procedure previously presented is
repeated (modifying only the parameters of C
1
) until
the imposed performances are obtained. In order to
obtain much better performances than the imposed
ones, the iterative tuning procedure can be
continued, but taking into consideration the variation
form and limits of the actuating signal. The variation
of the
EX
K constants between two successive
iterations, in both controller cases, has not an
imposed value (being modified considering the
grade of the performances improvement from an
iteration to the next one). In each controller case,
decreasing the value of the
EX
K constant we can
obtain a stronger control effect (action).
After obtaining the parameters of C
1
and C
2
, the
tuning of CB can be made. Using the same general
formulae, as in the case of C
1
and C
2
, but only a PD
structure, the
EX
K constant is decreased
progressively until the best possible performances
are obtained. After applying the presented
procedure, the following parameters are obtained:
for C
1
:
EX1
K 437.93 , for C
2
:
EX2
K0.35 ,
respectively for CB:
EXCB
K10 .
In Fig. 5, the comparative graph between the
automatic system’s analytical and numerical step
response is presented, at the overflowing point from
the system (the overflowing point of the equivalent
tank), considering the components of the disturbance
constants at the values pH
A
= 3 and D
A
(t) = 3l/s
(step disturbance, usual in the treated case).
On the graph the two responses cannot be
differentiated with the free eye due to the very small
errors between them. In steady state regime, the
value of cumulated relative error in percents
(Ungureşan and Niac, 2011) is proportional to
10
-3
%, this value very close to 0 showing the very
good numerical simulation performances. Also the
obtained control performances are very high ones,
the steady state error at position being 0 (the effect
of the disturbance is rejected), the settling time can
be considered 0 min because the value of the
response is enclosed in the stationary band of ±1%
around the steady state value (7) and the overshoot
module has an insignificant value of 0.03 % (the pH
variation around 7 does not affect the good working
of the system).
The necessity of using a very complex control
structure appears due to the fact that the imposed
performances to the control structure are very
restrictive ones, due to the sensitive character of the
application. In order to study the possibility of
NumericalSimulationandAutomaticControlofthepHValueinanIndustrialBluntingSystem
545