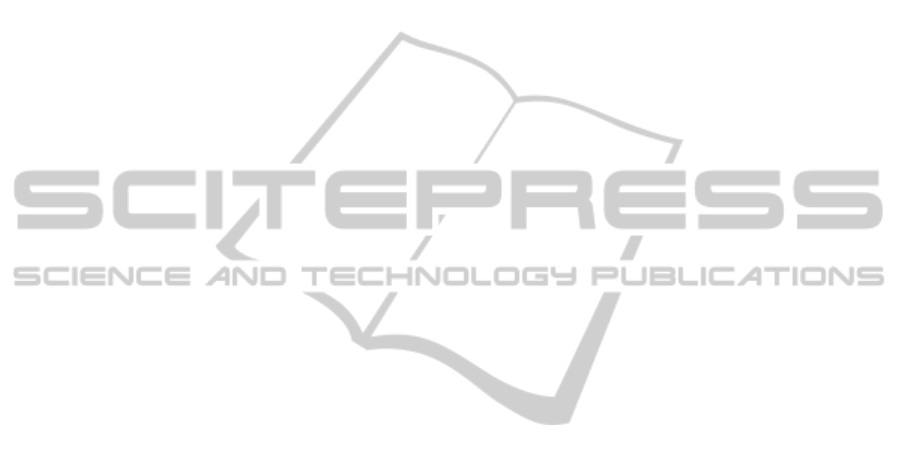
elling of the complex system, such alternative allows
to independently verifying each submodel properties
and having more compact and understandable mod-
els. Using each submodel makes easier the validation
of every step of Dijkstra’s algorithm.
5 CONCLUSIONS
This research work addressed the problem of multi-
objective optimization in oil pipeline network: the
calculation of the shortest reliable path is taking into
account pipes’ length and valves’ dynamic reliability
which varies with time and with conditions of use.
The study proposed, firstly, the definition of dy-
namic reliability and the determination of its pa-
rameters; secondly, the adoption of the scalarization
method in order to transform the multi-objective opti-
mization problem into a shortest path problem solved
by Dijkstra’s algorithm and based on a HLP-nets
model.
The implementation of this algorithm in the
framework of HLP-nets has the important advantage
of avoiding the curse of dimensionality that can ap-
pear in combinatorial optimization problems concern-
ing real pipeline networks. With this framework
the problem dimension is independent of the graph’s
nodes’ number, since the dimension impacts only in
the tokens’ number.
Another important issue is the global network
management when several orders must be satisfied
simultaneously and several non-intercepting align-
ments must be used at the same time. This introduces
additional constrains in the minimal path search that
must be accommodated in the HLP-nets model to pre-
vent conflicts in pipe selection and concatenation.
Maintenance operations must be programmed to
prevent an exaggerated decrease in valves and pumps
reliability. The dynamic reliability, used in this work,
can eventually be used as a trigger to maintenance
plans that must be taken into consideration and rep-
resent another additional constraint in the problem.
These are interesting directions for future re-
search.
REFERENCES
Cacheux, P.-J. and Collas, S. Probability of failure due to
a demand : a concept needing clarification. In 18
ieme
congr
`
es.
Ching-Lai, H. and AbuSyed, M. M. (1979). Multiple ob-
jective decision making, methods and applications: a
state-of-the-art survey. Springer-Verlag.
Cox, D. (1972). Regression models and life tables. Journal
of the Royal Statistical Society, series B, vol. 34, no.
2.
Devooght, J. and Lewins, J. (1997). Dynamic Reliability, in
Advances in Nuclear Science & Technology. Springer
US, Volume 25.
Dijkstra, E. W. (1959). A note on two problems in connex-
ion with graphs. Numerische Mathematik 1, Springer-
Lehrbuch.
Dominique, C., Lyonnet, P., Brissaud, F., and Lanternier,
B. (2007). Mod
´
elisation des taux de d
´
efaillance en
m
´
ecanique. In Performances et Nouvelles Technolo-
gies en Maintenance.
Hahn, B. and Valentine, D. (2013). Essential Matlab for
Engineers and Scientists. Academic Press, London,
5th edition.
Jensen, K. and Kristensen, L. (2009). Coloured Petri Nets
– Modeling and Validation of Concurrent Systems.
Springer-Verlag, Berlin.
Kadri, H. and Zouari, B. (2014). Shortest path search in
dynamic reliability space: Hierarchical coloured petri
nets model and application to a pipeline network. In
6th International Conference on Modelling and Simu-
lation.
Loman, J. and Wendai, W. (2002). On reliability modeling
and analysis of highly reliable large systems. In Pro-
ceedings of Maintainability Symposium. IEEEXplore.
Pagani, E. and Pellegrini, L. (2009). Scalarization and
sensitivity analysis in Vector Optimization. The lin-
ear case. Working Paper Series, Department of Eco-
nomics, University of Verona.
Rojas-D’Onofrio, J., M
´
arquez, J., Boutleux, E., and Niel,
E. (2011). Path search algorithm for connections with
pumps in crude oil pipe networks. In IFAC World
Congress.
SINTEF, I. M. (2002). Offshore Reliability Data Handbook.
Det Norske Veritas (DNV).
Tyrone, L. and Jones, T. (2011). Handbook of Reliabil-
ity Prediction Procedures for Mechanical Eqfuipment.
Naval Surface Warfare Center West Bethesda, Mary-
land, 2nd edition.
Westergaard, M. and Kristensen, L. (2009). The access/cpn
framework: A tool for interacting with the cpn tools
simulator. In 30th International Conference on Appli-
cations and Theory of Petri Nets.
SIMULTECH2014-4thInternationalConferenceonSimulationandModelingMethodologies,Technologiesand
Applications
218