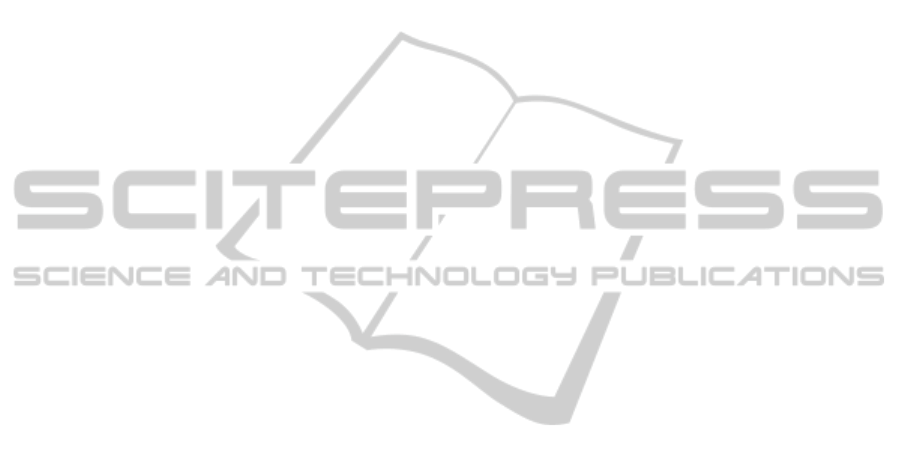
ing from this framework are more suitable to be im-
plemented in the real world.
In order to provide a study case, we illustrate the
proposed framework through a real-world simulator
in the field of electric railways. We will analyze the
simulators characteristics, establishing a correspon-
dence to the different issues of the framework. The
aim of that simulator, presented in (Gomez et al.,
2012), is to design optimal configurations of over-
head line deployments on railway switches. Starting
from a set of parameters with regard to both infras-
tructure and train, the simulator generates different
deployments of the overhead infrastructure. For each
deployment, the simulator reproduces the pantograph
behaviour of the train running across the switch, tak-
ing into account pantograph and wire positions, cate-
nary geometry, tension of the wires, angles of attack,
and more. All these factors can influence the viability
of a solution, and thereby they must be considered.
Finally, the best deployment is selected, on the ba-
sis of several optimization metrics adopted from legal
normative and experts of the field. Therefore, more
than solving a particular set of equations, the simula-
tor takes into account the whole design process.
The paper is structured as follows: Section 2 de-
scribes the simulation framework proposed. Section
3 analyses in detail the railway overhead air switch
problem. Section 4 describes the architecture of the
simulator, and how it corresponds to the proposed
framework. Section 5 evaluates the simulator, indi-
cating times spent on each one of the framework is-
sues. Finally, conclusions, final remarks, and future
work are presented in Section 6.
2 SIMULATION FRAMEWORK
Railway infrastructures are considered critical sys-
tems, with requirements of efficiency, security and
safety, and hence they should be optimized. Nev-
ertheless, performing a high number of experiments
with real systems (tracks, locomotives, electric instal-
lations, etc.) is impracticable in terms of time and
money. The main goal of a simulator, in the field
of railway infrastructure design, is to simulate experi-
mental designs or prototypesto evaluate if they are ac-
ceptable or not, or to provide a degree of fitness. This
procedure is composed of several tasks: first, a candi-
date solution must be selected, either being provided
by the user, or being generated by the simulator itself.
Then, the simulation is performed and the results are
analysed. The candidate solution is scored, and a de-
cision to accept it or reject it is taken. This proce-
dure is repeated across multiple fields in this area. In
railway dynamics, rail-vehicle interaction is analysed,
aiming to get new designs of rails and bogies which
may reduce wear and breakdowns. In overhead con-
tact line designs, structural behaviour (Nejlaoui et al.,
2013) of poles and portal frames are evaluated, check-
ing their feasibility (Saa et al., 2012). In the field of
energy provisioning, a proposal of electric installation
locations may be simulated checking whether energy
is available to all planned trains (Abrahamsson et al.,
2013). (Hani et al., 2006) provides a simulation-based
optimization in order to provide the best building po-
sitions in a railway maintenance facility.
Although this general structure is present in most
railway infrastructure simulators, it may not be suf-
ficient to grant an acceptable degree of productivity,
and should be enhanced. A simulator in railway in-
frastructure design must not be restricted to evalu-
ate solutions provided by the user, but also it should
find acceptable solutions by itself, with a high degree
of fitness, and in a reasonable amount of time. To
achieve these targets we present a simulation frame-
work, which allows to increase the output of simu-
lators by covering more capabilities than the main
procedure described before. Our enhancements are
focused on four main issues below addressed. The
sources of this approach are: railway company ex-
perts, railway infrastructure design and planning pro-
cesses described in (Kiessling et al., 2009), and previ-
ous works in this area made by the authors (Carretero
et al., 2003) (Saa et al., 2012).
First of all, a trade-off between accuracy and com-
plexity is required when designing a simulator. Pro-
ductivity issues in railway industry require not to
waste so much time when evaluating a single solu-
tion, as the design process may require to evaluate a
lot of candidate solutions. There is a relationship be-
tween the accuracy of the model and the complexity
of the simulation. On the one hand, accurate mod-
els are usually hard to simulate, and require more and
more operations, so the more accurate is the model,
the more complex it is, and the more time is needed
to reach the solution. On the other hand, accurate
models are likely to reproduce real results. Optimal
balance between accuracy and simulation may be dif-
ferent in different design processes, but we state that
an efficient simulator should simulate and evaluate a
single candidate solution in the lowest possible time.
We state that an acceptable threshold to be productive
is to simulate and evaluate a candidate solution in less
than one hour.
In the second place, automatic generation and
simulation of solutions falls outside the scope of most
simulators. Therefore, the user must feed the simula-
tor providing new possible solutions, which leads to
SIMULTECH2014-4thInternationalConferenceonSimulationandModelingMethodologies,Technologiesand
Applications
72