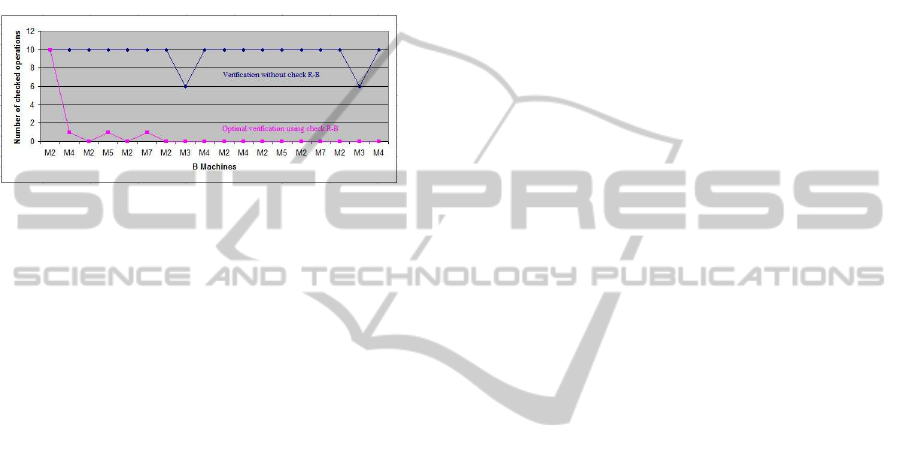
(resp, Meduim, High), the prover checks 20 opera-
tions. When the system is in Light1 and by using the
prototype tool, 11 operations will be verified. Fur-
ther more, if Drill1 breaks down, the system switches
from Light1 to Light2, the prover checks 16 opera-
tions, otherwise 11 operations. These different exper-
imentations clearly show the benefits of the proposed
algorithm. Figure 8, presents the advantages of Check
R-B when the system runs (M2, M4, M2, M5, M2,
M7, M2, M3, M4) in order.
Figure 8: Comparison between verification process with
and without using Check R-B .
6 CONCLUSION
In this paper, we have proposed a new Reconfigurable
B formalism to reconfigure control systems following
the B method. This formalism consists of behavior
and a control modules. The first one is modeled by
different abstract machines describing all the possible
behaviors of the system according to three reconfig-
uration levels : architectural, structural and data lev-
els. The second module allows the system to dynam-
ically switch from one configuration to another dur-
ing a power failure or a user request. The proposed
formalism has been applied to the FESTO system.
We have specified all the different configurations with
B method and have verified all the proof obligations
with the powerful tool B4free. We have also proposed
an optimal algorithm to verify reconfigurable B con-
trol systems. It indicates for a given configuration,
which operations have to be verified. An operation
should be only once checked by the prover. Thus,
from a configuration to another one, we verify only
the new operations. We have proved the optimality
and the efficiency of our algorithm with this origi-
nal tool. We report the experimental results, which
demonstrate an improvement of up to 50% as com-
pared to a direct verification.
This paper is a first step, where we focus on mod-
eling and verification of reconfigurable B centralised
system. Several points will be addressed in the future
work. Firstly, we plan to apply the R-B formalism for
distributed systems. Secondly, we plan to develop a
new verification algorithm for these systems.
REFERENCES
Abrial, J.-R. (1996). The B-Book. Cambridge University
Press.
Behem, P., Benoit, P., and Meynadier, J. (1999). Me-
teor: A successful application of b in a large project.
pages 369–387. In FM99-World Conference on for-
mal Methods in the Development of Computing Sys-
tems, Springer - Verlag.
Casset, L. (2002). Development of an embedded verifier
for java card byte code using formal methods. Formal
methodes, 2391:290–309.
De Palma, N., Bellissard, L., and Riveill, M. (1998).
Dynamic reconfiguration of agent-based applica-
tions. pages 369–387. in Proceedings of the Eu-
ropean SIGOPS Workshop: Support for Compos-
ing Distributed Applications, ACM, Sintra, Portugal,
Springer - Verlag.
Hallerstade, S. (2003). Parallel hardware design in b, in
didier bert. pages 101–102. Formal specification and
Development in Z and B, Springer - Verlag.
Khalgui, M. and Gharbi, A. (2010). Development of an
embedded verifier for java card byte code using for-
mal methods. Ubiquitous Systems and Pervasive Net-
works, 1(1):19–28.
Khalgui, M., Mosbahi, O., Li, Z., and Hanisch, H.-M.
(2011). Reconfigurable multiagent embedded con-
trol systems from modeling to implementation. IEEE
Trans. Computers, 60(4):538–551.
Madlener, F., Weingart, J., and Huss, S. (2010). Verifica-
tion of dynamically reconfigurable embedded systems
by model transformation rules. 4th IEEE/ACM Inter-
national conference on Hardwave-Software Code sign
and System Synthesis (CODES+ISSS 2010), part of
the Embedded Systems Week.
Pouzancare, G. (2003). How to diagnose a modern car with
a formal b model. volume 2651, pages 98–100. For-
mal specification and Development in Z and B, In-
ternational Conference of B and Z Users (ZB2003),
Turku, Finland, Springer - Verlag.
Pouzancare, G. and Pitzalis, J. (2003). Modlisation en b
vnementielle des fonctions mcaniques, lectriques et
informatiques dun vhicule. Technique et Science In-
formatiques, 22(1):119–128.
Pratl, G., Dietrich, D., Hancke, G., and Penzhorn, W.
(2007). A new model for autonomous, networked con-
trol systems. IEEE Transactions on Industrial Infor-
matics, 3(1):21–32.
Theiss, S., Vasyutynsky, V., and Kabitzsch, K. (2009). Soft-
ware agents in industry: A customized framework in
theory and praxis. IEEE Transactions on Industrial
Informatics, 5(2):563–577.
Zhang, J., Khalgui, M., Li, Z.and Senior Member, I., and
Mosbahi, O. (2013). R-tnces: A novel formalism for
reconfigurable discrete event control systems. IEEE
Transactions On Systems, Man, And Cybernetics, Part
A: Systems And Humans, 43(4):757 – 772.
NewSolutionsforModelingandVerificationofB-basedReconfigurableControlSystems
757