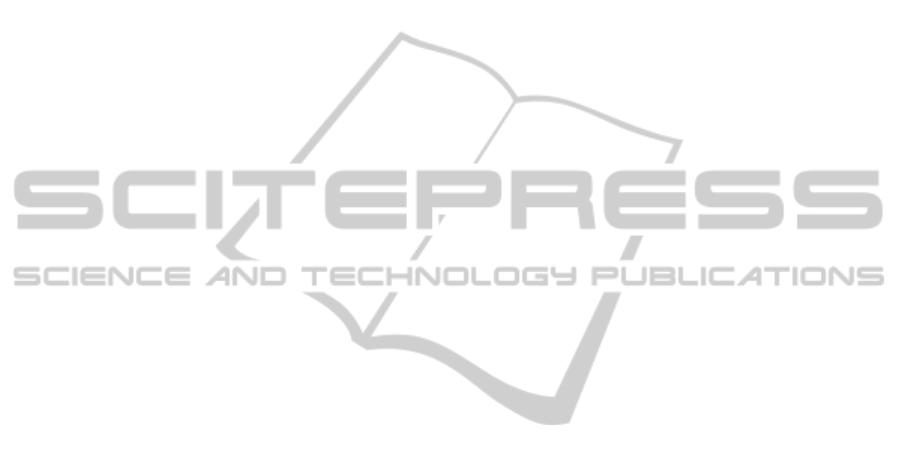
5 CONCLUSION
The problem of the minimal-cost trajectory planning
for a given end-effector motion law and a relaxed
path is proposed in this paper. We define this prob-
lem as domain-independent and formulate it with no
regard to the solution method. As a consequence,
we do not impose any requirement on the constraints
or the cost function. It was shown that relaxing the
path can lead to a significant trajectory cost reduc-
tion. This improvement is achieved with no depen-
dency on whether the motion law was defined by an
industrial process or was optimized. The limitation of
the approach follows from its generality. It cannot be
applied in real time, as the used heuristic is computa-
tionally slower than the convex optimization solvers.
One way to achieve better results is to generalize
the problem further by relaxing the motion law, as in
the current problem formulation it is considered to be
given and fixed. Currently, we considered only one
IK solution, e.g., “elbow-up”. However, making use
of the multiplicity of IK solutions might provide bet-
ter results. Robot base location in the environment
greatly influences the cost of the C-space trajectory
obtained for the end-effector path. In many applica-
tions robot base location is not important, or at least
can vary within a certain area. In this paper a greedy
local search method was presented. However, the po-
tential of the problem can be utilized evenmore by ap-
plying more sophisticated search techniques that have
mechanisms to avoid local optimum, e.g., Genetic Al-
gorithm or Variable Neighborhood Search.
ACKNOWLEDGEMENTS
The work in this paper is partly funded by the German
Ministry of Education and Research (BMBF) within
the Forschungscampus STIMULATE (grant number
03FO16101A).
REFERENCES
Alatartsev, S., Mersheeva, V., Augustine, M., and Ortmeier,
F. (2013). On optimizing a sequence of robotic tasks.
In IEEE/RSJ International Conference on Intelligent
Robots and Systems (IROS).
Alatartsev, S. and Ortmeier, F. (2014). Improving the Se-
quence of Robotic Tasks with Freedom of Execution.
In IEEE/RSJ International Conference on Intelligent
Robots and Systems (IROS).
Aspragathos, N. (1998). Cartesian trajectory generation un-
der bounded position deviation. Mechanism and ma-
chine theory, 33(6):697–709.
Ata, A. A. (2007). Optimal trajectory planning of manipu-
lators: A review. Journal of Engineering Science and
Technology, 1:32.
Ata, A. A. and Myo, T. R. (2005). Optimal point-to-point
trajectory tracking of redundant manipulators using
generalized pattern search. International Journal of
Advanced Robotic Systems, 2(3).
Berenson, D., Srinivasa, S., and Kuffner, J. (2011). Task
space regions: A framework for pose-constrained ma-
nipulation planning. International Journal of Robotics
Research (IJRR), 30(12):1435–1460.
Biagiotti, L. and Melchiorri, C. (2008). Trajectory Planning
for Automatic Machines and Robots. Springer Berlin
Heidelberg.
Chettibi, T., Lehtihet, H., Haddad, M., and Hanchi, S.
(2004). Minimum cost trajectory planning for indus-
trial robots. European Journal of Mechanics-A/Solids,
23(4):703–715.
Craig, J. (2005). Introduction to Robotics: Mechanics and
Control. Pearson.
Dror, M., Efrat, A., Lubiw, A., and Mitchell, J. S. B. (2003).
Touring a sequence of polygons. In 35th annual ACM
symposium on Theory of Computing, pages 473–482.
ACM Press.
From, P. J., Gunnar, J., and Gravdahl, J. T. (2011). Optimal
paint gun orientation in spray paint applications – ex-
perimental results. IEEE Transactions on Automation
Science and Engineering, 8(2):438–442.
Gasparetto, A. and Zanotto, V. (2010). Optimal trajectory
planning for industrial robots. Advances in Engineer-
ing Software, 41:548–556.
Hooke, R. and Jeeves, T. A. (1961). Direct search solution
of numerical and statistical problems. Journal of the
ACM, 8(2):212–229.
Kolter, J. Z. and Ng, A. Y. (2009). Task-space trajectories
via cubic spline optimization. In IEEE International
Conference on Robotics and Automation (ICRA).
Kov´acs, A. (2013). Task sequencing for remote laserweld-
ing in the automotive industry. In 23rd International
Conference on Automated Planning and Scheduling
(ICAPS).
Liu, H., Lai, X., and Wu, W. (2013). Time-optimal and jerk-
continuous trajectory planning for robot manipulators
with kinematic constraints. Robotics and Computer-
Integrated Manufacturing, 29(2):309–317.
Macfarlane, S. and Croft, E. A. (2003). Jerk-bounded ma-
nipulator trajectory planning: design for real-time ap-
plications. IEEE Transactions on Robotics and Au-
tomation, 19(1):42–52.
Olabi, A., B´ear´ee, R., Gibaru, O., and Damak, M. (2010).
Feedrate planning for machining with industrial six-
axis robots. Control Engineering Practice, 18(5):471–
482.
Pan, X., Li, F., and Klette, R. (2010). Approximate short-
est path algorithms for sequences of pairwise disjoint
simple polygons. In Canadian Conference on Com-
putational Geometry, pages 175–178.
Simon, D. (1993). The application of neural networks to
optimal robot trajectory planning. Robotics and Au-
tonomous Systems, 11:23–34.
ICINCO2014-11thInternationalConferenceonInformaticsinControl,AutomationandRobotics
390