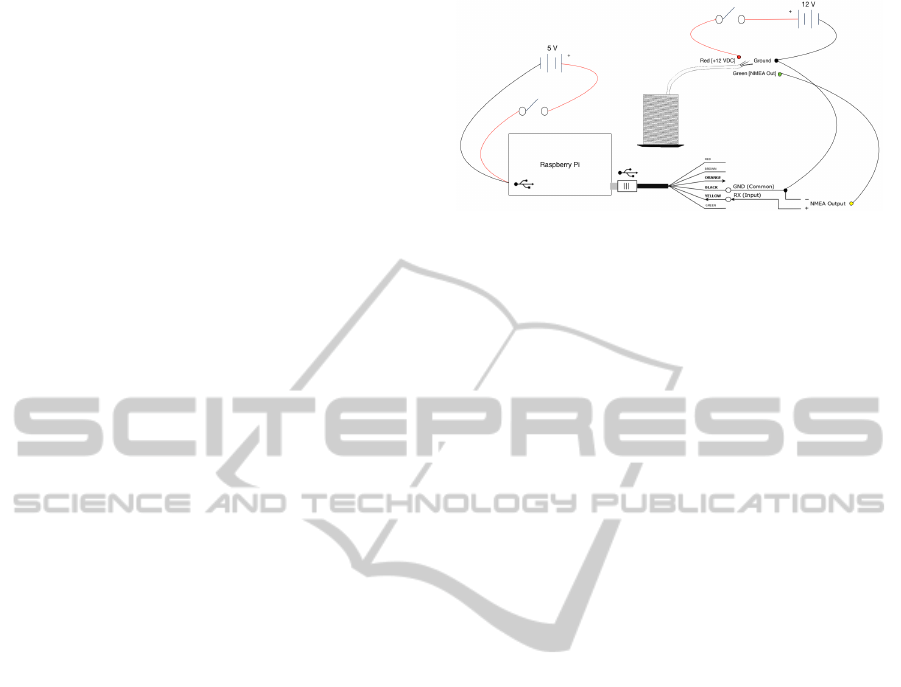
data that is transmitted from a single talker to multiple
listeners in parallel. The newer NMEA 2000 proto-
col is slowly being adopted in favour of its predeces-
sor, the NMEA 0183. The NMEA 2000 (Association
et al., 2005) is a network protocol built on top of the
controller area network bus supporting both multiple
talkers and multiple listeners at 250 kbps. Another
difference between the NMEA 0183 and NMEA 2000
protocols is a switch from ASCII encoded data sen-
tences to a compact binary format with a proprietary
specification (Spitzer et al., 2009).
2.3 From Echo Sounders to ROS
A wide range of devices support the NMEA 0183 pro-
tocol. In terms of the robotics community, perhaps
the most well integrated of these devices are GPS re-
ceivers. Fortunately, a number of researchers have
developed software infrastructures that support GPS
devices and this investment is easily repurposed for
Echo Sounders that support the NMEA 0183 proto-
col.
ROS has become a de-facto standard for much
of the autonomous robot community and its use
is especially prevalent in the research community.
Within ROS, processes are represented as nodes
which communicate through messages within a pub-
lisher/subscriber framework. The process of integrat-
ing echo sounders within a ROS infrastructure in-
volves providing the necessary power/data connec-
tions to the device and then transducing messages re-
ceived from the echo sounder into corresponding ROS
messages.
3 PHYSICAL CONSTRUCTION
A critical aspect in the construction of any component
of a field robot, and this is especially true for robots
working near water, is ensuring that the device is iso-
lated from its environment. Incidents that are only a
minor annoyance for a robot operating indoors can be
catastrophic for a field robot. For the echo sounder
system described here, water is of particular concern.
Although exposure to fresh water might be brushed
aside, salt-water or water from chlorine-treated pools
can result in permanent damage to electric circuits,
and there is always the possibly of complete emersion
due to wave and sea action. In order to deal with this
issue, we have encased the sensor in a water-proof
housing. Two different sensor housings have been
built. The first, an experimental housing, is shown
in Figure-2(a) while the production housing is shown
Figure 3: RECHOS wiring diagram.
in Figure-2(b). In both cases the devices are designed
to be sealed against the elements.
In the design of any device that will be deployed in
harsh environments breaks in the case should be min-
imized. Switches mounted externally to the case are
designed to be waterproof, and the number of cables
leaving the device are minimized. The experimental
housing was designed to be completely sealed, with
communications to and from the device being accom-
plished via a wireless signal. For the production de-
vice we have augmented the wireless capability with
the ability to hardwire the device into the ROS net-
work should this prove desirable.
The experimental housing is based on a cylindri-
cal underwater enclosure. Acrylic ports are used to
seal the caps of the cylinder. Three toggle switches
are mounted to the top port. Two are used to con-
trol power to the transducer and onboard electron-
ics. The third is available for use by application soft-
ware. This configuration allows for pre- and post-
deployment testing, and testing of the system out of
water using a mobile device or laptop, with the trans-
ducer safely powered off. The production housing is
based around standard ABS pipe infrastructure and
is designed to be more easily mounted on the King-
fisher and other robot platforms. This improved hous-
ing also includes additional ports facilitating ethernet
connectivity and the recharging of batteries.
The sensor packages are designed to be a self-
contained systems so as to enable the device to
be fully portable. Although the planned deploy-
ment of the production device involves the Kingfisher
robot (Figure-1) it is intended that the device will
also be deployed on other devices including recre-
ational/commercial vessels. In such deployments it
may not be straightforward to provide physical wiring
between the sensor and power/data networks.
The ROS echo sounder (RECHOS) is comprised
of three major components. The production version
includes an additional component to improve the
accuracy of sensor readings.
ICINCO2014-11thInternationalConferenceonInformaticsinControl,AutomationandRobotics
508