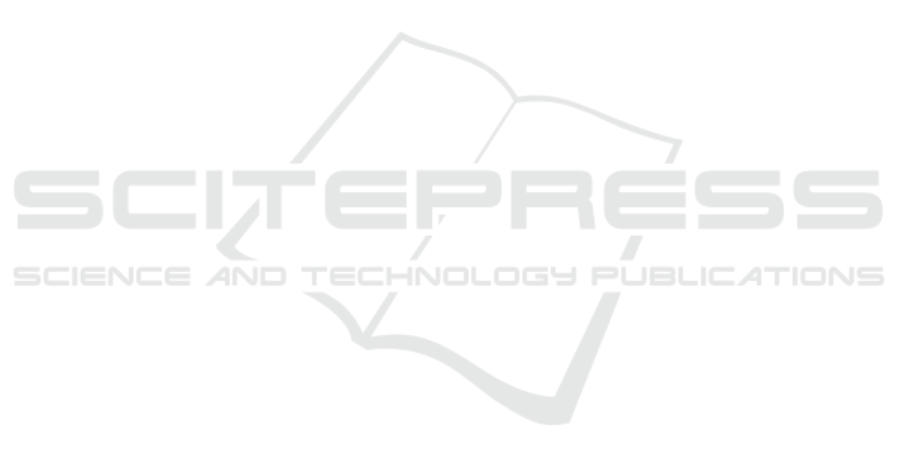
Design of a Multi-robot Bin Packing System in an Automatic
Warehouse
S. J. You and S. H. Ji
Korea Institute of Industrial Technology, Sa-3-dong, Sangrok-gu, Ansan-si, KyungKi-do, South Korea
Keywords: Automatic Warehouse, Bin Packing System, Multi-robots, Mobile-robot Motion Planning, Collision Model.
Abstract: It is possible to reconfigure supply chains with less cost and time if we use the mobile-robot bin packing
system. So, many companies attempt at adopting mobile robots as their new carrier in their own warehouse.
However, it is difficult to utilize indoor service robots as a carrier due to the localization problem, the safety
problem, and the narrow bin packing environment. So we propose a practically applicable solution
technique for a multi-robot bin packing system in an automatic warehouse, which assures a reasonable
safety, computation time and a real world application for more than 3 multi-robots. First, design criteria for
out bin packing system are introduced. Second, we suggest some sketch of robot mechanical parts. Finally,
the method of managing multi-robots in an automatic warehouse robot design with a collision motion
planner is proposed.
1 INTRODUCTION
Multi-agent motion planning is one of the interesting
and essential research fields in robotics. The demand
for various specialized robots has been increasing
rapidly with the advancement of robot technology.
For example, it is possible to reconfigure supply
chains with less cost and time if we use the mobile-
robot bin packing system. So, many companies
attempt at adopting mobile robots as their new
carrier in their own warehouse. However, it is
difficult to utilize indoor service robots as a carrier
due to the localization problem, the safety problem,
and the narrow bin packing environment. So we
propose a practically applicable solution technique
for a multi-robot bin packing system in an automatic
warehouse, which assures a reasonable safety,
computation time and a real world application for
more than 3 multi-robots. First, design criteria for
out bin packing system are introduced. Second, we
suggest some sketch of robot mechanical parts.
Finally, the method of managing multi-robots in an
automatic warehouse robot design with a collision
motion planner is proposed
Multi-agent motion planning is still a challenging
field of research, having some technical difficulties
in resolving conflict among agents. The centralized
approaches have been faced with problems such as
the curse of dimensionality, complexity,
computational difficulty, and NP-hard problem
(Canny, 1988); (Akella, 2002).
To overcome these problems in the approach, we
proposed the extended collision map method (Ji,
2007). We modified the collision map such that the
method enables N agents to proceed with the
collision-free operation according to the priority by
going on the collision avoidance process one after
another from the highest priority agent. Yet, in this
method, the mutual relation regarding the collision
region among agents was not analyzed.
In this regard, in this paper the mutual relation
regarding the collision region is analyzed, and based
upon the studied collision features, (M,D) network
model which can express the traveling features of
multi agent is shown. (M,D) network model can
express not only the collision features between two
agents but also the complicated mutual interference
among more than three agents. Likewise, the
collision-free operation of multi agent can be
designed and the operating finish time of agents can
be figured by using (M,D) network model.
The remainder of the paper is organized as
follows: Section 2 defines design criteria for our bin
packing system and some sketch of robot
mechanical parts. Section 3 presents the concept of
the key technique of this paper – Collision model.
Section 4 provides the way how to plan collision-
533
J. You S. and H. Ji S..
Design of a Multi-robot Bin Packing System in an Automatic Warehouse.
DOI: 10.5220/0005098505330538
In Proceedings of the 11th International Conference on Informatics in Control, Automation and Robotics (ICINCO-2014), pages 533-538
ISBN: 978-989-758-040-6
Copyright
c
2014 SCITEPRESS (Science and Technology Publications, Lda.)