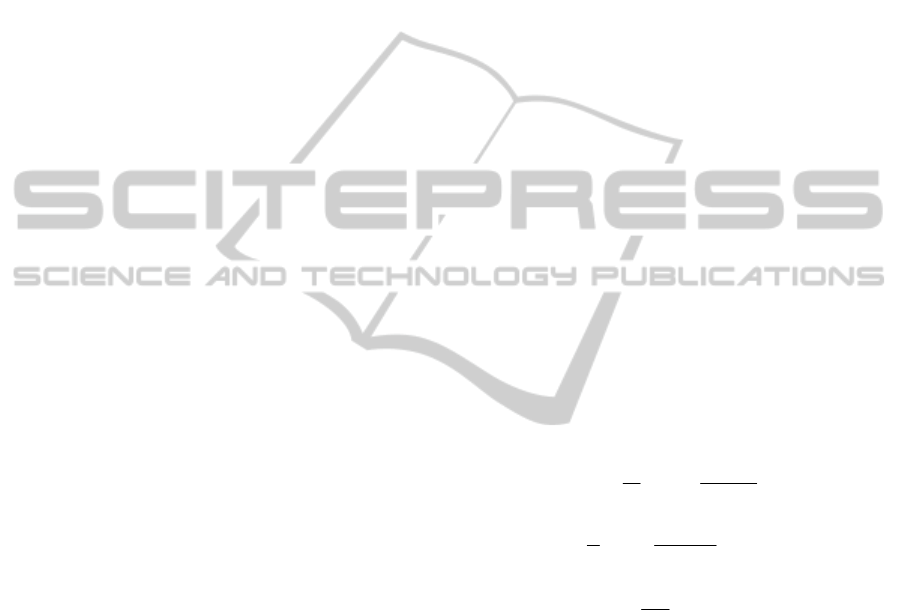
(George, 1994). Now-a-days Evolutionary methods
like Genetic Algorithm (GA), biologically inspired
methods like Particle Swarm Optimization (PSO),
Ant Colony optimisation (ACO) etc. are used for
tuning the parameters of the controllers. These new
tuning techniques can efficiently solve complex
problems like nonlinearity in the plant, variable
speed problems, where the conventional methods
may not optimize the controller parameter so
accurately. PSO is another Heuristic approach
which is inspired by the ability of flock of birds or
herd of animals to adapt to their environment. It was
developed in 1995 by James Kennedy and Russ
Eberhart while attempting to simulate the
choreographed, graceful motion of the swarm of
birds as a part of socio-cognitive study investigating
the motion of collective intelligence in biological
population. In PSO, a set of randomly generated
solutions propagates in the designed space towards
the optimal solution over a number of iteration based
on large amount of information about the designed
space (Kennedy, 1995). Both GA and PSO are
similar in the sense that these two techniques are
population based heuristic search methods and they
approach for the optimal solution by updating
generations. Since these approaches are supposed to
find a solution to a given objective function but
employ different strategies and computation effort, it
is appropriate to compare their performance.
In citation (Hameyer, 2008) the authors perform
a multiobjective optimization in a SRM aiming both
to maximize the mitigation of the torque ripple and
to minimize the degradations of the starting and
mean torques. The technique was applied on the
optimization of some rotor geometrical parameters
with the aid of finite element simulations to evaluate
the approximation points for the Kriging model. In
(Owatchaiphong, 2009), a design methodology is
presented for sizing a SRM. The proposed method
combines the use of genetic and fuzzy algorithms
together to simplify the design method. In (Balaji,
2011) Particle Swarm Optimization (PSO) based
design optimization of SRM has been presented.
Here The SRM design is formulated as multi
objective constrained optimization problem. The
objective functions for obtaining desired design are
maximization of average torque and minimization of
torque ripple with stator and rotor pole arc as design
variables. But all these optimisation are aimed to
optimise motors’ structural design.
Many researchers have applied both GA and PSO in
different fields of engineering e.g. In (Panda, 2007),
the authors have compared GA with PSO for
designing a TCSC based controller for power system
stability improvement.
In this present work we have applied PSO to search
for the optimal PI controller parameters as well as
firing angle and commutation angle of SRM drive
The performance of this optimization techniques in
terms of convergence rate, error minimization and
time complexity is good.
2 MATERIALS AND METHODS
2.1 Switched Reluctance Motor
The Reluctance Motor is an electric motor in which
torque is produced by the tendency of its moveable
part to move to a position where the inductance of
the excited winding is maximized or reluctance of
the winding is minimum. This motor has field coils
as of a DC Motor field winding for its Stator and no
coils or magnets in the Rotor. The rotor is aligned
whenever the diametrically opposite stator poles are
excited. In a magnetic circuit the rotating parts
prefer to come in minimum reluctance (maximum
inductance) position at the instance of excitation.
When two rotor poles are aligned with two stator
poles, another set of rotor poles will be out of
alignment with respect to another set of stator poles.
Hence by switching stator currents in a sequence, the
rotor is rotated.
(,)
(,) (,)
di dL i
VRiLi it
dt dt
(1)
2
1(,)
.
2
e
N
dL i
Ti
dt
(2)
eL
d
TT J B
dt
(3)
The SRM can be modeled using the following
system equations [(1)-(3)], where V, T
e
, T
L
are
applied voltage, electromagnetic torque and load
torque respectively. R and L are the resistance and
inductance of the stator per phase winding. J and B
are inertia constant and damping constants of the
machine. i is the current through the winding and
is the speed of the machine.
(,)
i
is the Stator
Inductance, which depends upon the rotor position
(fig 1) and also current in stator winding is a
function of both position and time, it is non-linear
and thus a simple equivalent circuit of SRM is not
possible. The inductance profile is curved at the top;
which causes high Torque ripples, speed
oscillations, increased audible noise and fatigue of
the shaft.
ICINCO2014-11thInternationalConferenceonInformaticsinControl,AutomationandRobotics
392