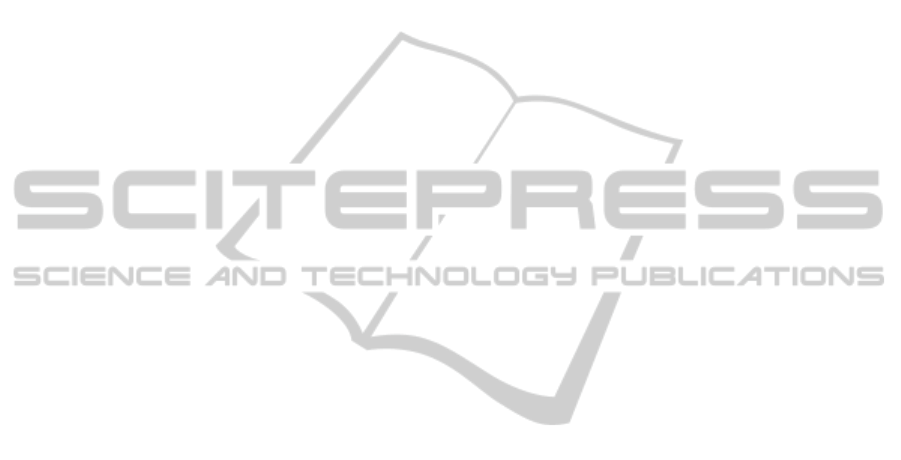
cession machining of aircraft parts.. For the consid-
ered application area, the technological process gen-
erates essential interaction between the workpiece
and manipulator, which causes non-negligible de-
flections of the end-effector. To compensate related
positioning errors on the control level (via adjusting
a target trajectory), an accurate but simple enough
elasto-static model is required. In practice, the de-
sired model is not usually provided by robot manu-
factures and should be obtained from dedicated ex-
perimental study. Let us apply the developed tech-
nique to get the desired model and to identify its pa-
rameters in real industrial environment.
The considered manipulator contains 7 links sep-
arated by 6 actuated joints. Taking into account that
in general the elastostatic properties of each link are
defined by 6x6 stiffness matrix, the complete but
obviously redundant model contains 258 parameters.
As a result of application model reduction tech-
niques (M1-M5), the number of parameters to be
identified has been reduced down to 26. More details
on each step are given in 0. Additional restrictions
here are caused by the partial-pose measurement
technique and the gravity-based loading generating
the desired deflections. Relevant experimental setup
is presented in 0. Because of such measurement
method, 10 elastostatic parameters are not identifia-
ble from the available measurement data. The ma-
nipulator configurations for the elastostatic calibra-
tion were generated using the design of experiments
and previously developed test-pose technique, which
is based on the industry-oriented performance meas-
ure (Klimchik, Wu et al., 2012). Another particulari-
ty of the industrial robot KUKA KR270 that should
be taken into account in an accurate elasto-staic
model is a gravity compensator that is attached in
parallel to the second actuated joint. Its equivalent
model was presented in (Klimchik, Wu et al., 2013).
In the frame of the complete and irreducible model,
the gravity compensator impact is taken into account
by introducing a configuration dependant virtual
spring in the second joint. More details on this ap-
proach are given in (Klimchik, Wu et al., 2013).
In order to ensure higher identification accuracy,
the measurement configurations have been selected
using the design of experiment theory. In contrast to
other works, an industry-oriented performance
measure has been used (Wu, Klimchik et al., 2013),
which evaluates the robot positioning accuracy after
calibration. In total, 15 measurement configurations
for 5 different angles q
2
have been generated.
For the comparison purposes, calibration was
performed using several elastostatic models that dif-
fer in their basic assumptions: (i) complete irreduci-
ble stiffness model and (ii) conventional model for
the manipulator with rigid links and compliant actu-
ated joints. Here, conventional elastostatic models J1
and J2 take into account the actuated joint compli-
ances only. Both models (complete and reduced
ones) have been examined with and without taking
into account the effect of the gravity compensator.
The obtained results are summarized in 0 showing
capability to compensate the compliance errors us-
ing different elastostatic models. As follows from
them, the lowest compliance errors can be achieved
using the model C2 (obtained using the developed
model reduction technique), which ensures the posi-
tional accuracy 0.21 mm. In contrast, the conven-
tional elasto-static model with rigid links gives accu-
racy 3.5 times worse comparing to model C2. The
difference in the efficiency of the compliance errors
compensation between the models J1/J2 and C1/C2
confirms that link compliances have essential impact
on the robot positioning accuracy and cannot be ne-
glected in accurate manufacturing. According to ex-
perimental results presented in 0, by means of the
complete elastostatic model, it is possible to com-
pensate 95% of the compliance errors. In contrast,
using the conventional model that takes into account
the joint elasticity’s merely, only 84% of positioning
errors caused by external force can be compensated.
This emphasizes the advantage of the proposed
model. The histograms of the errors distribution for
the model C2 (0) show that the non-compensated
compliance errors in all directions are unbiased and
almost normally distributed.
Hence, using the developed low-order stiffness
model for the compliance error compensation gives
essential improvement of the precision for the robot-
ic based milling. It allowed us to compensate more
than 95% of deflections caused by external loading
and to guarantee the precision of about 0.2 mm un-
der the loading of 2.5 kN (it is comparable with the
robot repeatability of 0.06 mm).
5 CONCLUSION
The paper deals with the problem of the manipulator
stiffness modeling. The main attention is paid to the
elastostatic parameters identification and model re-
duction. In contrast to previous works, the manipula-
tor stiffness properties are described by the sophisti-
cated model, which takes into account the flexibili-
ties of all mechanical elements described by 6×6
stiffness matrices. This obviously yields extremely
high number of the model parameters that cannot be
CompleteStiffnessModelforaSerialRobot
199