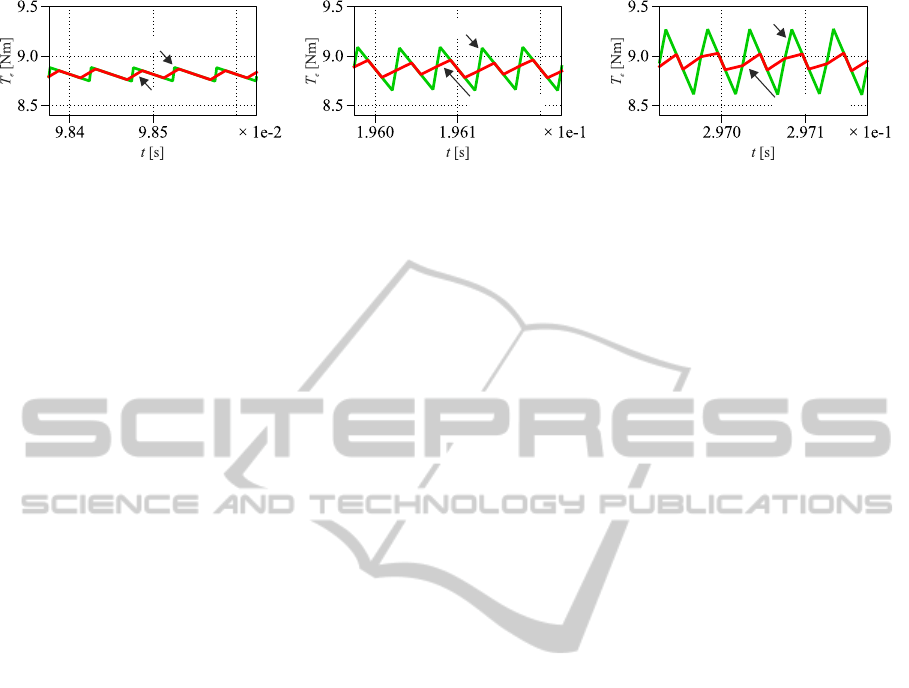
VSI
VMC + VSI
VSI
VMC + VSI
VSI
VMC + VSI
a) b) c)
Figure 7: Electromagnetic torque waveforms of PMSM fed by VSI and VMC + VSI in a steady-state for the related load
torque: a) ω
m
= 10rad/s, b) ω
m
= 50rad/s, c) ω
m
= 100rad/s.
5 CONCLUSIONS
It was found that neural network state feedback
controller can be successfully used to control non-
stationary and non-linear plant (i.e. PMSM fed by
VSI with VMC) in terms of torque ripple minimiza-
tion. Use of the proposed controller causes, that lin-
earization and decoupling process of the plant are not
needed. It was also found that DC voltage of the VSI
can be precisely controlled with the help of an addi-
tional VMC control system.
Based on 2 low-order low-pass filters adaptive for-
mula used to obtain an appropriate inverter gain with
respect to actual value of the reference velocity was
introduced.
Simulation test results confirm similar dynamic
performance and significant torque ripple minimiza-
tion of designed control system in comparison to
PMSM fed by VSI with stationary state feedback con-
troller - torque ripple factor is at least 30% smaller.
Experimental verification of the described con-
trol system with neural network based adaptive state
feedback controller and voltage matching circuit is
planned in the future.
REFERENCES
Ferrari, S. and Stengel, R. F. (2005). Smooth function ap-
proximation using neural networks. IEEE Transac-
tions on Neural Networks, 16(1):24–38.
Grzesiak, L. M. and Tarczewski, T. (2011). Permanent mag-
net synchronous motor discrete linear quadratic speed
controller. In IEEE International Symposium on In-
dustrial Electronics, ISIE 2011, pp. 667–672. IEEE.
Grzesiak, L. M. and Tarczewski, T. (2013). PMSM servo-
drive control system with a state feedback and a
load torque feedforward compensation. COMPEL:
The International Journal for Computation and Math-
ematics in Electrical and Electronic Engineering,
32(1):364–382.
Gulez, K., Adam, A. A., and Pastaci, H. (2008). Torque
ripple and EMI noise minimization in PMSM using
active filter topology and field-oriented control. IEEE
Transactions on Industrial Electronics, 55(1):251–
257.
Hasanien, H. M. (2010). Torque ripple minimization of per-
manent magnet synchronous motor using digital ob-
server controller. Energy Conversion and Manage-
ment, 51(1):98–104.
Huang, S. and Tan, K. K. (2012). Intelligent friction model-
ing and compensation using neural network approxi-
mations. IEEE Transactions on Industrial Electronics,
59(8):3342–3349.
Hung, J. Y. and Ding, Z. (1993). Design of currents to re-
duce torque ripple in brushless permanent magnet mo-
tors. IEE Proceedings B Electric Power Applications,
140(4):260–266.
Jahns, T. M. and Soong, W. L. (1996). Pulsating torque min-
imization techniques for permanent magnet AC motor
drives - a review. IEEE Transactions on Industrial
Electronics, 43(2):321–330.
Kojima, M., Hirabayashi, K., Kawabata, Y., Ejiogu, E. C.,
and Kawabata, T. (2004). Novel vector control system
using deadbeat-controlled PWM inverter with output
LC filter. IEEE Transactions on Industry Applica-
tions, 40(1):162–169.
Krishnan, R. (2010). Permanent Magnet Synchronous and
Brushless DC Motor Drives. CRC Press, New York.
Petrovic, V., Ortega, R., Stankovic, A. M., and Tadmor, G.
(2000). Design and implementation of an adaptive
controller for torque ripple minimization in PM syn-
chronous motors. IEEE Transactions on Power Elec-
tronics, 15(5):871–880.
Qian, W., Panda, S. K., and Xu, J.-X. (2004). Torque ripple
minimization in PM synchronous motors using iter-
ative learning control. IEEE Transactions on Power
Electronics, 19(2):272–279.
Steinke, J. K. (1999). Use of an LC filter to achieve a motor-
friendly performance of the PWM voltage source in-
verter. IEEE Transactions on Energy Conversion,
14(3):649–654.
Tarczewski, T. and Grzesiak, L. M. (2013). PMSM fed
by 3-level NPC sinusoidal inverter with discrete state
feedback controller. In 15th European Conference on
Power Electronics and Applications, EPE 2013, pp.
1–9. IEEE.
Tarczewski, T., Niewiara, L., and Grzesiak, L. M. (2014).
Torque ripple minimization for PMSM using voltage
matching circuit and neural network based adaptive
state feedback control. In 16th European Conference
on Power Electronics and Applications, EPE 2014.
IEEE.
Tewari, A. (2002). Modern Control Design: with MATLAB
and SIMULINK. Wiley, Chichester.
ApplicationofArtificialNeuralNetworkStateFeedbackControllertoTorqueRippleMinimizationofPMSM
369