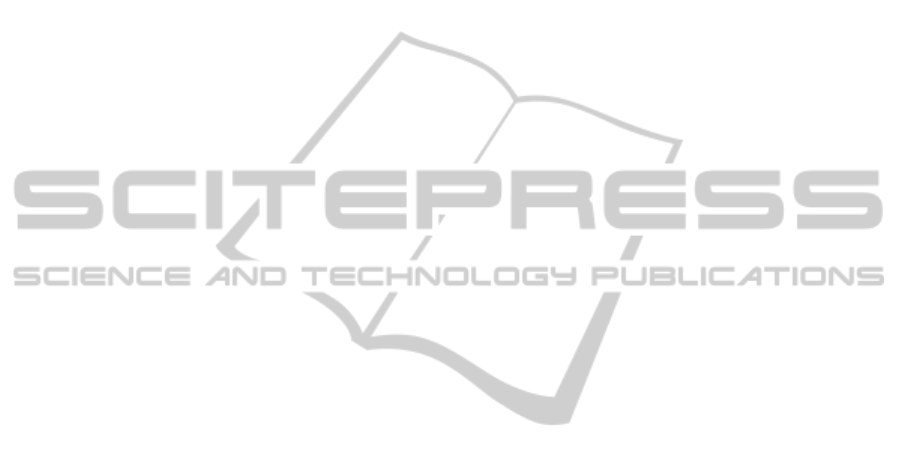
open pit mine production scheduling problem.
Computers & OR 37 (9), pp. 1641-1647.
Caccetta, L., Hill, S., 2003. An application of branch and
cut to open pit mine scheduling. Journal of Global
Optimization, 27 (2–3), pp. 349–365.
Chanda, E.K.C., Dagdelen, K., 1995. Optimal blending of
mine production using goal programming and
interactive graphics systems, International Journal of
surface Mining, Reclamation and the Environment,
Vol. 9, pp. 203-208.
Chicoisne, R., Espinoza, D., Goycoolea, M., Moreno E.,
Rubio E., 2012. A New Algorithm for the Open-Pit
Mine Production Scheduling Problem. Operations
Research 60 (3), pp. 517-528.
Crawford, B., Soto, R., Monfroy, E., Palma, W., Castro,
C., Paredes, F., 2013. Parameter tuning of a choice-
function based hyperheuristic using particle swarm
optimization. Expert Syst. Appl. 40 (5), pp. 1690-1695.
Crawford, B., Soto, R., Monfroy, E., Castro, C., Palma,
W., Paredes F, 2013. A hybrid soft computing
approach for subset problems Mathematical Problems
in Engineering, Vol. 2013, Article ID 716069, 12
pages.
Denby, B., Schofield, D., 1994. Open-pit design and
scheduling by use of genetic algorithms. Transactions
of the Institution of Mining and Metallurgy, Section A:
Mining Industry, 103, A21–A26.
Espinoza, D., Goycoolea, M., Moreno, E., Newman, A,
2012. MineLib: A Library of Open Pit Mining
Problems. Ann. Oper. Res. 206 (1), pp. 91-114.
Lamghari, A., Dimitrakopoulos, R, 2012. A diversified
Tabu search approach for the open-pit mine
production scheduling problem with metal uncertainty.
European Journal of Operational Research 222 (3),
pp. 642-652.
Gholamnejad, J., Osanloo, M., Karimi, B., 2006. A
Chance-Constrained Programming Approach for Open
Pit Long-Term Production Scheduling in Stochastic
Environments. The Journal of the South African
Institute of Mining and Metallurgy, Vol. 106, pp.105-
114.
Gholamnejad, J., Osanloo, M., Khorram, E, 2008. A
Chance Constrained Integer Programming Model for
Open Pit Long-Term Production Planning.
International Journal of Engineering Transactions A:
Basics (21) 4, pp. 407-418.
Marcotte, D., Caron, J., 2013. Ultimate open pit stochastic
optimization. Computers & Geosciences Vol. 51, pp.
238-246.
Monfroy, E., Castro, C., Crawford, B., Soto, R., Paredes,
F., Figueroa, C., 2013. A reactive and hybrid
constraint solver. J. Exp. Theor. Artif. Intell. 25 (1),
pp. 1-22.
Pizarro, P., Rivera, G., Soto, R., Crawford, B., Castro, C.,
Monfroy, E., 2011. Constraint-Based Nurse Rostering
for the Valparaíso Clinic Center in Chile. In:
Stephanidis, C. (ed.) Posters, HCII 2011, Part II.
CCIS, vol. 174, pp.448-452, Springer.
Ramazan, S., 2007. The new Fundamental Tree Algorithm
for production scheduling of open pit mines. European
Journal of Operational Research 177(2), pp.1153-
1166.
Soto, R., Crawford, B., Galleguillos, C., Monfroy, E.,
Paredes, F, 2013. A hybrid AC3-tabu search algorithm
for solving Sudoku puzzles. Expert Syst. Appl. 40(15),
pp. 5817-5821.
Soto, R., Crawford, B., Misra, S., Palma, W., Monfroy, E.,
Castro, C., Paredes, F., 2013. Choice functions for
autonomous search in constraint programming: GA vs.
PSO. Tehnicki Vjesnik. Vol. 20(3), pp. 525-531.
Soto, R., Crawford, B., Misra, S., Monfroy, E., Palma, W.,
Castro, C., Paredes, F., 2014. Constraint Programming
for optimal design of architectures for water
distribution tanks and reservoirs: a case study.
Tehnicki Vjesnik. Vol. 21(1).
Soto, R., Kjellerstrand, H., Duran, O., Crawford, B.,
Monfroy, E., Paredes, F., 2012. Cell formation in
group technology using constraint programming and
Boolean satisfiability. Expert Syst. Appl. 39(13), pp.
11423-11427.
Zhang, M., 2006. Combining genetic algorithms and
topological sort to optimize open-pit mine plans. In
proceedings of the 15th mine planning and equipment
selection, pp. 1234–1239.
SolvingOpen-PitLong-TermProductionPlanningProblemswithConstraintProgramming-APerformanceEvaluation
77