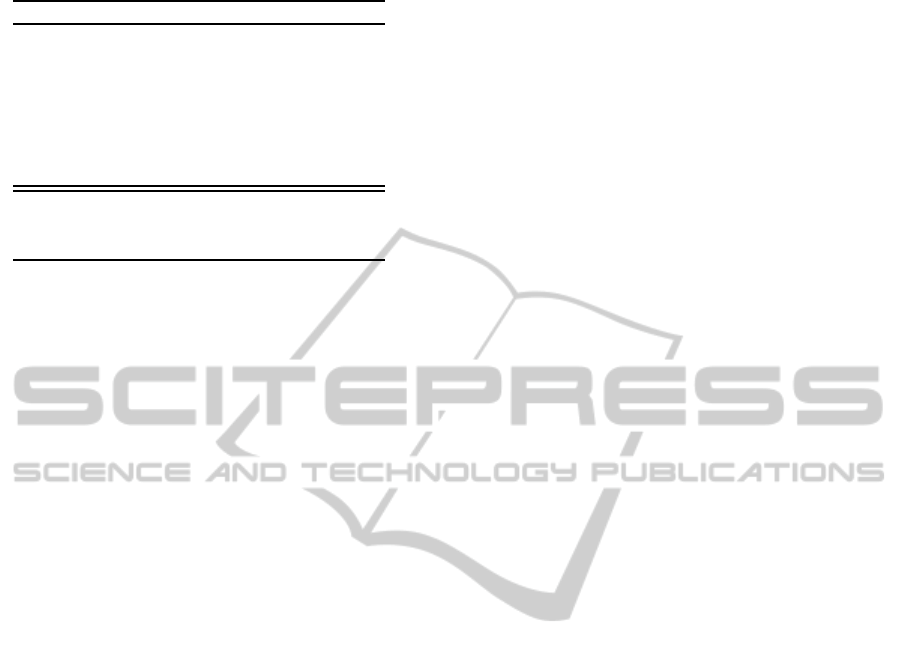
Table 9: Experimental results.
Control Strategy KPI
1
KPI
2
KPI
3
Expertise 4.25 -0.019 6.60
Strategy ‘a’ 2.38 -0.236 -6.75
Expertise -6.25 0.208 4.66
Strategy ‘b’ 1.45 -0.062 -2.50
Expertise -1.18 0.048 2.17
Strategy ‘a’ 3.92 -0.015 -0.43
Strategy ‘b’ -5.76 -0.231 -0.93
Expertise (mean) -1.06 0.08 4.48
Strategy ‘a’ (mean) 3.15 -0.13 -3.59
Strategy ‘b’ (mean) -2.16 -0.15 -1.72
reduction of the coke consumption as well as of the
IRFs production have been gained. The strategy ‘b’,
on the other hand, led to comparable results regarding
the coke consumption and the IRFs production, but
caused an average decrement of the productivity.
During both the short and the long period tests the
opinions of the technicians have been taken into ac-
count in order to evaluate the practical goodness of
the strategies as well as the KPI’s variations.
The behaviour most frequently used by the plant
experts was very similar to that of the strategy ‘b’ and
in contrast with the strategy ‘a’. Indeed, the strat-
egy ‘a’ takes into account only the average perme-
ability and whenever a variation of the gates posi-
tion is required in order to improve the permeabil-
ity, the variation is reported to the gates. This leads
to frequent variation in the gates positions and some-
times in abrupt changes. The technicians, on the other
hand, use a more conservative approach that tends to
perform slight modification in the gates position and
rarely abrupt changes.
Summing up the results of the tests of the two
control strategies: strategy ‘a’ gives better automatic
results, but it is less coherent to the technicians’
standard operating practice, thus they can experience
higher efforts in order to follow the plant behavior
when this control strategy is applied. Strategy ‘b’
leads to fairly good results, but it is more coherent
to the standard operating practice.
Finally, it can be noticeable that the advisory sys-
tem has been designed to be improved through its use,
as the overall software system supports data collec-
tion and analysis. After a longer period of use it will
be possible to refine the performances of the proposed
system using the same statistical parameters that sup-
plied the system.
5 CONCLUSION
A new approach based on fuzzy rule-based expertsys-
tems and a new advisory system to control the charg-
ing gates of a sinter plant is presented. Two new con-
trol strategies have been developed and tested on the
field.
Strategy ‘a’ is more invasive within the process
operational conditions, as it aims at maximizing the
productivity without any kind of trade-off. It can be
used when the plant is characterized by lower produc-
tivity (e.g. the plant is restarted after a stoppage): in
these cases the greater the control amount, the shorter
the time elapsed before reaching fair operating condi-
tions.
On the other hand, strategy ‘b’ is more conser-
vative, as it aims at maximizing the productivity but
considers also the stress on the gates’ actuators and
produces less perturbation in the operating conditions
with respect to the other strategy. It can be used when
the plant is characterized by higher productivity and
the machine shows a higher sensitivity to the changes
on the gates.
Real-time tests are still ongoing at the sintering
plant of ILVA S.p.A. (Taranto Works, Italy) and satis-
factory results confirm the goodness of the automatic
control system.
Future work will deal with the development of a
new strategy combining the strong points of the two
developed ones. In detail, this strategy can select au-
tomatically the use of the strategy ‘a’ during the lower
productivity phase of the plant switching on the other
strategy (‘b’) during the phase with high productiv-
ity and vice-versa. In this way a single strategy can
take the best advantages from the two developed ones
achieving good results during all the production phase
of the plant.
ACKNOWLEDGEMENTS
The work described in the present paper was devel-
oped within the project entitled ”New measurement
and control techniques for total control in iron ore
sinter plants” ToSiCo (Contract No. RFSR-CT-2009-
00001) that has received funding from the Research
Fund for Coal and Steel of the European Union. The
sole responsibility of the issues treated in the present
paper lies with the authors; the Commission is not re-
sponsible for any use that may be made of the infor-
mation contained therein.
REFERENCES
Arbeithuber, C., J¨orgl, H. P., and Raml, H. (1995). Fuzzy
control of an iron ore sintering plant. Control Engi-
FCTA2014-InternationalConferenceonFuzzyComputationTheoryandApplications
74