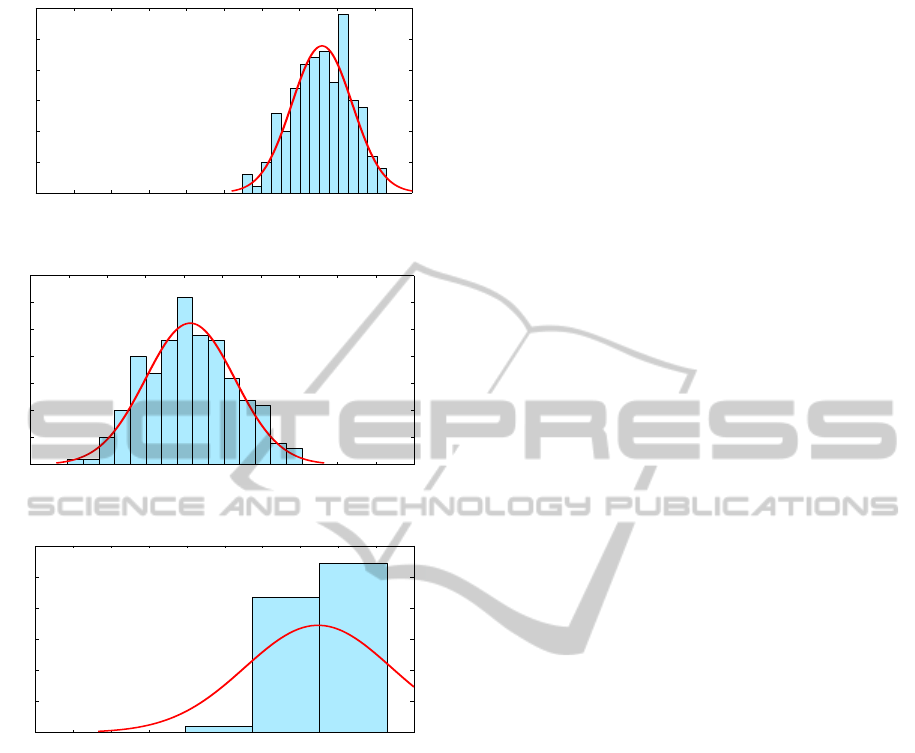
0.95 1 1.05 1.1 1.15 1.2 1.25 1.3 1.35 1.4
x 10
−4
0
5
10
15
20
25
30
y(k) [M
ts
]
Probability
Figure 12: Probability distribution of y
cal
(k) using M
ts
.
0.9 0.95 1 1.05 1.1 1.15 1.2 1.25 1.3 1.35 1.4
x 10
−4
0
5
10
15
20
25
30
35
y(k)[M
tp
]
Probability
Figure 13: Probability distribution of y
cal
(k) using M
tp
.
0.95 1 1.05 1.1 1.15 1.2 1.25 1.3 1.35 1.4
x 10
−4
0
20
40
60
80
100
120
y(k)[model]
Probability
Figure 14: Probability distribution of y
mod
(k) using model.
value of data distribution seems to be equal. That
shows the model and experimental results are seems
to be satisfactory. In figures 12 and 13, the distribu-
tion of y
cal
measured by M
tp
and y
mod
are observed to
be different mean value.
5 CONCLUSIONS
A discrete-time model is developed and validated
with the static and transient mode. The model is also
validated using the real engine experimental data. The
y(k) calculated using the two methods of total charge
estimation and y (k) from model are compared. The
error in y(k) in case of M
tp
(k) is higher than the cal-
culated by M
ts
(k) due to the propagation of error in
different measured variables. In further continuing of
this research work, validation of model will be done
based on the y(k) measured using M
tp
by the adding
of some correction factor to minimized the error at
different operating condition of engine data. A ob-
server will be established to control the air-fuel ratio,
torque and RGF using above model on cycle basis.
ACKNOWLEDGEMENTS
The authors wish to acknowledge the Toyota Motors
Corporation for the supporting in this research and
helpful discussions and Mr. Mingxin Kang for the
helping in conduct the experiment:
REFERENCES
Rizzoni G. (1999). A stochastic model for the indicated
pressure process and the dynamics of internal com-
bustion engine. IEEE Trans. Veh. Technol., vol.38, no.
3, pp.180-192, Aug. 1989.
Peyton Jones, J. C., Roberts J. B., and Landsborough K.J.
(2010). A cumulative-summation-based stochastic
knock controller. Proc. Inst. Mech. Eng., vol.224, no.
7, pp. 969-983, 2010.
Clerk, D. (1886). The gas engine. 1st ed., Longmans, Green
and Co., 1886.
Daw, C. S., Finney, C. E. A., Green, J. B., Kennel, M. B.,
and Thomas, J. F. (1996). A simple model for cyclic
variations in a spark-ignition engine. SAE Warrendale,
PA,.962086, May 1996.
Daw, C. S., Finney, C. E. A., Kennel, M. B., and Connolly,
F. T. (1998). Observing and modeling nonlinear dy-
namics in an internal combustion engine. Phys. Rev.
E., vol.57, no.3, pp. 2811-2819, 1998.
Arsie, I., Rocco, D., L., Pianese, C., and Cesare, M., D.
(2013). Estimation of in-cylinder mass and AFR by
cylinder pressure measurement in automotive Diesel
engines. IFAC World Congress, 2013.
Desantes, J. M., Galindo, J., Guardiola, C., and Dolz, V.
(2010). Air mass flow estimation in turbocharged
diesel engines from in-cylinder pressure measure-
ment. Experimental Thermal and Fluid Science, vol.
34, pp. 37-47, 2010.
Yang, J., Shen, T., and Jiao, X. (2010). Model-based
stochastic optimal air-fuel ratio control with Residual
gas fraction of spark ignition engine IEEE, 2013.
Jonathan, B. V., Brian, C. K., Jagannathan, S., and
Drallmeier, J.,M (2008). Optput feedback controller
for operation of spark ignition engines at lean con-
ditions using neural networks. IEEE, vol. 16, no. 2,
March 2008.
SIMULTECH2014-4thInternationalConferenceonSimulationandModelingMethodologies,Technologiesand
Applications
750