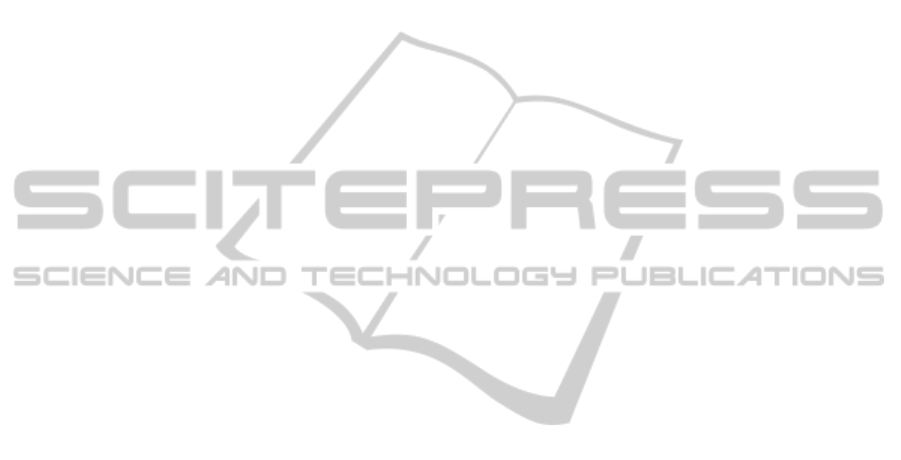
Repetition is performed with st. 3 with the only
difference being that at the boundaries of nodes , as
the boundary conditions are not acceptable uniform
parameter field , and the field is taken from the
calculation node connectivity . Repetition continue
as long as the parameters of the nodes on the borders
will not cease to change significantly. This means
that a stable equilibrium is attained at the boundaries
of nodes , i.e. mutual influence on each other node
set, in other words are found on the boundaries of
such parameters under which the correct modeling
nodes simultaneously on both sides of the border.
Upon completion of this phase of the simulation are
only GTE agreed gasdynamic parameters of
Upon
completion of this phase of the simulation are only
GTE agreed gasdynamic parameters of GTE. It
remains only to ensure proper connectivity modeling
capacity of the compressor and turbine, because they
are mounted on the same shaft , and this is achieved
by giving them equal speed. However, cases are
possible inequality of the compressor and the
turbine, for example, due to the increased heat of the
GTE in the case of the turbine generates more than
the compressor consumes the simulated speed. This
may occur as a consequence computational error
(excessive heat due to inaccurate calculation of
combustion processes), and because of invalid
mode, causing inconsistency really work sites
(Ivliev, 1977). For instance, if too high the amount
of fuel entering the combustion chamber, it is natural
for the turbine flows more energy. In the case of a
real experiment in this case the inequality works
turbine and compressor causes an increase in rotor
speed, increasing the energy consumed by the
compressor, turbine and reduction rotor speed at a
level ensuring consistency of work sites. However,
the settlement program does not automatically
change the speed of the rotor. Therefore, such a
process can be modeled by hand or using scripts
from performing the following sequence of actions:
1. Calculation GTE initial predetermined shaft
speed.
2. Analysis of the results, the definition of torque
difference compressor and turbine ΔM = Mt + Mc (
Mt and Mc are of opposite sign).
3. Depending on the sign ΔM predetermined
increase or decrease the rotor speed and repetition of
the algorithm to st.1 until ΔM decreases to a
predetermined level of error.
In the case of calculation of GTE on the mode
specified TK , such as takeoff or cruising , speed is
set and cannot be edited . In this case the
equalization moments can only be done by changing
the Mt by correcting the amount of fuel supplied to
the combustion chamber performed manually or by
using scripts on a similar algorithm. If the same
amount of fuel is also given ( eg on the conditions of
the experiment) , then because of the lack of degrees
of freedom of the rotor unbalance moments
unavoidably for this model is only a consequence of
computational error: incorrect definition of
resistance paths of the compressor and turbine , or
heat during combustion (eg in the experiment is
incomplete combustion. in this case, the mismatch of
the nodes can be eliminated only by a change
(specification) model: selection and correction
models of turbulence, combustion spray, etc.
2.4 The Problems of Matched Models
For modeling the engine needs to be linked
following parameters:
1) Fluid. In Numeca user can specify only a
single component of fluid. Therefore, the
compressor calculated on the pure air in the
combustion chamber Fluent - a mixture of air, fuel,
and products, and a turbine in Numeca - on the
working fluid with parameters (specific heat,
viscosity, etc.) of a mixture which has been obtained
at the output of the burner.
2) Transfer of parameter fields between elements
of GTE from one node to another is done by
averaging the parameters in the circumferential
direction. Application of the radial distribution of
the flow parameter in Fluent performed with User-
Define Functions (UDF). Each function reads from
the file allocation parameters adjustment channel
obtained from the calculation of the compressor and
turbine in Numeca. Then calculated the radius of the
center of each computational cell at the border and is
calculated corresponding to the radius parameter
using linear interpolation (Fig. 2).
2.4.1 Fluid
To calculate the flow in the turbine must set the
parameters of the working body. In this case the
turbine working fluid is a mixture of gases at the
outlet of the combustion chamber of the following
composition.
Accordingly, the main contribution to the
composition of the mixture produces four
components. Mixture parameters are calculated
according to the law of an ideal mixture:
С = ΣСi·mi
M = ΣMi·mi
R = ΣRi·mi
SIMULTECH2014-4thInternationalConferenceonSimulationandModelingMethodologies,Technologiesand
Applications
276