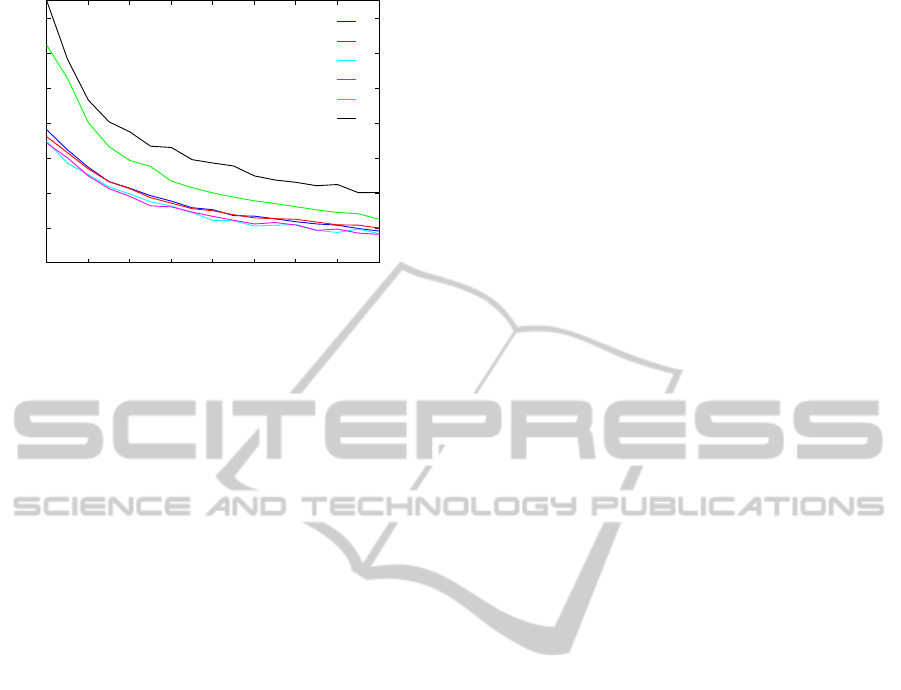
¯e
R
¯e(R
x
#1
)
¯e(R
x
#2
)
¯e(R
x
#3
)
¯e(R
x
#4
)
¯e(R
z
#2
)
¯e(R
z
#4
)
Number Poses N
0
0.05
0.1
0.15
0.2
0.25
0.3
0.35
4 6 8 10 12 14 16 18 20
Figure 10: Average rotational error of R
x
and R
z
over the
number of poses N.
5 CONCLUSIONS
This paper presents two self-calibration methods for
externally calibrating a projector to a robotic hand.
One of them additionally gives the solution of the
transformation between the robot base and an exter-
nal camera.
In contrast to existing approaches, the presented
solutions need neither any additional device at the
end-effector nor any calibration unit in the environ-
ment. The capability is demonstrated by the posi-
tive results of using real hardware. Provided with
ground truth data, simulations prove the accuracy of
the methods.
It has been shown that the error that results from
the unknown scale factors quickly converges by in-
creasing the number of poses. The additional error
resulting from simultaneously estimating the camera
pose is negligible. This is beneficial since the camera-
projector pair can be used as a structured light sensor.
Future works will tackle optimizing of the solu-
tion and identifying good robot arm poses for calibra-
tion. Spatial coded light will be considered, as it en-
ables us to use the method in dynamic environments.
REFERENCES
Andreff, N., Horaud, R., and Espiau, B. (2001). Robot
hand-eye calibration using structure-from-motion. In-
ternational Journal of Robotics Research, 20(3):228–
248.
Brewer, J. W. (1978). Kronecker products and matrix calcu-
lus in system theory. IEEE Trans Circuits Syst, CAS-
25(9):772–781.
De Tommaso, D., Calinon, S., and Caldwell, D. (2012).
Using compliant robots as projective interfaces in dy-
namic environments. Lecture Notes in Computer Sci-
ence, 7621:338–347.
Dornaika, F. and Horaud, R. (1998). Simultaneous robot-
world and hand-eye calibration. IEEE Transactions
on Robotics and Automation, 14(4):617–622.
Gavaghan, K., Peterhans, M., Oliveira-Santos, T., and
Weber, S. (2011). A portable image overlay
projection device for computer-aided open liver
surgery. IEEE Transactions on Biomedical Engineer-
ing, 58(6):1855–1864.
Hartley, R. (1997). In defense of the eight-point algorithm.
IEEE Transactions on Pattern Analysis and Machine
Intelligence, 19(6):580–593.
Hartley, R. and Zisserman, A. (2000). Multiple View Geom-
etry in Computer Vision.
Lourakis, M. (Jul. 2004). levmar: Levenberg-marquardt
nonlinear least squares algorithms in C/C++. [web
page] http://www.ics.forth.gr/∼lourakis/levmar/. [Ac-
cessed on 31 Jan. 2005.].
Moreno, D. and Taubin, G. (2012). Simple, accurate, and
robust projector-camera calibration. In 3D Imaging,
Modeling, Processing, Visualization and Transmis-
sion (3DIMPVT), 2012 Second International Confer-
ence on, pages 464–471.
Reinhart, G., Vogl, W., and Kresse, I. (2007). A projection-
based user interface for industrial robots. In Proceed-
ings of the 2007 IEEE International Conference on
Virtual Environments, Human-Computer Interfaces,
and Measurement Systems, VECIMS 2007, pages 67–
71.
Salvi, J., Pags, J., and Batlle, J. (2004). Pattern codification
strategies in structured light systems. Pattern Recog-
nition, 37(4):827–849.
Shiu, Y. C. and Ahmad, S. (1989). Calibration of wrist-
mounted robotic sensors by solving homogeneous
transform equations of the form ax = xb. IEEE Trans-
actions on Robotics and Automation, 5(1):16–29.
Tsai, R. Y. and Lenz, R. K. (1989). New technique for fully
autonomous and efficient 3d robotics hand/eye cali-
bration. IEEE Transactions on Robotics and Automa-
tion, 5(3):345–358.
Zhang, S. and Huang, P. (2006). Novel method for struc-
tured light system calibration. Optical Engineering,
45(8).
Zhang, Z. (2000). A flexible new technique for camera cal-
ibration. IEEE Transactions on Pattern Analysis and
Machine Intelligence, 22(11):1330–1334.
Zhuang, H., Roth, Z. S., and Sudhakar, R. (1994). Si-
multaneous robot/world and tool/flange calibration
by solving homogeneous transformation equations of
the form ax=yb. IEEE T. Robotics and Automation,
10(4):549–554.
Hand-projectorSelf-calibrationUsingStructuredLight
91