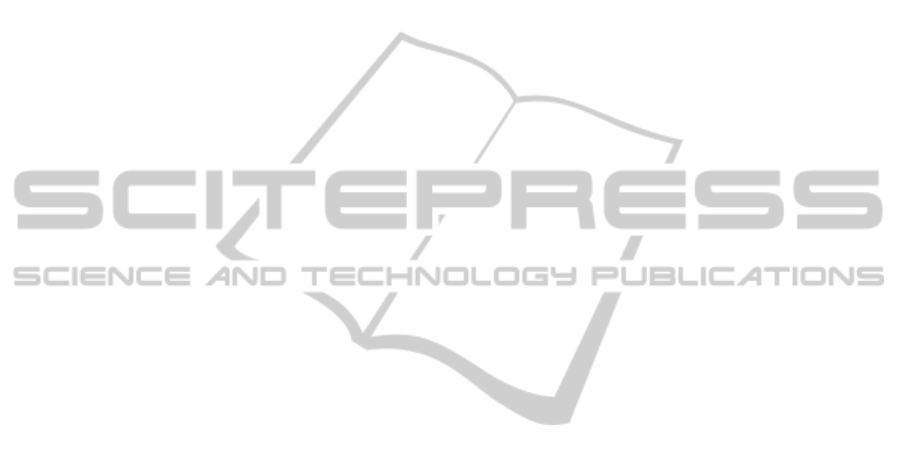
achieved by this controller in compared to a
conventional PID approach. The future work of
the authors will include the implementation of the
proposed approach on the real arm to validate the
performance of this scheme in experimental results.
ACKNOWLEDGEMENTS
This work is supported by the European Research
Council under EU FP7-ICT projects SAPHARI no.
287513 and WALKMAN no. 611832.
REFERENCES
Albu-Sch¨affer, A., Petit, F., and Ott, C. (2012). Energy
Shaping Control for a Class of Underactuated
Euler-Lagrange Systems. In Petrovic, I. and Korondi,
P., editors, 10th IFAC Symposium on Robot Control,
Dubrovnik, Croatia.
Astr¨om, K. J. and Murray, R. M. (2010). Feedback systems:
an introduction for scientists and engineers. Princeton
university press.
Ben-Israel, A. (1966). A Newton-Raphson method for
the solution of systems of equations. Journal
of Mathematical analysis and applications,
15(2):243–252.
Beyl, P., Van Damme, M., Van Ham, R., Vanderborght, B.,
and Lefeber, D. (2009). Design and control of a lower
limb exoskeleton for robot-assisted gait training.
Applied Bionics and Biomechanics, 6(2):229–243.
Bicchi, A., Rizzini, S. L., and Tonietti, G. (2001).
Compliant design for intrinsic safety: General issues
and preliminary design. In Intelligent Robots
and Systems, 2001. Proceedings. 2001 IEEE/RSJ
International Conference on, volume 4, pages
1864–1869. IEEE.
Braun, D. J., Petit, F., Huber, F., Haddadin, S., Van
Der Smagt, P., Albu-Schaffer, A., and Vijayakumar,
S. (2013). Robots driven by compliant actuators:
Optimal control under actuation constraints. IEEE
Transactions on Robotics, 29(5):1085–1101.
Cannon, R. H. and Rosenthal, D. E. (1984). Experiments
in control of flexible structures with noncolocated
sensors and actuators. Journal of Guidance, Control,
and Dynamics, 7(5):546–553.
Catalano, M. G., Grioli, G., Garabini, M., Bonomo,
F., Mancini, M., Tsagarakis, N., and Bicchi, A.
(2011). VSA-CubeBot: A modular variable stiffness
platform for multiple degrees of freedom robots.
In Proceedings - IEEE International Conference on
Robotics and Automation, pages 5090–5095.
Chen, L., Garabini, M., Laffranchi, M., Kashiri, N.,
Tsagarakis, N. G., Bicchi, A., and Caldwell, D. G.
(2013a). Optimal Control for Maximizing Velocity
of the CompAct Compliant Actuator. In Robotics
and Automation (ICRA), 2013 IEEE International
Conference on, pages 516–522, Karlsruhe (Germany).
Chen, L., Laffranchi, M., Lee, J., Kashiri, N., Tsagarakis,
N. G., and Caldwell, D. G. (2013b). Link
position control of a compliant actuator with unknown
transmission friction torque. In Intelligent Robots
and Systems (IROS), 2013 IEEE/RSJ International
Conference on, pages 4058–4064. IEEE.
De Luca, A., Siciliano, B., and Zollo, L. (2005). PD control
with on-line gravity compensation for robots with
elastic joints: Theory and experiments. Automatica,
41(10):1809–1819.
Garcia, E., Ar´evalo, J. C., Mu˜noz, G., and Gonzalez-de
Santos, P. (2011). Combining series elastic actuation
and magneto-rheological damping for the control of
agile locomotion. Robotics and Autonomous Systems,
59(10):827–839.
Haddadin, S., Albu-Sch¨affer, A., and Hirzinger, G. (2009).
Requirements for safe robots: Measurements, analysis
and new insights. The International Journal of
Robotics Research, 28(11-12):1507–1527.
Kashiri, N., Laffranchi, M., Lee, J., Tsagarakis, N. G.,
Chen, L., and Caldwell, D. (2014a). Real-time
damping estimation for variable impedance actuator.
In Robotics and Automation (ICRA), 2014 IEEE
International Conference on, pages 1072–1077.
IEEE.
Kashiri, N., Laffranchi, M., Tsagarakis, N. G., Margan, A.,
and Caldwell, D. G. (2014b). Physical Interaction
Detection and Control of Compliant Manipulators
Equipped with Friction Clutches. In Robotics
and Automation (ICRA), 2014 IEEE International
Conference on, pages 1066–1071. IEEE.
Kashiri, N., Laffranchi, M., Tsagarakis, N. G., Sardellitti,
I., and Caldwell, D. G. (2013a). Dynamic
modeling and adaptable control of the CompAct arm.
In Mechatronics (ICM), 2013 IEEE International
Conference on, pages 477–482.
Kashiri, N., Tsagarakis, N. G., Laffranchi, M., and
Caldwell, D. G. (2013b). On the stiffness design
of intrinsic compliant manipulators. In Advanced
Intelligent Mechatronics (AIM), 2013 IEEE/ASME
International Conference on, pages 1306–1311.
IEEE.
Kikuuwe, R. and Fujimoto, H. (2006). Proxy-based sliding
mode control for accurate and safe position control.
In Robotics and Automation, 2006. ICRA 2006.
Proceedings 2006 IEEE International Conference on,
pages 25–30. IEEE.
Kikuuwe, R., Yasukouchi, S., Fujimoto, H., and Yamamoto,
M. (2010). Proxy-based sliding mode control: a safer
extension of PID position control. Robotics, IEEE
Transactions on, 26(4):670–683.
Laffranchi, M., Tsagarakis, N., and Caldwell, D. G.
(2011). A compact compliant actuator (CompAct)
with variable physical damping. In Robotics
and Automation (ICRA), 2011 IEEE International
Conference on, pages 4644–4650. IEEE.
Laffranchi, M., Tsagarakis, N. G., and Caldwell, D. G.
(2013). CompAct Arm: a Compliant Manipulator
ICINCO2014-11thInternationalConferenceonInformaticsinControl,AutomationandRobotics
182