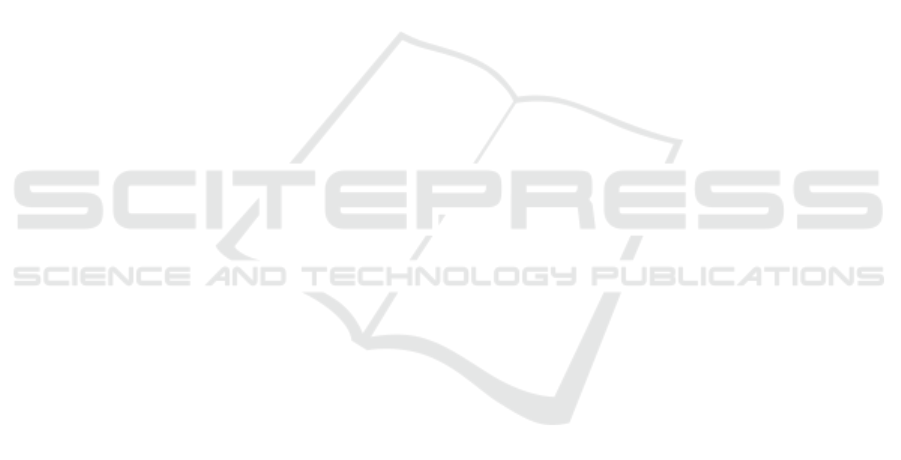
Flexible Shape Measurement System for Chemical Plant Using
Magnetic Sensors
Kumiko Yoshida
1
and Kikuhito Kawasue
2
1
Interdisciplinary Graduate School of Agriculture and Engineering, University of Miyazaki, 1-1 Gakuen Kibanadai Nishi,
Miyazaki, Japan
2
Department of Environmental Robotics, University of Miyazaki, 1-1Gakuen Kibanadai Nishi, Miyazaki, Japan
Keywords: Computer Vision, Pipe Measurement, Magnetic Sensor, CCD Camera, Point Cloud.
Abstract: We propose a flexible computer vision system using magnetic sensors. The system enables a flexible free
scanning of a CCD camera and a laser slit using 3D magnetic sensors. Many numbers of views of each
model from different angles can be taken on measuring the configuration between a CCD camera and a laser
slit projector simultaneously. The information of different views is combined to reconstruct the 3D object
on a computer display. In this paper, the application for pipe measurement is introduced. Experimental
results show the feasibility of our system.
1 INTRODUCTION
Replacement or construction of new pipes is often
carried out for the renewal of the superannuated
facilities in a chemical plant and general factory.
Generally, as the facilities in the plant are running
continuously, the period of the replacement work
should be minimum time to keep the productivity. In
order to cope with this requirement, detailed and
exact data (drawing) of the pipe arrangements are
indispensable. However, almost all drawings do not
correctly match with the state of current pipe
arrangements in the factory. Therefore, the re-
measurement of the pipes is required frequently at
the plant. Generally, the re-measurement is
conducted by manually using a metal tape measure
etc. and it causes the redo of the replacement or
construction works since the accuracy of the manual
measurement is uncertain.
Recently, the three-dimensional measurement
systems with a laser scanner are widely used in
various fields (Faugeras, 1996; Ochiai, 1988; Torras,
1992). These systems have begun to be utilized also
for the equipment measurement in chemical plants.
The measurement system can obtain thousands of
point cloud data with three-dimensional position in a
few second. Point cloud data are sets of vertices in a
three-dimensional coordinate system. The point
cloud data are useful for the fundamental data to
grasp the situation of the facilities in the plant. In the
typical measurement system with a laser scanner, an
infrared laser is sent out and reflected back to the
system. The distance is measured by the time of
flight of the laser pulse between the device and
target, or the shift in the wavelength of the return
beam(Pueschel, 2013). However, since these laser
scanners are generally fixed on the stable ground
with a tripod, the setting position is restricted and
the unmeasurable area are existed such as the narrow
or pipes crowded area etc. These areas have to be
measured by conventional way using metal measure
etc. Therefore hand held measurement system for
the measurement in such a crowded area has been
required.
In this paper, hand held measuring system using
magnetic sensors is introduced. This system is based
on the slit-ray projection method. Slit-ray is
projected on the surface of an object and the
reflected light is recorded by a CCD camera. Three-
dimensional position on the slit is calculated on
considering the configuration of the CCD and the
laser projector. Proposed system with magnetic
sensors enables us a separated free scanning of each
of a CCD camera and a laser slit projector. The
magnetic receiver (Polhemus Inc.) is attached in
each of a CCD camera and a laser projector. The
magnetic transmitter is placed on the fixed table and
the magnetic fields are generated from the
transmitter. The magnetic receiver detects the each
three-dimensional position and the orientation of the
758
Yoshida K. and Kawasue K..
Flexible Shape Measurement System for Chemical Plant Using Magnetic Sensors.
DOI: 10.5220/0005097707580763
In Proceedings of the 11th International Conference on Informatics in Control, Automation and Robotics (ICINCO-2014), pages 758-763
ISBN: 978-989-758-039-0
Copyright
c
2014 SCITEPRESS (Science and Technology Publications, Lda.)