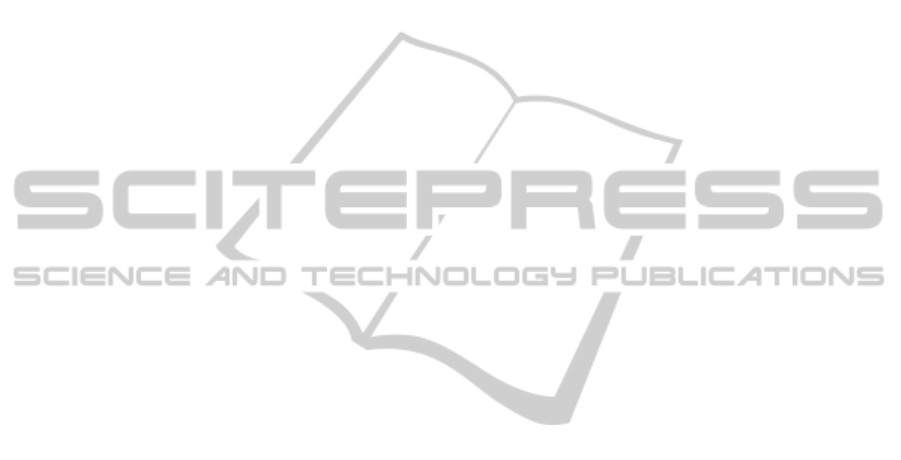
6 CONCLUSIONS
In this study, two objective functions are considered.
One is the flight distance, the other is the robustness.
The flight distance is the most important, but
robustness is also important, especially for the world
of competitive sports. Therefore, concurrent
optimization of flight distance and robustness of
discus throwing is carried out using a genetic
algorithm. Fourteen design variables are considered,
which include the skill of the thrower and the
inherent features of the equipment. The design
variables concerned with the skill and the equipment
were treated concurrently. The conclusions are
summarized as follows:
There is a trade-off between flight distance and
robustness.
The longest flight distance that could be
achieved was 79.0 meters. However, it is not
robust. There is a possibility of losing flight
distance of 1.3 meters, if the release condition
slightly deviates from the optimal release
condition.
The flight distance is 78.8 meters at the sweet
spot solution, where both objective functions of
the flight distance and the robustness have
better values simultaneously. There is a
possibility of losing flight distance of 0.48
meters.
The stalling angle for the sweet spot solution is
relatively high. In other words, the maximum
lift for the sweet spot solution becomes greater.
At the sweet spot solution, the spin rate about
the transverse axis is a relatively high
R of 6.22
rev/s, the moment of inertia on the transverse
axis is a relatively high
I
T
of 0.0058 kgm
2
and
the mass is almost the lowest permissible
m
d
of
1.007 kg. The width is a relatively high
w of
181.5mm, the thickness is 38mm, the metal rim
radius is a relatively high
R
MR
of 6.3mm and
the diameter of the flat center area is a
relatively high
D
FCA
of 55mm.
ACKNOWLEDGEMENTS
This work is supported by a Grant-in-Aid for
Scientific Research (A), Japan Society for the
Promotion of Science.
REFERENCES
Deb, K., 2001. Multi-Objective Optimization using
Evolutionary Algorithms. Wiley, New York
Hubbard, M. and Cheng, K., 2007. Optimal discus
trajectories, J Biomechanics, 40, pp.3650-3659.
Leigh, S., Liu, H., Hubbard, M. and Yu, B., 2010.
Individualized optimal release angles in discuss
throwing, J Biomechanics, 43, pp.540-545.
Sasaki, D., and Obayashi, S., Efficient search for trade-
offs by adaptive range multi-objective genetic
algorithms, AIAA Journal of Aerospace Computing,
Information, and Communication, 2005, pp.44-64.
Seo, K., Kobayashi, O., Murakami, M., Yorita, D., Nagai,
H. and Asai, K., 2010. Simulation of the trajectory of a
punted rugby ball taking into account the
asymmetrical pressure distribution caused by the
seams. Journal of Visualization, 13, pp. 97-105.
Seo K., Shimoyama K., Ohta K., Ohgi Y. and Kimura Y.,
2012. Aerodynamic behaviour of a discus, Procedia
Engineering 34, pp.92-97.
Stevens, B. and Lewis, F., 2003. Aircraft control and
simulation, Wiley. Hoboken, New Jersey, 2
nd
edition.
ECTA2014-InternationalConferenceonEvolutionaryComputationTheoryandApplications
206